气体涡轮流量计检测的必要性及核心内容
气体涡轮流量计是一种广泛应用于石油、化工、天然气等领域的高精度流量测量仪表,其通过检测气体流经涡轮叶片时的旋转速度来计算流量。由于长期处于高压、高温、腐蚀性气体等复杂工况下,仪表的性能可能因机械磨损、零部件老化或环境干扰而逐渐下降,导致测量误差增大。因此,定期开展气体涡轮流量计的检测是保障生产安全、优化能源管理和满足计量法规要求的核心环节。
检测工作通常依据国家标准(如JJG 1037-2008《涡轮流量计检定规程》)及行业规范进行,涵盖从外观检查到动态性能验证的多维度项目。科学规范的检测不仅能发现潜在故障,还能通过校准提升仪表的长期稳定性与数据可靠性。
气体涡轮流量计核心检测项目
1. 外观及机械结构检查
检测人员需确认流量计外壳无变形、锈蚀或泄漏,涡轮叶片无损伤或异物卡阻。同时检查轴承磨损情况,旋转部件是否灵活平稳。对于带有信号输出接口的仪表,需验证电缆防护层完整性及接插件密封性能。
2. 示值误差检定
通过标准表法或容积法在多个流量点(如Qmax、0.5Qmax、Qmin)进行对比测试,计算示值误差是否在允许范围内(一般要求≤±1.5%)。测试时需控制气体压力、温度等参数,并记录重复性指标。
3. 压力损失测试
使用差压变送器测量流量计入口与出口的压差值,验证其是否符合制造商标称的压损曲线。异常压损可能预示流道堵塞或涡轮系统阻力异常。
4. 电磁兼容性(EMC)测试
模拟工业现场可能存在的电磁干扰(如变频器、大功率设备),检测流量计在强电磁场环境下的信号输出稳定性,确保脉冲信号或模拟信号无失真。
5. 环境适应性验证
包括温度循环试验(-20℃~+60℃)、振动试验(模拟管道振动)、防爆性能检测(适用于危险区域)等,评估仪表在极端工况下的运行可靠性。
6. 动态响应特性分析
通过阶跃流量变化测试,获取仪表的时间常数与响应延迟数据,验证其能否满足快速流量波动的测量需求。
检测注意事项与建议
检测前需确保流量计安装满足直管段要求(前10D后5D),气体介质清洁度符合标准。对于在线检测,应优先选择非介入式方法(如超声波比对)。建议每12-24个月进行一次全面检测,高负荷工况下需缩短周期。检测后应出具包含修正系数、不确定度分析的完整报告,为后续使用提供数据支持。
结语
气体涡轮流量计的检测是保障其计量性能的关键技术手段。通过系统化的检测项目组合,能够有效诊断仪表状态、预防故障风险,并为生产工艺优化提供精准的数据基础。企业应结合自身工况制定检测计划,并选择具备 资质的专业机构执行,从而最大化仪表的生命周期价值。
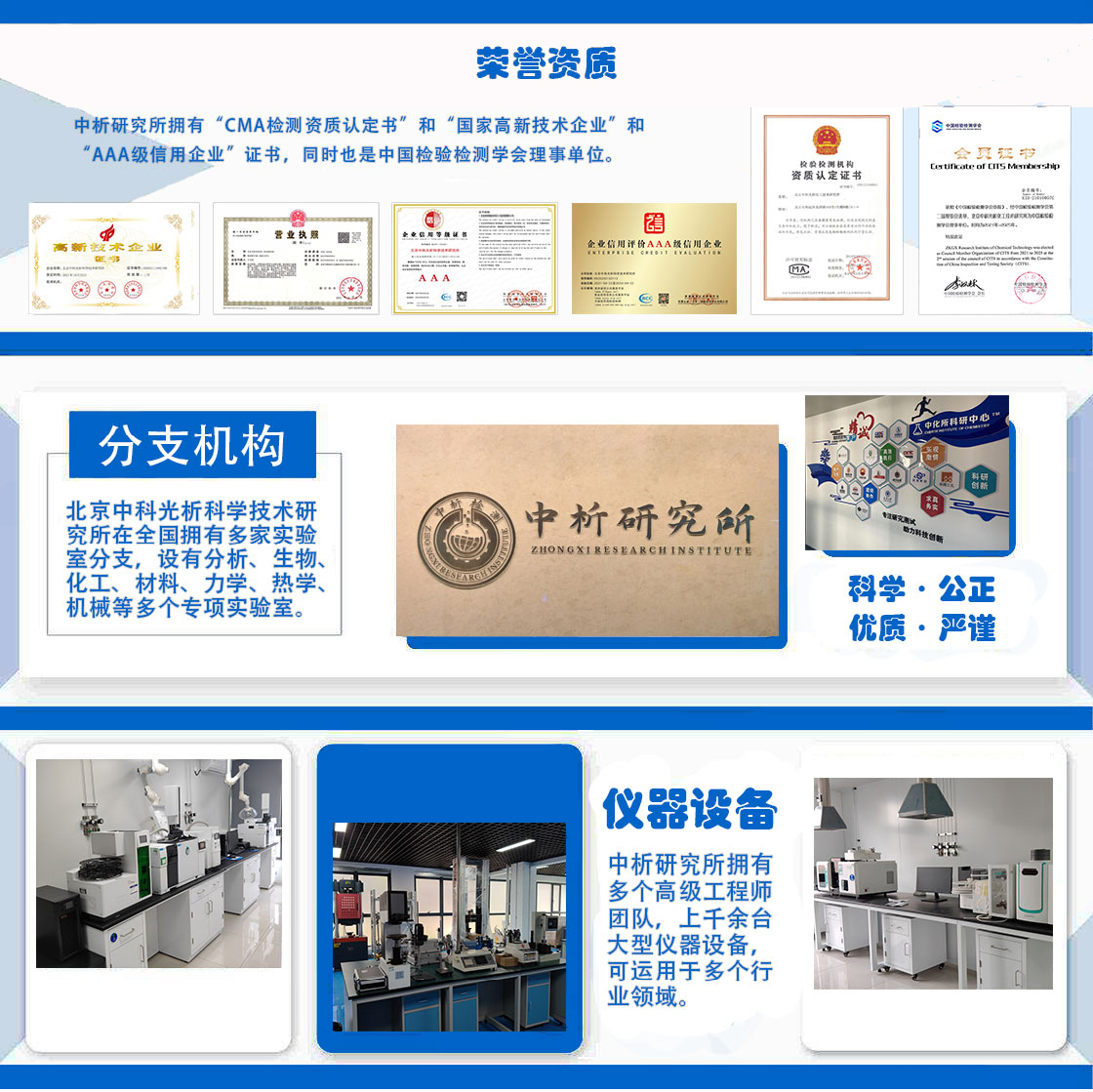
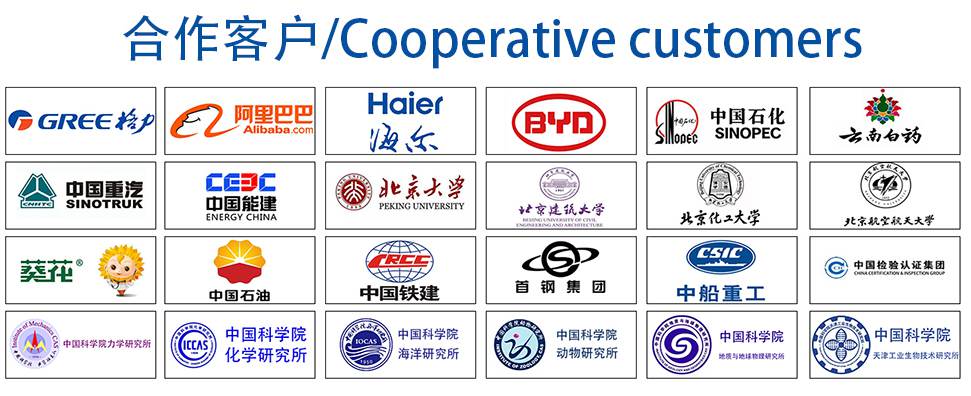