输油泵总成检测的重要性
输油泵总成作为燃油系统的核心部件,其性能直接关系到发动机供油的稳定性、燃油效率和设备安全性。在汽车、工程机械、船舶及发电机组等领域,输油泵总成的可靠性是保障动力系统正常运行的关键。通过系统化的检测,能够及时发现密封失效、磨损超标、压力异常等问题,避免因部件故障导致的停机损失或安全隐患。检测项目需覆盖物理性能、密封性、耐久性及电气特性等多个维度,同时需遵循行业标准(如ISO、SAE、GB/T等)和企业技术规范。
输油泵总成核心检测项目
1. 外观与尺寸检测
通过目视检查与精密测量工具(如三坐标仪、卡尺)验证壳体、连接法兰、密封面等部位的完整性。重点检测表面划痕、腐蚀、变形及关键安装尺寸公差(如泵体直径±0.05mm),确保与发动机的兼容性和装配精度。
2. 密封性能测试
采用气压/液压试验台模拟工作状态,分阶段施加0.3-1.2MPa压力,保持30分钟以上,监测泄漏量(要求≤0.5ml/min)。针对旋转轴封等动态密封部件,需进行1000次以上启停循环测试,并配合荧光检漏法定位微渗漏点。
3. 供油性能检测
在专用试验台架上,通过流量计和压力传感器测量不同转速(500-4000rpm)下的输出流量(误差≤±3%)和压力波动(≤±5%)。高温(120℃)与低温(-40℃)环境模拟测试可验证极端工况下的性能稳定性。
4. 电气系统检测
对电动输油泵的电机绕组进行绝缘电阻测试(≥100MΩ@500VDC)、耐压试验(1500VAC/60s无击穿),并验证ECU控制信号响应时间(<50ms)。集成式传感器需校验油位/压力信号的线性度(R²≥0.99)。
5. 耐久性试验
在加速寿命试验台连续运行500小时以上,监测关键参数衰减趋势。采用HAST(高加速应力试验)方法,在高温高湿(85℃/85%RH)环境下验证材料抗老化性能,评估橡胶密封件寿命周期。
6. 材料成分分析
通过光谱仪、金相显微镜对泵体材质(如ADC12铝合金)进行成分验证(Si含量11-13%),检查轴类零件的表面硬化层深度(HV0.3≥550,层深0.1-0.3mm),确保材料符合疲劳强度要求。
检测数据管理与追溯
现代检测需集成MES系统,对每台输油泵总成建立二维码电子档案,记录全生命周期检测数据(包括振动频谱、温度曲线等)。通过SPC统计分析关键参数CPK值,实现过程能力持续优化,并为召回提供数据支持。
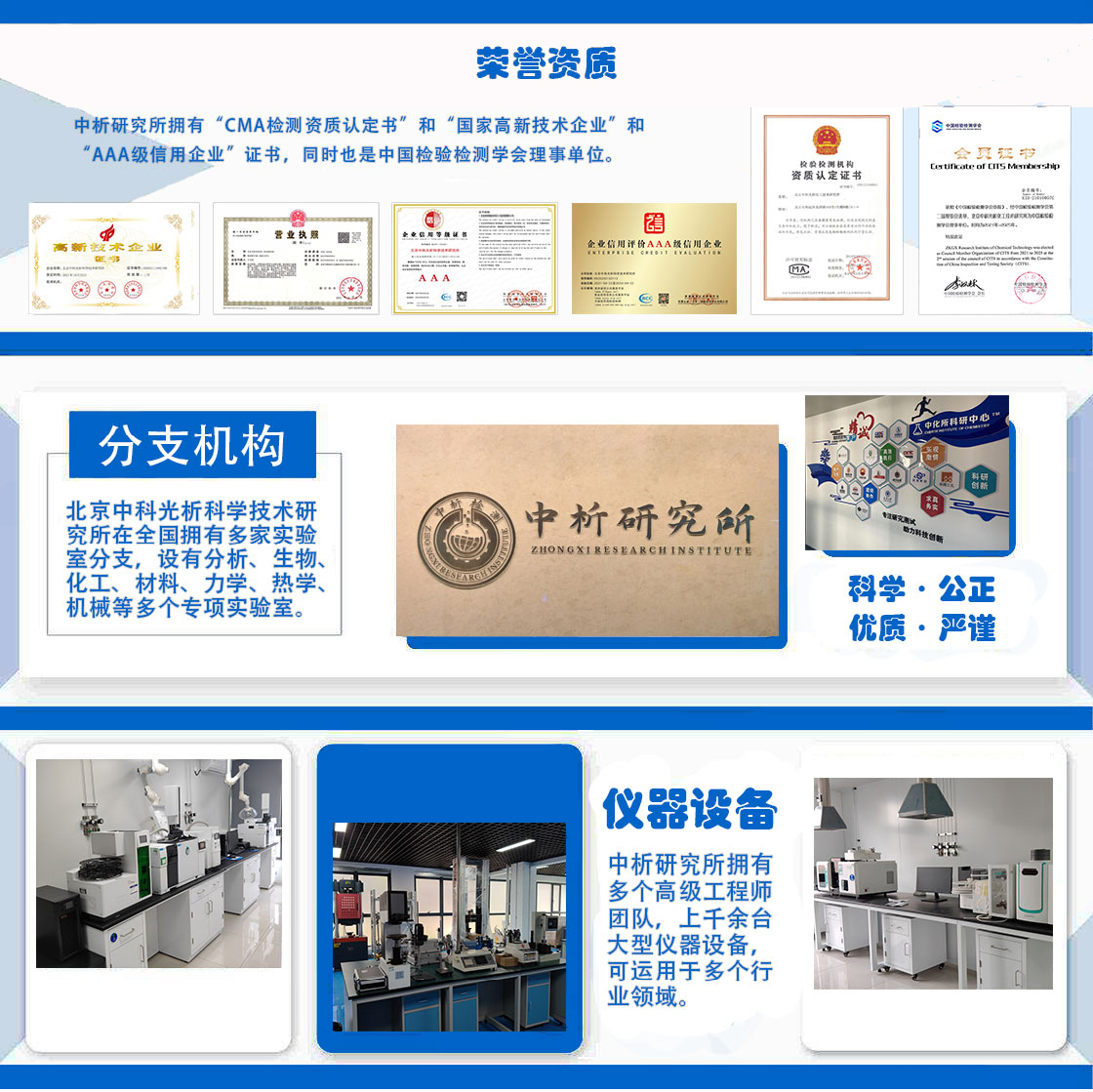
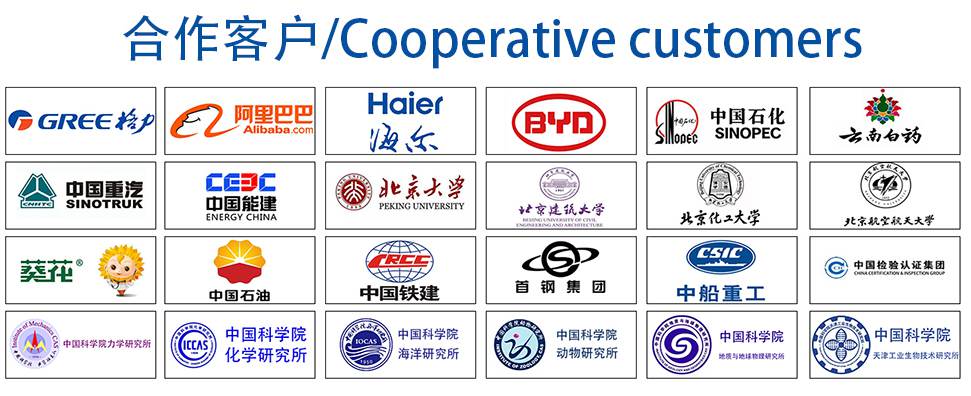