纳滤装置检测:核心项目与实施要点
纳滤装置作为一种高效的水处理技术,广泛应用于饮用水净化、工业废水处理、医药提纯等领域。其核心通过选择性分离膜对水中离子、有机物及微生物进行截留,实现物质的精细分离。为确保装置长期稳定运行、出水水质达标并延长膜元件寿命,定期开展系统性检测至关重要。纳滤装置检测需覆盖机械性能、分离效率、安全防护等维度,以下从关键检测项目展开详细说明。
一、产水性能检测
产水性能是评估纳滤装置效能的核心指标,包括:
1. 产水通量检测:通过流量计测量单位时间、单位膜面积产水量(L/m²·h),判断是否因膜污染或结垢导致通量衰减。
2. 脱盐率测试:使用电导率仪对比原水与产水的电导率差值,计算脱除率(通常需达到90%以上)。
3. 有机物截留率分析:针对特定污染物(如腐殖酸、农药残留等),采用UV254或TOC仪器检测截留效果。
二、膜元件完整性检测
膜完整性直接影响分离精度及运行成本,需重点检测:
1. 气泡观察法:向膜组件内注入压缩空气,浸入水中观察漏气点,定位破损膜丝位置。
2. 压力衰减测试:封闭产水端后加压至0.2-0.3MPa,监测5分钟内压降是否超过10%。
3. 荧光示踪法:向进水侧加入荧光素钠,通过产水荧光强度判断膜破损程度。
三、系统密封性检测
密封失效可能导致水质污染和能耗增加,检测内容包括:
1. 管路及接口气密性测试:使用氦质谱检漏仪或保压试验(保压30分钟压降≤5%)。
2. O型圈及密封垫状态检查:定期拆解观察老化、变形情况,测量压缩永久变形率。
3. 压力容器端盖密封检测:通过扭矩扳手验证紧固力是否符合设计值(通常200-300N·m)。
四、化学清洗效果评估
针对膜污染进行的化学清洗需验证有效性:
1. 清洗前后通量恢复率:对比清洗前后的标准化通量,目标恢复率≥95%。
2. 清洗废液成分分析:检测废液中的Ca²⁺、Fe³⁺、TOC浓度,评估污染物剥离效果。
3. 膜表面电镜扫描:采用SEM观察膜孔结构,确认无药剂结晶或二次污染。
五、自动化控制检测
现代纳滤系统集成PLC控制功能,需验证:
1. 压力传感器校准:对比现场仪表与标准压力表读数偏差(允许±1% FS)。
2. 自动反洗程序测试:模拟触发条件验证冲洗频率、时长、流量是否符合设定值。
3. 报警联锁功能:人为制造高压、低流量等异常工况,确认停机保护响应速度。
六、材料与结构安全性检测
定期开展设备本体检测可预防失效风险:
1. 膜壳耐压试验:按1.25倍设计压力进行水压试验,保压30分钟无渗漏。
2. 316L不锈钢部件检测:使用铁素体检测仪验证材质真实性,避免Cl⁻腐蚀风险。
3. 玻璃钢压力容器检测:通过超声测厚仪检查树脂层厚度,评估抗压强度衰减情况。
七、环境与安全防护检测
关注系统运行的环境影响与操作安全性:
1. 浓水排放合规性:检测COD、总氮、总磷等指标是否符合《污水综合排放标准》。
2. 化学药剂储存安全:检查酸碱储罐二次防漏装置、应急洗眼器配备情况。
3. 电气柜IP防护等级测试:验证防水防尘性能(通常要求IP54以上)。
通过以上检测项目的系统实施,可全面掌握纳滤装置的运行状态,及时识别膜污染、机械损伤、控制故障等隐患。建议建立季度常规检测与年度深度检测相结合的机制,同时结合在线监测数据实现预测性维护。检测过程中需严格遵循GB/T 31327-2014《纳滤膜元件检测方法》、HJ 579-2010《膜分离法污水处理工程技术规范》等行业标准,确保检测结果的准确性与可比性。
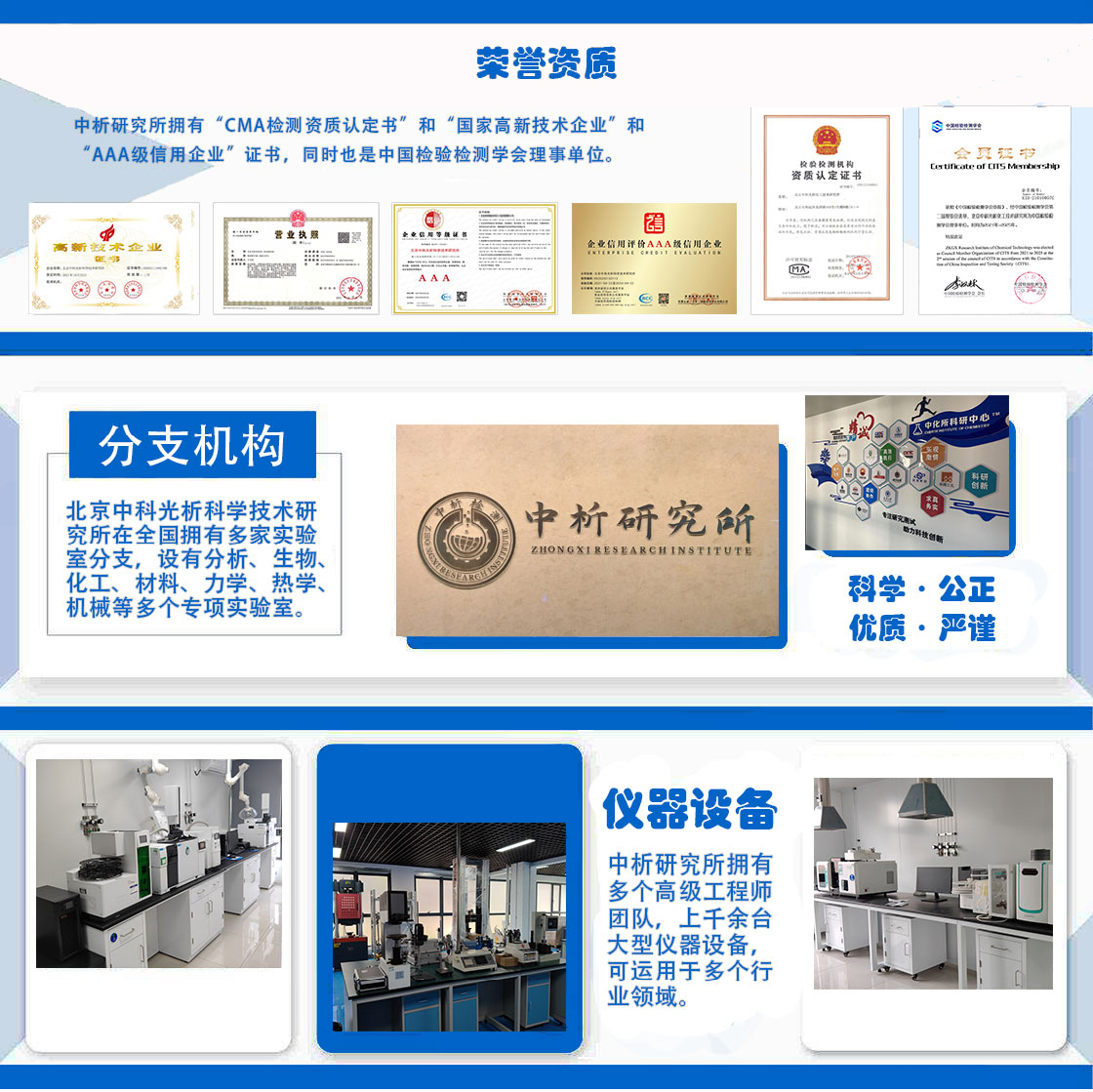
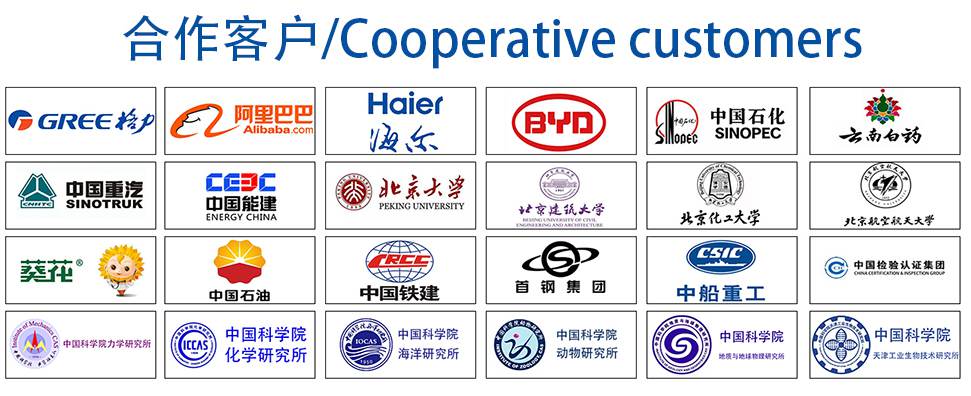