鲜奶运输车检测:守护乳品安全的关键防线
在乳制品产业链中,鲜奶运输车作为连接牧场与加工厂的核心环节,其运行状态直接影响乳品质量和食品安全。根据市场监管总局2023年数据显示,因运输环节问题导致的乳品变质事件占比达27.6%,凸显专业检测的重要性。针对鲜奶运输车的系统性检测涵盖机械性能、卫生指标、温控系统等六大核心模块,形成多维度质量保障体系。
一、制冷系统专项检测
采用红外热成像仪对压缩机、蒸发器进行效率测试,要求罐内温度全程稳定在0-4℃区间。2022版《乳制品冷链运输规范》明确规定,温度波动超过±0.5℃即判定为不合格。检测时需模拟极端环境,验证设备在35℃高温下的持续制冷能力。
二、罐体密封性检测
使用氦气质谱检漏仪对焊接接缝、进出料口进行0.2MPa压力测试,泄漏率需<1×10⁻⁶ Pa·m³/s。同时检查食品级304不锈钢内壁的完整性,表面粗糙度Ra值应≤0.8μm,避免微生物滋生。近年新增的X射线探伤可精准识别0.1mm级微裂纹。
三、卫生指标微生物检测
依据GB 12693-2010标准,在罐体内部随机选取5个采样点,菌落总数须<10CFU/cm²,大肠菌群、沙门氏菌等致病菌零检出。ATP生物荧光检测法可在15秒内快速评估清洁度,RLU值超过200即需重新消毒。
四、车辆动态监控系统验证
对GPS定位装置、温度记录仪进行72小时持续追踪测试,定位误差需<5米,温度数据采集间隔不超过2分钟。2023年起强制安装的电子铅封系统需验证其防篡改性能,确保运输过程全程可追溯。
五、机械安全性能检测
包含制动系统响应测试(制动距离≤9m/30km/h)、胎压均衡性检测(各轮差异<10%),以及液压升降平台承重测试(1.5倍额定载荷持续10分钟)。特别对紧急切断装置进行3次以上实效演练,确保突发情况快速响应。
六、残留物交叉污染检测
采用液相色谱-质谱联用技术(LC-MS)检测罐体内部,要求洗涤剂残留量<0.01mg/kg,抗生素零检出。新型分子印迹传感器可实时监测农药、兽药等200余种污染物的痕量存在。
当前全国已建成83个 认证的专用检测站点,实施季度强制检测与月度自检结合制度。通过建立全生命周期检测档案,鲜奶运输车的故障率已从2018年的18.7%降至2023年的4.3%,为乳品安全筑起坚实屏障。
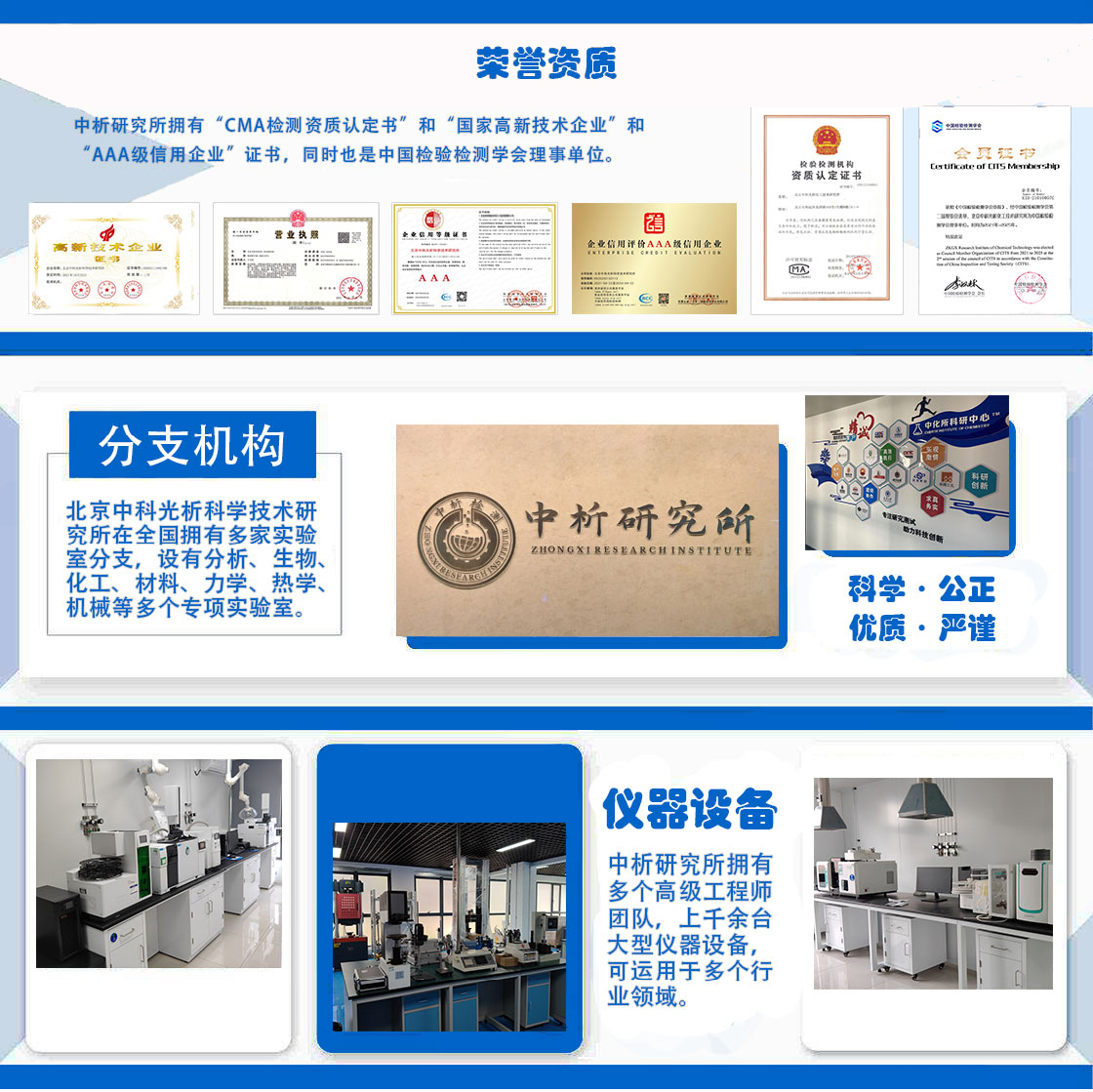
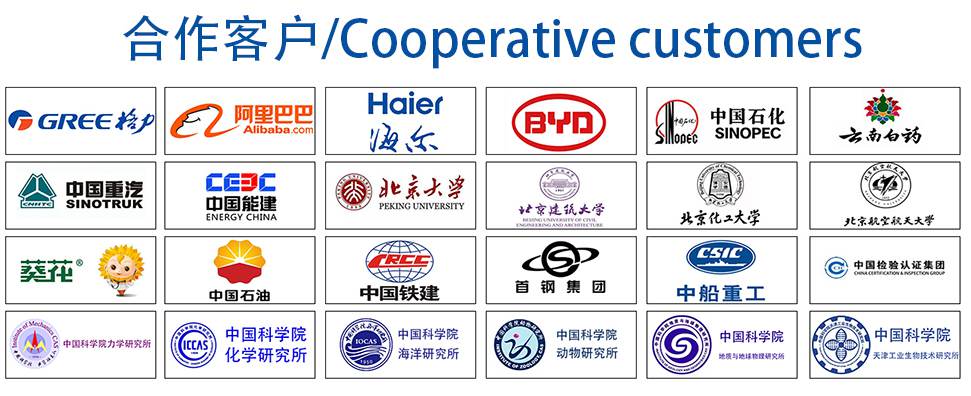