超/微滤水处理设备检测:技术与应用的关键环节
超滤(UF)和微滤(MF)技术作为现代水处理领域的核心工艺,凭借其高效分离、低能耗和广适性等优势,被广泛应用于饮用水净化、工业废水处理、医疗制药及食品加工等领域。然而,设备的长期稳定运行和过滤效果高度依赖科学严谨的检测流程。通过系统化的检测,能够精准评估设备性能、发现潜在隐患并优化工艺参数,从而确保水质达标、延长设备寿命并降低运维成本。本文将从超/微滤水处理设备的核心检测项目出发,解析其技术要点与行业标准。
一、膜组件性能检测
膜组件是超/微滤设备的核心部件,检测需覆盖物理完整性与通量表现。通过泡点法或压力衰减法验证膜丝无破损或泄漏;利用纯水通量测试评估膜污染程度及清洗效果;同时检测跨膜压差(TMP)与产水量,确保其符合设计指标(如膜孔径分布应稳定在0.01-0.1μm范围内)。
二、系统密封性检测
设备密封性直接影响截留效率与能耗。需对膜壳、管路连接处及阀门进行压力测试(通常为1.5倍工作压力保压30分钟),观察是否有渗漏或压降异常现象,并结合气密性检测仪量化泄露风险。
三、产水水质分析
根据目标水质标准(如GB 5749-2022生活饮用水卫生标准),对产水进行微生物(菌落总数、大肠杆菌)、浊度、悬浮物(SS)、颗粒物粒径分布及化学污染物(如TOC、重金属离子)的检测,验证超/微滤工艺对杂质的去除率是否达标。
四、系统运行参数校准
包括流量计精度校验、压力传感器灵敏度测试、反冲洗/化学清洗程序的时序与强度验证。例如,反冲洗频率是否匹配进水水质波动,化学清洗剂浓度(如次氯酸钠、柠檬酸)是否既能恢复通量又避免膜损伤。
五、材料兼容性检测
针对膜材料(如PVDF、PES)与接触介质的化学耐受性,需模拟极端工况进行耐酸碱、耐氧化剂及耐温性能测试,避免因材料腐蚀或溶胀导致膜结构失效。
六、自动化控制功能验证
检测PLC/SCADA系统的逻辑控制能力,包括故障报警(如压力骤升、流量异常)、自动清洗触发机制及数据记录完整性,确保设备在无人值守下的安全运行。
七、结构安全与稳定性评估
对设备支架、焊接部位及承压部件进行机械强度测试(如振动试验、疲劳试验),并检查电气系统的绝缘等级与接地保护,满足GB 5226.1等工业安全规范要求。
八、预处理与后处理单元联动检测
针对多级工艺系统(如超滤+反渗透),需验证预处理单元(如砂滤、活性炭)的过滤精度是否匹配膜组件的进水要求(SDI值<5),以及后处理单元的杀菌、调质装置是否有效保障终端水质。
九、环保与排放合规性检测
对浓水排放的污染物浓度(如COD、总氮)、废化学清洗剂的处理效果进行监测,确保符合《污水综合排放标准》(GB 8978),避免二次污染。
十、定期维护检测与寿命预测
建立周期性检测档案,通过历史数据对比分析膜通量衰减率、能耗变化趋势等,结合机器学习算法预测膜寿命,制定预防性更换计划,最大化设备经济价值。
通过上述多维度的检测技术体系,可全面保障超/微滤水处理设备的可靠性与工艺效能,为水质安全与资源化利用提供科学支撑。
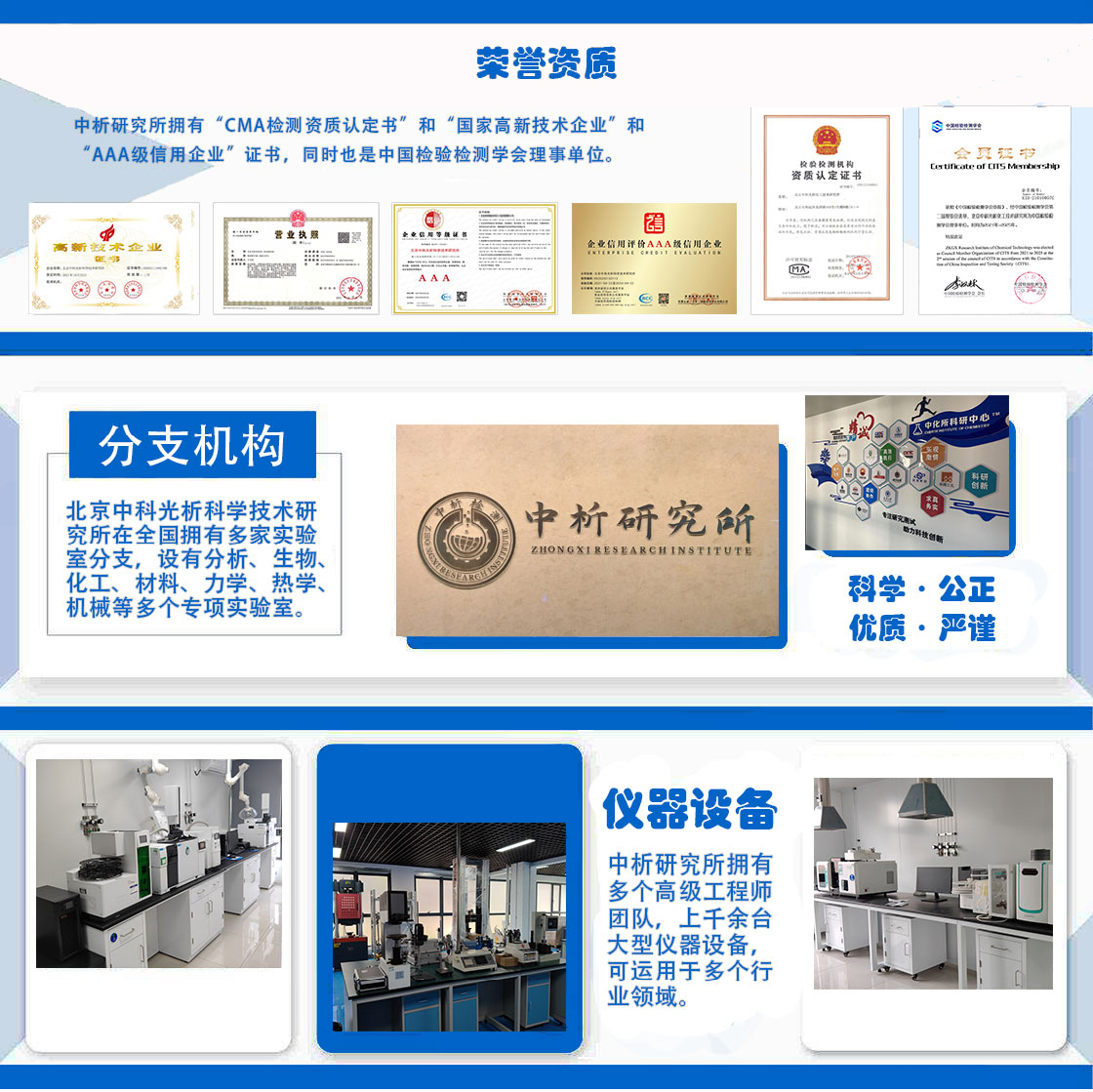
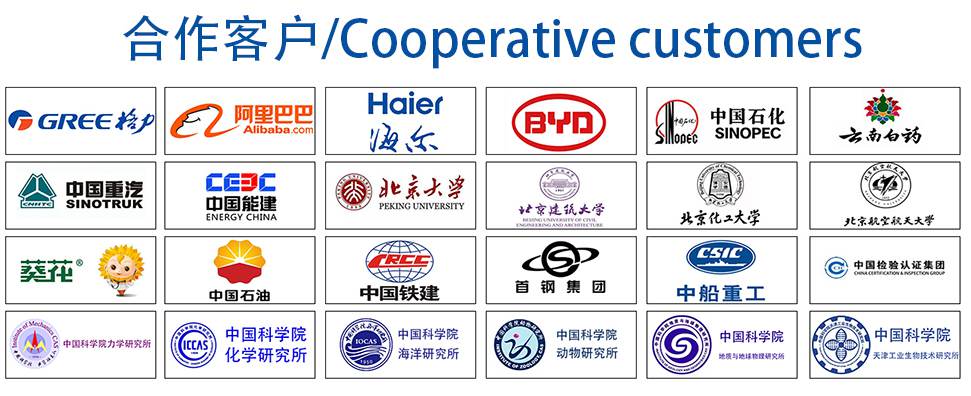