煤矿用电化学式氧气传感器检测
实验室拥有众多大型仪器及各类分析检测设备,研究所长期与各大企业、高校和科研院所保持合作伙伴关系,始终以科学研究为首任,以客户为中心,不断提高自身综合检测能力和水平,致力于成为全国科学材料研发领域服务平台。
立即咨询煤矿用电化学式氧气传感器检测的重要性及项目解析
在煤矿安全生产中,氧气浓度的实时监测是预防瓦斯爆炸、窒息事故的关键环节。电化学式氧气传感器因其高灵敏度、快速响应和稳定性,成为井下环境监测的核心设备之一。然而,煤矿环境具有高粉尘、高湿度、腐蚀性气体等复杂特性,传感器的性能可能因长期暴露而衰减。因此,定期对电化学式氧气传感器进行系统性检测,是保障监测数据可靠性、维护矿工生命安全的重要措施。
核心检测项目及技术要点
1. 传感器精度校准
通过标准气体(如20.9%氧气浓度的洁净空气)进行零点与满量程校准,检测传感器输出值与实际浓度的偏差。要求误差范围不超过±1%FS(满量程),若偏差超出阈值需进行电路补偿或更换敏感元件。
2. 响应时间测试
模拟氧气浓度从21%突降至18%的工况,记录传感器达到90%稳态值所需时间。煤矿用传感器要求响应时间≤30秒,确保突发环境变化时能及时触发报警系统。
3. 长期稳定性评估
连续运行传感器720小时(模拟一个月工况),监测输出信号的漂移量。合格标准为漂移值不超过±2%FS,同时分析电解液泄漏、电极老化等潜在失效模式。
4. 交叉敏感性验证
向传感器通入CO、CH4、H2S等煤矿常见干扰气体,检测其对氧气测量的影响。要求交叉干扰误差≤1%O2,避免瓦斯共存环境下出现误判。
5. 环境适应性检测
包括:
- 温度循环测试(-20℃~50℃)验证温漂特性;
- 湿度实验(95%RH,48小时)评估防潮性能;
- 粉尘防护测试(IP65等级)确保探头防堵塞能力。
6. 使用寿命预测
通过加速老化实验(如高温高湿环境)推算传感器寿命周期,煤矿场景下通常要求工作寿命≥2年,需结合电解液消耗速率与电极腐蚀数据进行综合判定。
检测流程标准化建议
建议采用三级检测机制:日常巡检(每班次零点校验)、月度功能性检测、年度全面标定。检测数据应接入煤矿安全监控系统,实现传感器健康状态的动态评估与预警。对于高瓦斯矿井,需将检测周期缩短至常规标准的70%,并增加抗冲击振动测试项目。
结语
电化学式氧气传感器的精准检测是煤矿安全链条中不可或缺的一环。通过建立完善的检测体系、采用智能诊断技术(如电化学阻抗谱分析),能够显著提升故障预警能力。建议企业结合《煤矿安全规程》GB 3836标准,制定个性化的传感器管理方案,为井下作业构筑可靠的生命保障防线。
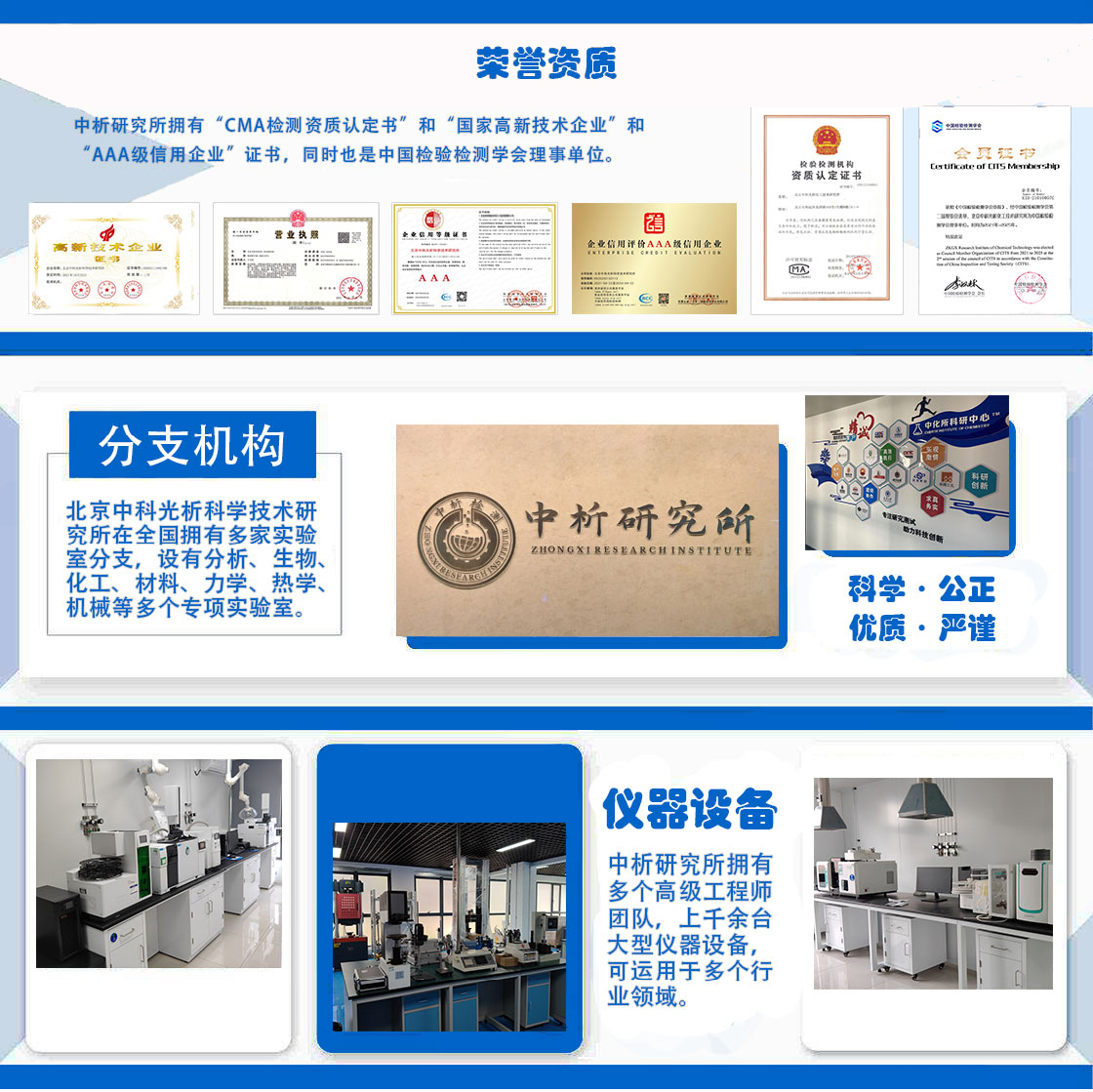
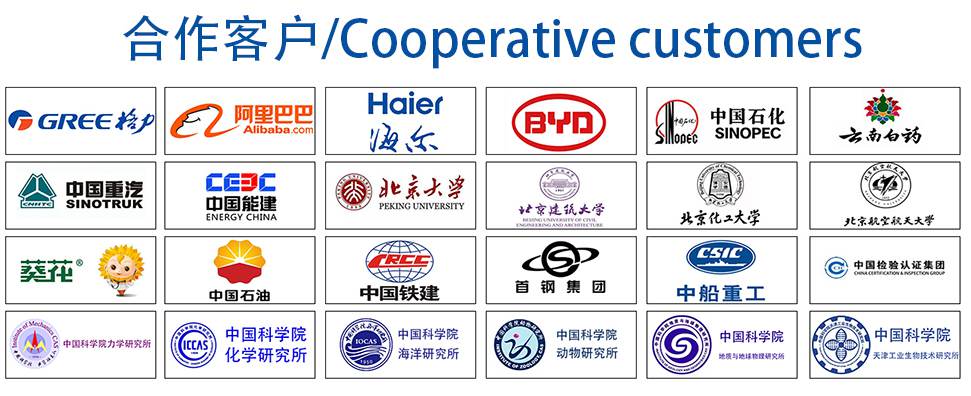