特殊用途电主轴检测
实验室拥有众多大型仪器及各类分析检测设备,研究所长期与各大企业、高校和科研院所保持合作伙伴关系,始终以科学研究为首任,以客户为中心,不断提高自身综合检测能力和水平,致力于成为全国科学材料研发领域服务平台。
立即咨询特殊用途电主轴检测的关键项目与技术要点
特殊用途电主轴作为高精度机电一体化设备的核心部件,广泛应用于航空航天、精密加工、半导体制造等领域。其性能直接决定设备的加工效率、精度及可靠性。与传统电主轴相比,特殊用途电主轴往往需要承受极端温度、高真空、强腐蚀或超高转速等特殊工况,因此对其检测提出了更严格的要求。检测过程需覆盖材料特性、动态性能、热稳定性、振动抑制能力等全方位指标,同时结合工况模拟测试验证其实际应用表现。
一、结构性能检测
1. 主轴轴向与径向跳动检测:采用非接触式激光位移传感器测量主轴的动态跳动量,精度需达到0.1μm级别。对于超高速电主轴(转速>50,000rpm),需在真空环境下进行测试以排除空气扰动影响。 2. 主轴刚度测试:通过施加径向及轴向载荷,结合应变片与位移传感器分析形变量,验证其静态与动态刚度是否符合ISO 10791-7标准。 3. 密封性能验证:针对防尘、防水或气密性要求的电主轴,使用氦质谱检漏仪进行泄漏率检测,确保防护等级达到IP68或更高标准。
二、电气性能检测
1. 绕组绝缘测试:采用5000V耐压测试仪检测定子绕组绝缘强度,同时测量绝缘电阻值(需>100MΩ/DC500V)。 2. 电磁兼容性(EMC)测试:依据IEC 61000标准进行传导干扰和辐射干扰测试,确保电主轴在复杂电磁环境中稳定运行。 3. 变频驱动匹配性验证:通过动态负载模拟系统测试电主轴在不同频率下的扭矩响应特性,验证驱动系统与控制算法的协同性能。
三、热特性与动态特性分析
1. 温升及热变形测试:利用红外热像仪监测连续运行下的温升曲线,配合激光干涉仪测量热致形变量,确保热平衡状态下精度损失不超过0.005mm。 2. 动态振动频谱分析:使用多通道振动测试系统采集主轴的振动加速度信号,通过FFT分析识别临界转速与共振点,优化动平衡等级至G0.4以下。 3. 润滑系统效能评估:针对油气润滑或微量润滑系统,测试润滑油膜形成状态与温升关系,验证润滑剂在极限转速下的抗烧结性能。
四、环境适应性专项测试
1. 高低温循环测试:将电主轴置于-40℃至150℃温度箱中进行200次冷热冲击测试,检测材料膨胀系数匹配性与轴承预紧力变化。 2. 防腐蚀性能检测:对表面涂层进行盐雾试验(ASTM B117标准),评估在含腐蚀性介质环境下的抗蚀能力。 3. 真空/高压环境验证:在模拟太空或深海环境的测试舱内,测试电主轴的气密性、散热效率及电磁干扰抑制能力。
五、寿命与可靠性验证
1. 加速寿命试验:通过3倍额定负载连续运行测试,结合威布尔分布模型预测平均无故障时间(MTBF),目标值需>20,000小时。 2. 启停冲击测试:模拟频繁启停工况(>10万次循环),检测轴承磨损量与配合面微动腐蚀情况。 3. 故障诊断与健康管理(PHM)验证:集成振动、温度、电流等多传感器数据,测试状态监测系统的故障预警准确率与剩余寿命预测误差。
特殊用途电主轴的检测需构建从材料级到系统级的完整验证体系,结合数字化检测平台实现全生命周期数据管理。通过上述多维度的检测项目,可有效保障电主轴在极端工况下的性能稳定性,为高端装备制造提供可靠的技术支撑。
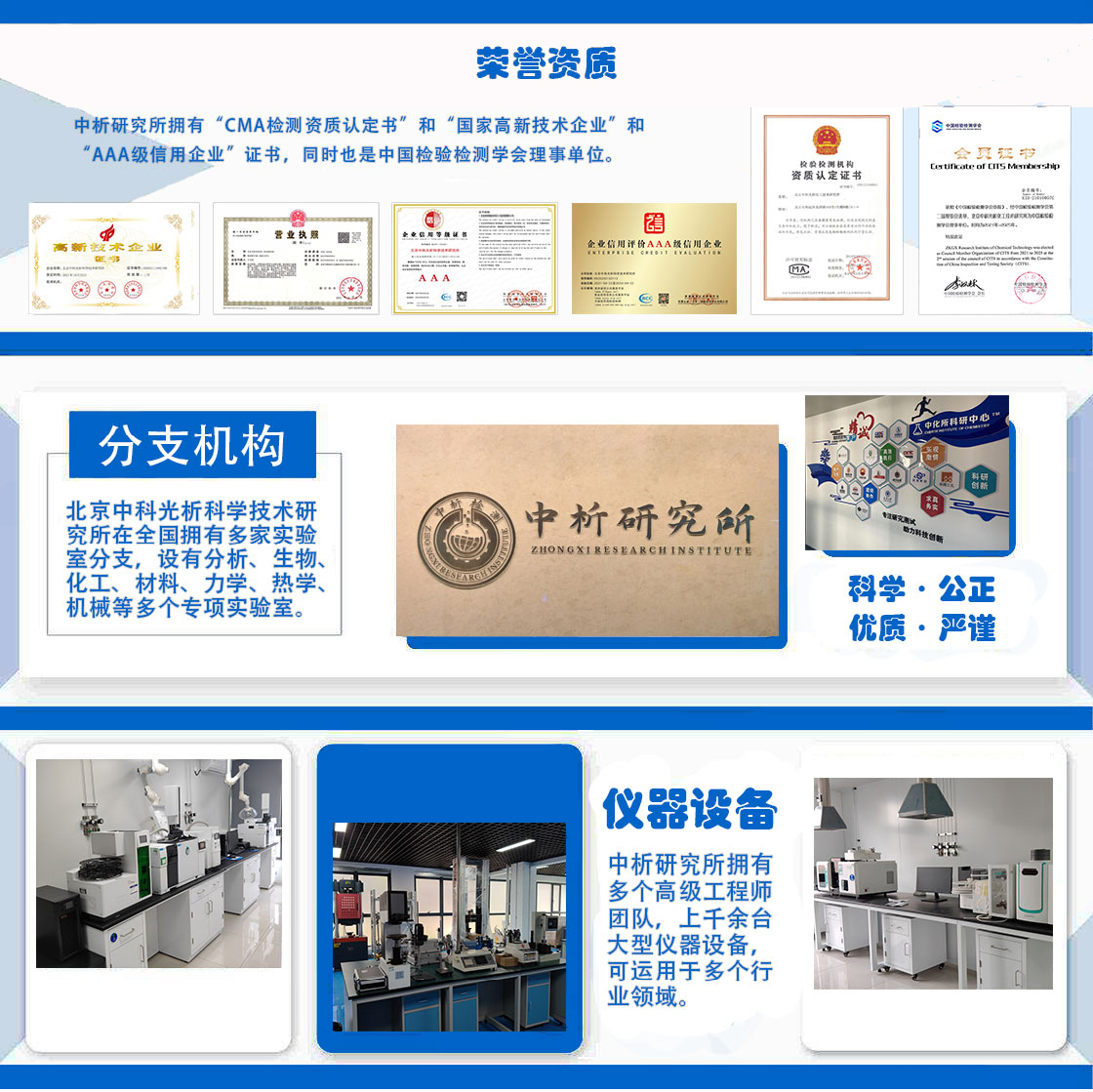
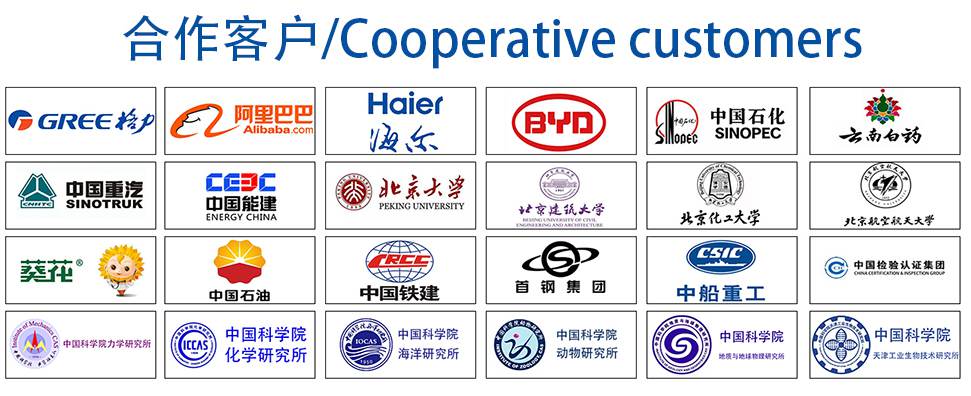