数控剃齿机检测的重要性与应用背景
数控剃齿机作为齿轮加工领域的核心设备,广泛应用于汽车、航空航天、精密机械等行业,其加工精度直接影响齿轮传动系统的性能和寿命。随着工业4.0的推进,对齿轮的精度要求日益严苛,例如新能源汽车的减速箱齿轮、机器人关节齿轮等均需达到微米级精度。为确保设备长期稳定运行并满足高精度加工需求,定期对数控剃齿机进行系统性检测与校准成为生产环节中不可或缺的步骤。通过科学的检测手段,能够及时发现设备误差、优化加工参数,从而避免批量质量事故,降低生产成本。
数控剃齿机核心检测项目
1. 几何精度检测
几何精度是剃齿机性能的基础,主要包含主轴径向跳动、轴向窜动、工作台平面度及导轨直线度等参数。检测时需使用激光干涉仪、电子水平仪等高精度仪器,依据ISO 230-2标准进行测量。例如,主轴径向跳动误差需控制在3μm以内,工作台平面度偏差应≤0.01mm/m,以确保齿轮齿形与齿向的加工一致性。
2. 运动精度检测
数控轴的运动精度直接影响齿轮分度误差与螺旋角精度,主要包括X/Y/Z轴的定位精度、重复定位精度以及多轴联动误差。采用球杆仪(Ballbar)进行圆度测试,结合数控系统自带的误差补偿功能,可有效校准反向间隙、螺距误差等关键参数。对于高精度机型,重复定位精度需达到±1.5μm以内。
3. 切削性能检测
通过模拟实际加工工况,检测剃齿刀与工件的啮合稳定性、切削力波动及表面粗糙度。使用动态力传感器监测切削力变化,结合三坐标测量机(CMM)对试切齿轮进行全尺寸分析,确保齿廓偏差(Fα)、齿向偏差(Fβ)等指标符合DIN 3962或AGMA 2015标准。典型要求为6级精度齿轮的Fα≤8μm,Fβ≤7μm。
4. 电气系统与温升检测
数控系统、伺服驱动及主轴电机的性能直接影响加工稳定性。需通过示波器检测电流波形谐波失真率,使用红外热像仪监测关键部件温升(如主轴轴承温度应<65℃)。此外,PLC逻辑响应时间、I/O信号延迟等参数需符合设备技术协议,避免因电气故障导致的加工异常。
5. 综合精度验证(试切法)
通过加工标准渐开线齿轮试件,利用齿轮测量中心进行全参数检测,综合验证设备整体性能。此方法可直观反映剃齿机在实际工况下的综合误差,包括周节累积误差(Fp)、齿距偏差(fpt)等核心指标。对于精密级剃齿机,Fp应≤12μm(模数2mm,直径100mm试件)。
检测周期与优化建议
建议每季度进行基础精度检测,每半年开展一次全面校准。对于24小时连续生产的设备,需增加切削性能动态监测频次。结合检测数据建立设备健康档案,利用AI算法预测磨损趋势,实施预防性维护。同时,建议采用环境恒温控制(20±1℃)和振动隔离基础,以减少外部干扰对检测结果的影响。
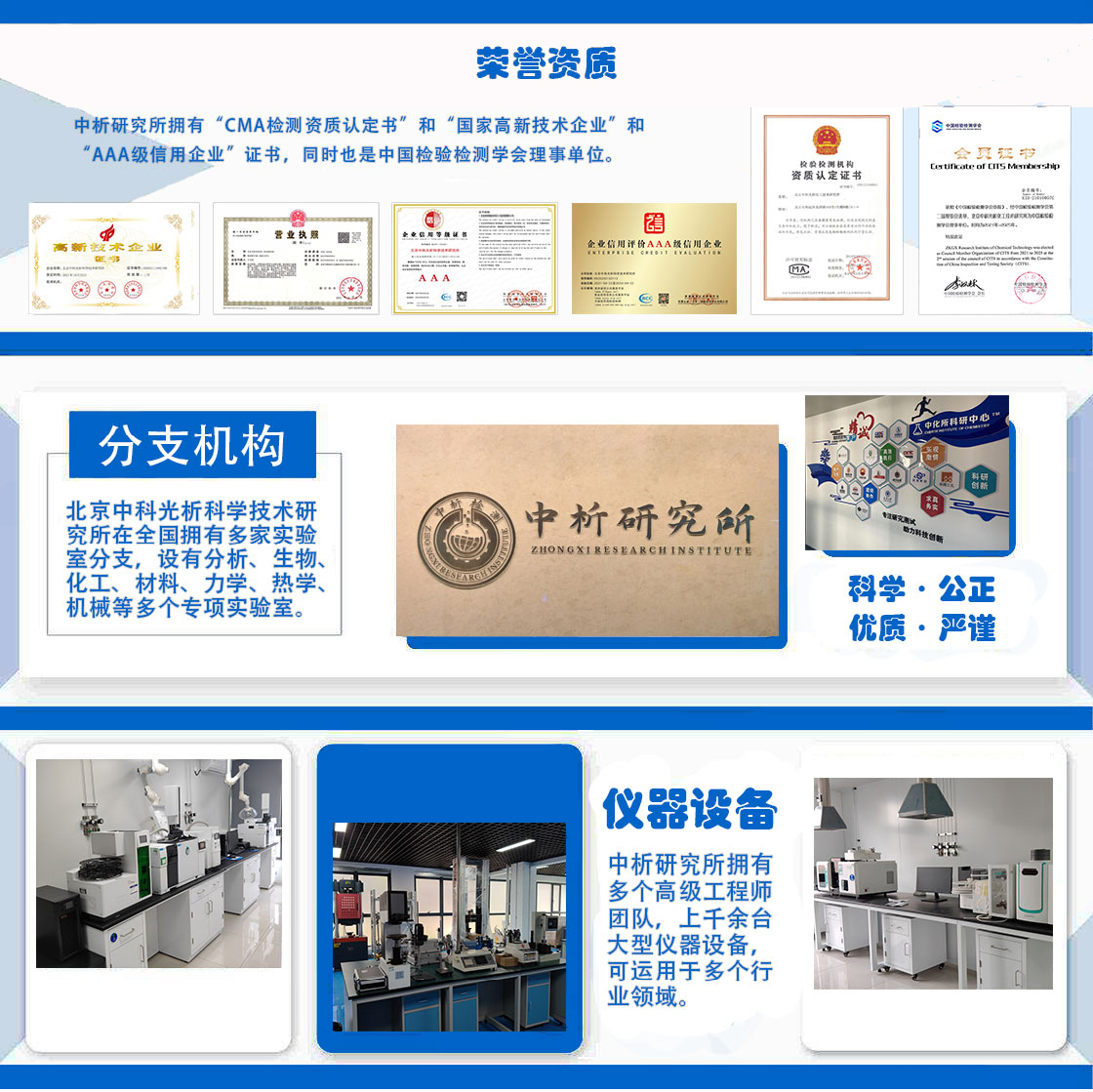
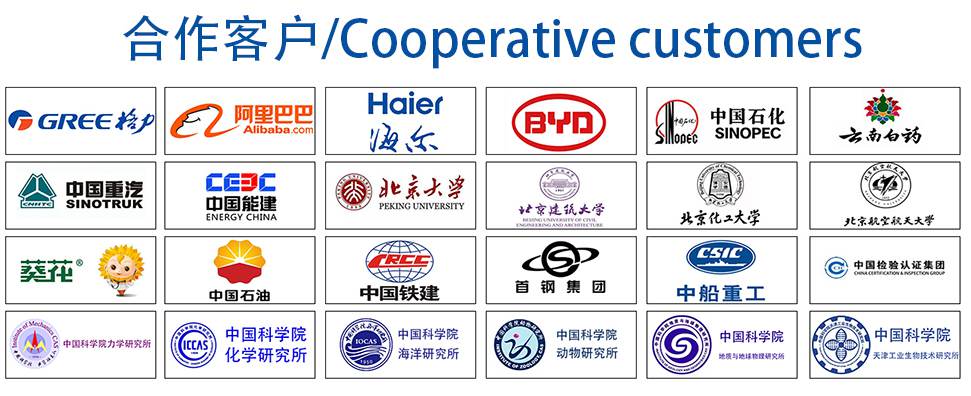