激光加工机检测的重要性与应用背景
激光加工机作为现代制造业的核心装备之一,广泛应用于金属切割、精密打标、焊接及3D打印等领域。其高精度、高效率的特性使其成为汽车、航空航天、电子等行业的首选加工设备。然而,激光设备性能的稳定性与加工质量直接相关,若参数偏移或部件损耗未被及时发现,可能导致产品报废、设备故障甚至安全隐患。因此,定期的激光加工机检测不仅是保障生产质量的必要环节,更是延长设备寿命、降低运维成本的关键措施。根据国家标准GB/T 18490-2018,激光加工设备的检测需覆盖光学系统、机械结构、电气控制等三大模块,涉及20余项关键指标。
核心检测项目及技术要点
1. 激光输出功率稳定性检测
使用激光功率计连续监测30分钟内的功率波动,要求工业级设备的功率偏差不超过±2%。重点检测激光器谐振腔的温度补偿功能,功率衰减超过5%需触发报警。此项检测可发现光学镜片污染、冷却系统异常等潜在问题。
2. 光束质量分析(M²值测量)
通过光束分析仪采集光斑直径、发散角等参数,计算M²因子。优质光纤激光器的M²值应小于1.3,二氧化碳激光器需控制在1.8以内。检测时需模拟实际工作距离,并评估不同功率下的光束模式稳定性。
3. 运动定位精度校准
使用激光干涉仪测量XYZ轴的定位精度,重复定位误差应≤5μm。特别要检测光路补偿系统的响应能力,当加工头移动速度达到60m/min时,焦点偏移量不得超过0.02mm。该指标直接影响异形工件的轮廓加工精度。
4. 冷却系统效能评估
记录冷却液温差(进口与出口差值)应稳定在2-4℃范围,流速波动不超过额定值的10%。通过红外热成像仪监测激光器外壳温度分布,异常热点可能预示散热器堵塞或制冷剂泄漏。
5. 安全防护系统验证
包括紧急停止响应时间(≤0.5秒)、防护罩联锁功能测试、激光泄漏量检测(需符合IEC 60825-1 Class 1要求)。需模拟突发断电、气体压力异常等工况,确保安全系统可靠动作。
6. 加工质量综合测试
采用标准试件进行实际加工,评估切割面粗糙度(Ra≤6.3μm)、熔渣残留量、切口锥度(≤0.5°)等指标。同时测试不同材料(不锈钢、铝合金、复合材料)的加工适应性,记录峰值功率波动曲线。
检测周期与设备维护建议
建议每500工作小时进行基础参数检测,2000小时开展全面校准。日常维护应重点关注光学镜片清洁度(每月检测透过率衰减)、导轨润滑状态(摩擦系数变化≤15%)、气体纯度(氧气含量<5ppm)。建立检测数据库,通过趋势分析预判激光器寿命,可降低70%以上非计划停机风险。
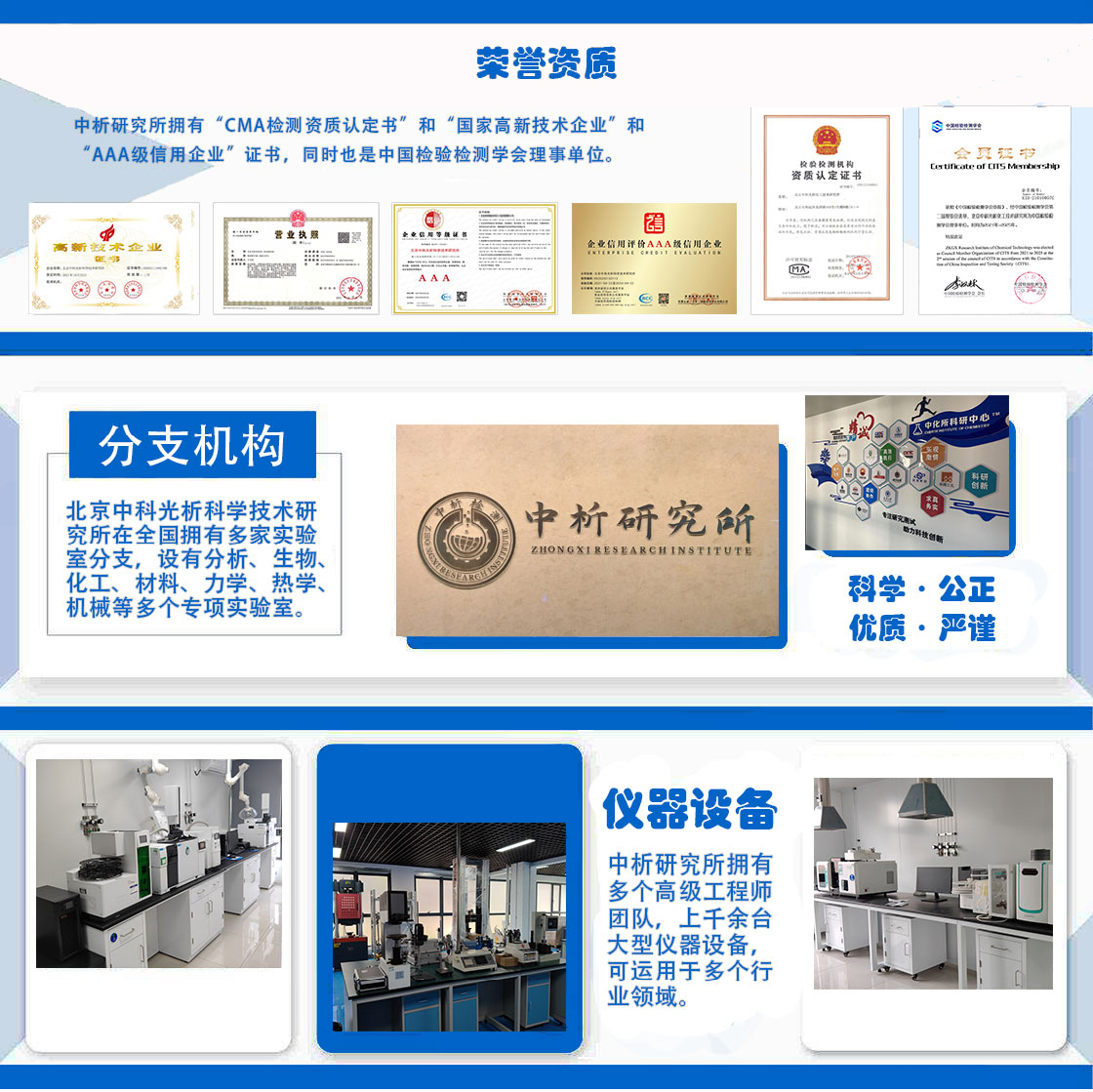
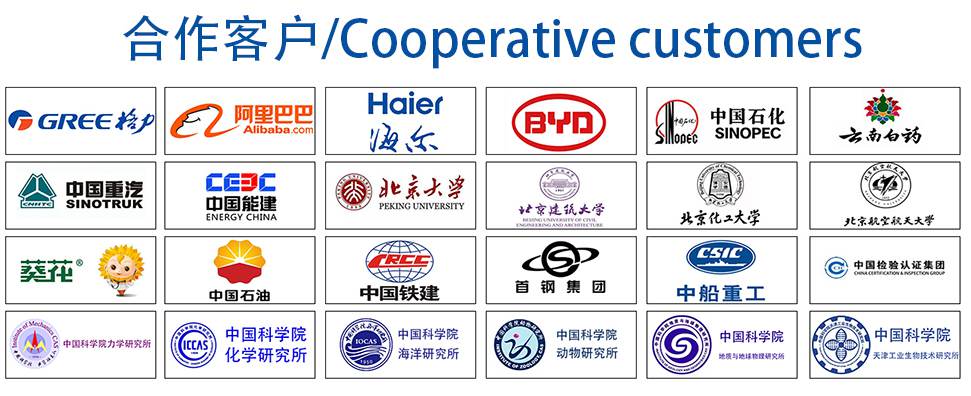