柴油机电控共轨系统高压供油泵总成检测的必要性与重要性
柴油机电控共轨系统作为现代柴油机的核心技术,其高压供油泵总成承担着为共轨系统提供稳定高压燃油的关键任务。随着排放法规的日益严格和发动机性能要求的提升,高压供油泵的精度、耐久性和可靠性直接影响着发动机的动力输出、燃油经济性及排放水平。在实际使用中,供油泵可能因机械磨损、密封失效、电磁阀故障或传感器信号异常等问题导致压力波动、燃油泄漏或供油不足等现象。因此,对高压供油泵总成的系统性检测不仅是故障诊断的核心环节,更是保障发动机高效运行和延长使用寿命的重要措施。
高压供油泵总成核心检测项目
1. 密封性能检测
通过液压试验台对高压油泵进行加压测试,检查泵体、柱塞偶件、进出油阀等关键部位的密封性。规范要求:在额定工作压力(通常1600-2000Bar)下保持3分钟,压力下降值需小于50Bar。若存在渗漏或压力快速衰减,需排查密封圈老化、柱塞磨损或阀座损伤等问题。
2. 供油压力与流量测试
使用专用检测设备模拟不同工况(如怠速、全负荷),测量供油泵的实时压力曲线和流量输出。需比对ECU设定值与实测值,偏差超过±5%时,需检查调压阀、流量控制阀及驱动机构状态。特别需关注压力波动是否在±20Bar范围内,异常波动可能反映柱塞弹簧疲劳或电磁阀响应延迟。
3. 电磁阀功能检测
通过示波器监测电磁阀驱动信号波形,结合电流检测判断线圈电阻(通常2-6Ω)和动作响应时间(≤2ms)。测试需覆盖高低压循环工况,观察阀芯运动是否卡滞,同时检测泄压通道的通畅性。常见的故障模式包括线圈短路、阀芯积碳或磨损导致的密封失效。
4. 传感器信号校验
对油泵内置的转速传感器、压力传感器进行信号采集与分析。转速信号需与曲轴信号同步,相位偏差不得超过2°;压力传感器的输出特性需符合线性度要求(误差<1%FS)。需特别注意高温工况下的信号漂移问题,必要时进行温度补偿测试。
辅助检测与预防性维护建议
1. 燃油清洁度检测
采集燃油样本进行颗粒物分析,要求污染物等级符合ISO 4406 18/16/13标准。颗粒物超标会加速柱塞偶件磨损,需同步检查燃油滤清器状态。
2. 振动与噪声分析
使用振动传感器检测泵体在2000-5000Hz频段的振动能量,异常峰值可能反映轴承损坏或齿轮啮合异常。运行噪声应低于85dB(A),尖锐异响常提示内部机械故障。
3. 预防性维护周期
建议每运行1000小时进行密封性能复检,每2000小时更换柱塞弹簧等易损件。长期停放设备需执行燃油系统防腐处理,避免精密部件锈蚀。
通过系统化的检测流程与数据化诊断,可精准定位高压供油泵总成的潜在故障,避免因供油系统失效导致的发动机停机风险,同时为优化燃油喷射控制策略提供数据支撑。
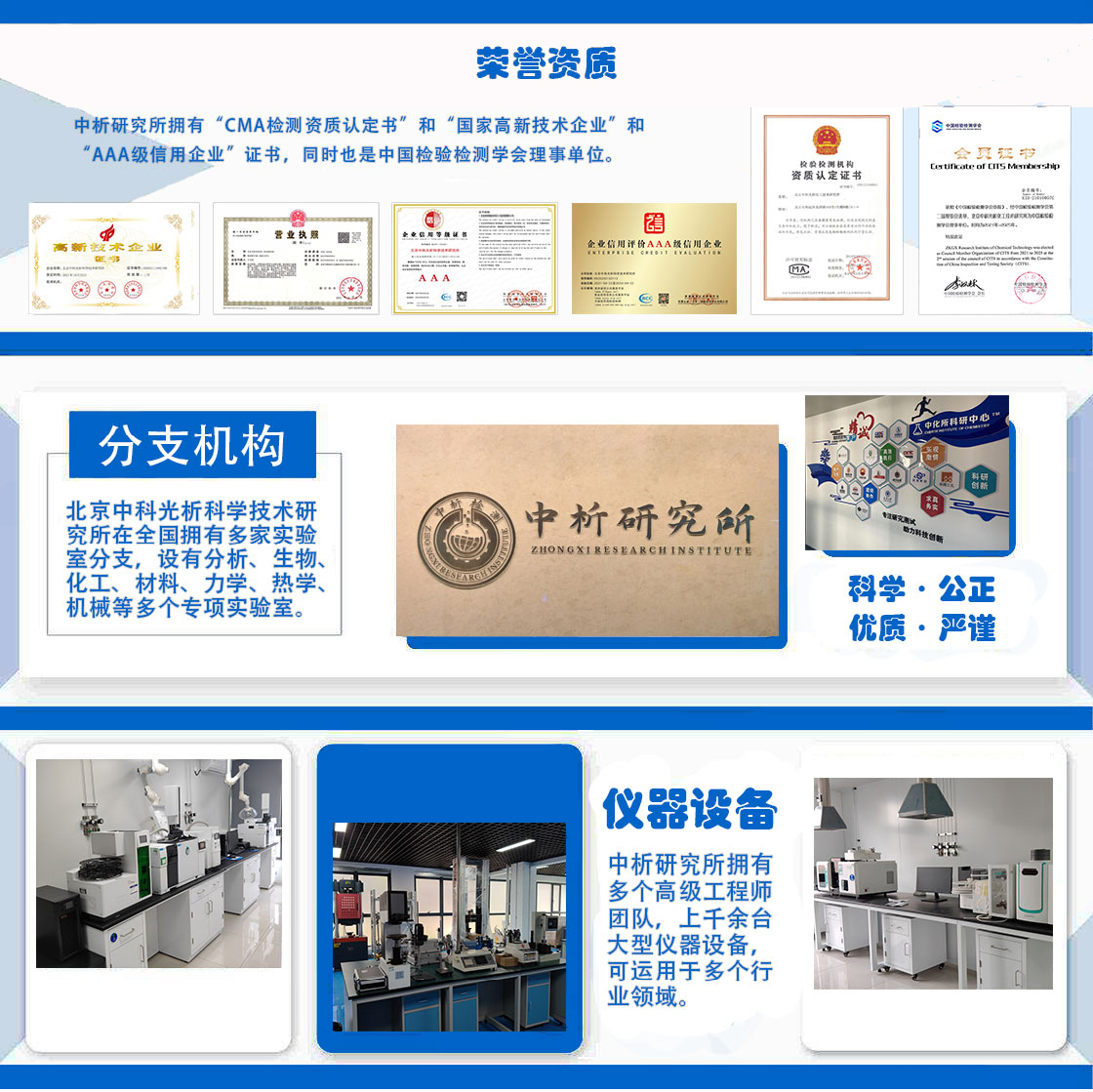
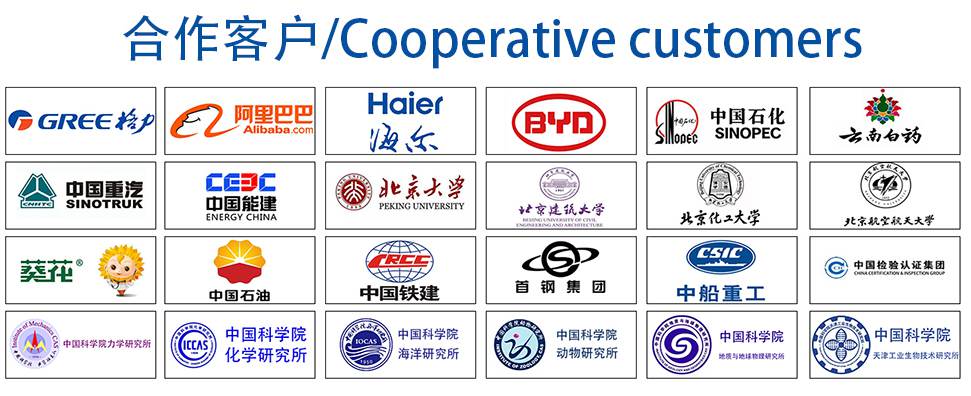