雕铣用电主轴检测的重要性与核心项目
作为精密雕铣加工设备的核心动力部件,电主轴的性能直接影响着加工精度、表面质量和生产效率。随着数控机床向高速化、高精度化发展,电主轴检测已成为设备维护与质量控制的关键环节。通过系统化检测可及时发现轴承磨损、转子失衡、温升异常等潜在问题,有效避免因主轴故障导致的工件报废、刀具损毁甚至设备停机,对保障连续生产具有显著的经济价值。
一、振动特性检测
使用振动分析仪测量主轴在空载和负载状态下的振动幅值,重点关注频率在100Hz-10kHz区间的振动分量。轴向振动应控制在0.8mm/s以内,径向振动不超过1.2mm/s。对于高精度加工场景,需采用激光多普勒测振仪实现非接触式纳米级振动测量。
二、温升性能测试
在额定转速连续运行2小时后,使用红外热像仪监测前后轴承座温升。优质电主轴温差应小于15℃,极限温升不超过55℃。重点检查冷却系统效能,水冷主轴需保证冷却液流量≥6L/min,油雾润滑系统油压需稳定在0.25-0.35MPa区间。
三、动态精度检测
采用动态主轴分析仪测量径向跳动和轴向窜动,30000rpm工况下径向跳动应≤3μm,轴向窜动≤2μm。高速动平衡测试要求残余不平衡量达到G1.0级标准,对于超精密加工设备需达到G0.4级平衡精度。
四、绝缘性能验证
使用500V兆欧表检测定子绕组对地绝缘电阻,冷态下应>100MΩ,热态下>50MΩ。耐压测试要求绕组与机壳间承受1500V/50Hz电压1分钟无击穿现象,漏电流<10mA。特别要注意冷却液渗入导致的绝缘劣化风险。
五、综合性能试验
在实际加工条件下进行切削力测试,监测功率波动不超过额定值的15%。通过表面粗糙度检测反向验证主轴性能,加工铝合金时Ra值应稳定在0.4-0.8μm区间。持续运行测试需累计500小时无异常磨损,轴承游隙变化量<5μm。
系统化的检测方案应包含日常点检、定期专业检测和故障后诊断三个层级,结合智能传感器与预测性维护系统,可实现电主轴全生命周期健康管理。企业建立完善的检测档案,可为设备选型、工艺优化提供数据支撑,显著提升精密加工核心竞争力。
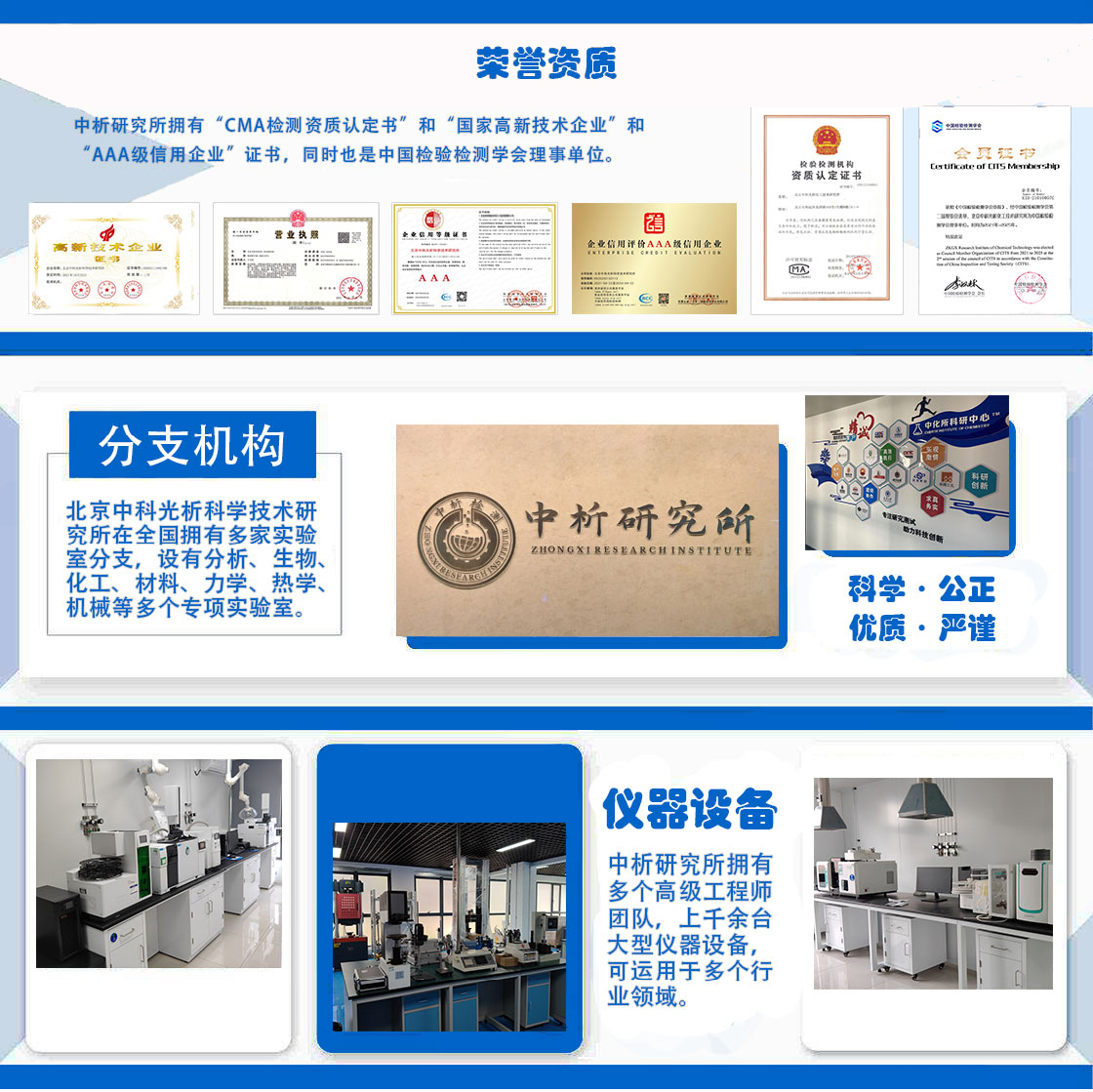
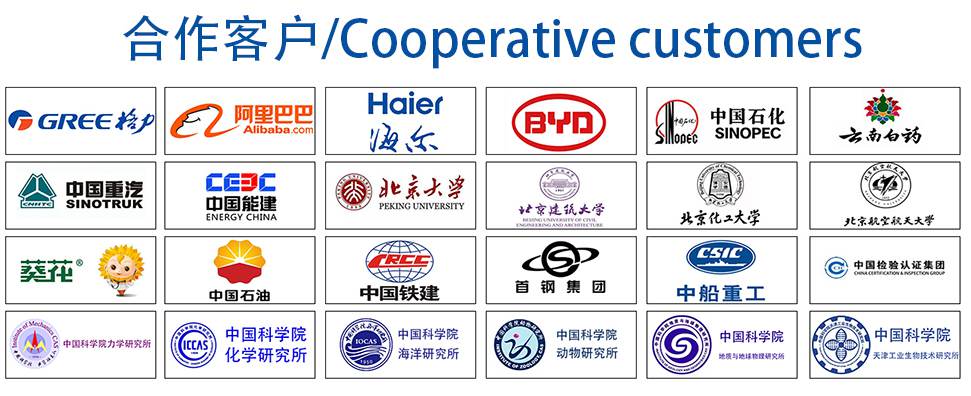