凿岩用硬质合金钎头检测技术解析
凿岩用硬质合金钎头作为矿山开采、隧道掘进等工程中的核心耗材,其性能直接关系到凿岩效率和工程成本。这类钎头通常由高强度合金钢基体与硬质合金刀片组成,需要在极端冲击载荷、高磨损和腐蚀环境下保持稳定性能。为确保产品质量符合GB/T 18376.3《硬质合金牌号》等行业标准,系统化的检测项目成为生产控制和技术验收的关键环节。
核心检测项目体系
完整的检测流程包含基础物理性能、几何参数、化学成分三大维度,通过以下重点项目构建质量控制网络:
1. 化学成分分析
采用直读光谱仪对基体材料进行元素检测,重点监控碳化钨(WC)含量、钴(Co)粘结相比例及杂质元素控制。钴含量波动需控制在±0.5%范围内,确保材料兼具硬度和韧性。同时使用X射线荧光光谱仪验证硬质合金刀片的成分稳定性。
2. 物理性能检测
配备洛氏硬度计(HRA标尺)对刀片进行多点硬度测试,典型值应达到88-92HRA。冲击韧性测试采用摆锤冲击试验机,试样规格为5×5×55mm无缺口标准件,要求冲击功不低于4J/cm²。金相显微镜下观察碳化物分布均匀性,晶粒度控制在1.5-2.5μm区间。
3. 几何参数测量
使用三坐标测量仪对刃部角度进行三维建模,前角误差需≤±1°,后角偏差控制±0.5°以内。内孔锥度采用气动量仪检测,锥度公差带应满足ISO 1718标准的4级精度要求。直径尺寸通过激光扫描仪实现高精度测量,重复性误差不超过0.02mm。
4. 表面质量评估
200倍电子显微镜下检查刀片焊接质量,要求钎缝结合率≥95%,无未焊透、夹渣等缺陷。表面粗糙度测试采用接触式轮廓仪,Ra值需≤0.8μm。磁粉探伤检测基体表层微裂纹,缺陷显示长度不得超过0.5mm。
5. 模拟工况测试
在液压脉冲试验台进行冲击疲劳试验,加载频率20Hz,冲击能量设定为30J,要求承受≥5×10⁵次冲击无破裂。耐磨性测试采用石英砂磨损试验,磨损量每小时不超过0.05mm³。盐雾试验箱模拟腐蚀环境,240小时试验后表面锈蚀面积需<3%。
通过上述多维度检测体系的实施,可有效保障钎头的破岩效率和使用寿命。检测数据的智能化采集与分析,更能为产品迭代升级提供数据支撑,推动硬质合金凿岩工具向高可靠性、长寿命方向发展。
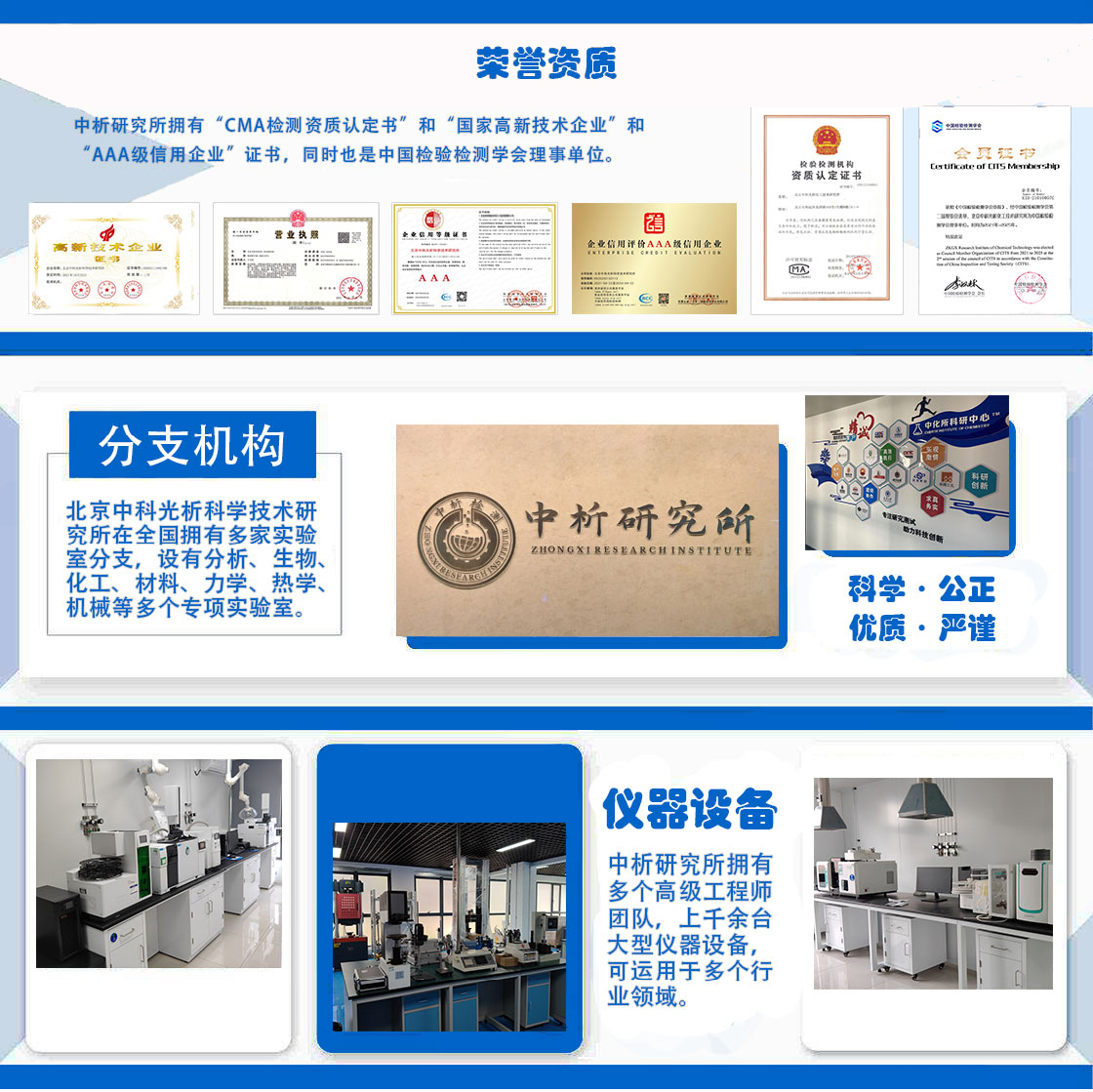
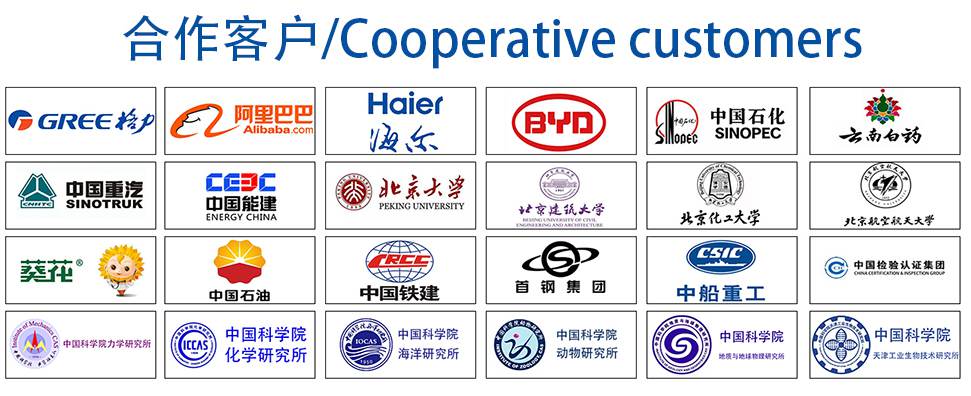