非金属燃油箱检测的重要性与核心项目解析
随着汽车轻量化与环保需求的提升,非金属燃油箱(如塑料或复合材料油箱)因其耐腐蚀、重量轻、设计灵活等优势,逐渐替代传统金属油箱成为主流选择。然而,燃油箱作为车辆燃油系统的核心部件,其安全性、密封性和耐久性直接关系到车辆运行安全和环境保护。因此,针对非金属燃油箱的检测成为汽车制造与零部件质量控制中不可或缺的环节。检测过程需覆盖材料性能、结构强度、环境适应性等多维度指标,以确保其符合国家标准(如GB/T 18354)及国际规范(如SAE J2578)。
关键检测项目及技术要求
1. 密封性测试
通过加压气体或液体检测燃油箱整体及连接部位的密封性,要求在规定压力下保持无渗漏。常见的测试方法包括气密性试验(压力保持法)和氦质谱检漏法,检测标准需参考ISO 12097-3。
2. 耐压与爆破强度检测
模拟油箱在极端压力下的承压能力,通过液压或气压试验测定其最大破裂压力,确保其能承受燃油系统工作压力及潜在冲击负荷。典型测试压力范围为0.03-0.15MPa,爆破压力需达到设计值的2倍以上。
3. 耐化学腐蚀性测试
将样品浸泡于不同浓度乙醇汽油、柴油或生物燃料中,评估材料溶胀、硬度变化及机械性能衰减情况。测试周期通常为1000小时以上,质量损失率需控制在5%以内。
4. 温度循环与冲击试验
通过高低温交变(-40℃至80℃)模拟极端气候环境,验证油箱材料的耐热老化性能及焊缝/接头的抗疲劳能力,要求完成500次循环后无裂纹或变形。
5. 振动与机械冲击测试
在振动台上模拟车辆行驶中的高频振动与道路冲击,检测油箱固定支架、连接管路等部位的抗振性能,持续振动时间不少于8小时,振幅需覆盖实际工况频谱范围。
6. 燃油渗透性检测
采用重量法或气相色谱法测定燃油箱对碳氢化合物的渗透率,要求满足国六标准(≤20mg/24h)或更严格的零蒸发排放(ZEV)要求。
检测设备与技术创新
现代检测体系中,红外热成像、三维数字图像相关(DIC)技术、有限元仿真分析等齐全手段被广泛应用。例如,DIC技术可实时监测油箱在压力载荷下的全场应变分布,而X射线断层扫描(CT)能无损检测内部结构缺陷。这些技术的结合显著提升了检测效率与结果可靠性。
总结
非金属燃油箱检测是保障车辆安全与环保合规的核心环节,需构建涵盖材料、结构、环境等多维度的检测体系。随着新能源汽车与混动技术的发展,检测标准将持续升级,推动行业向更高安全性与可持续性方向迈进。
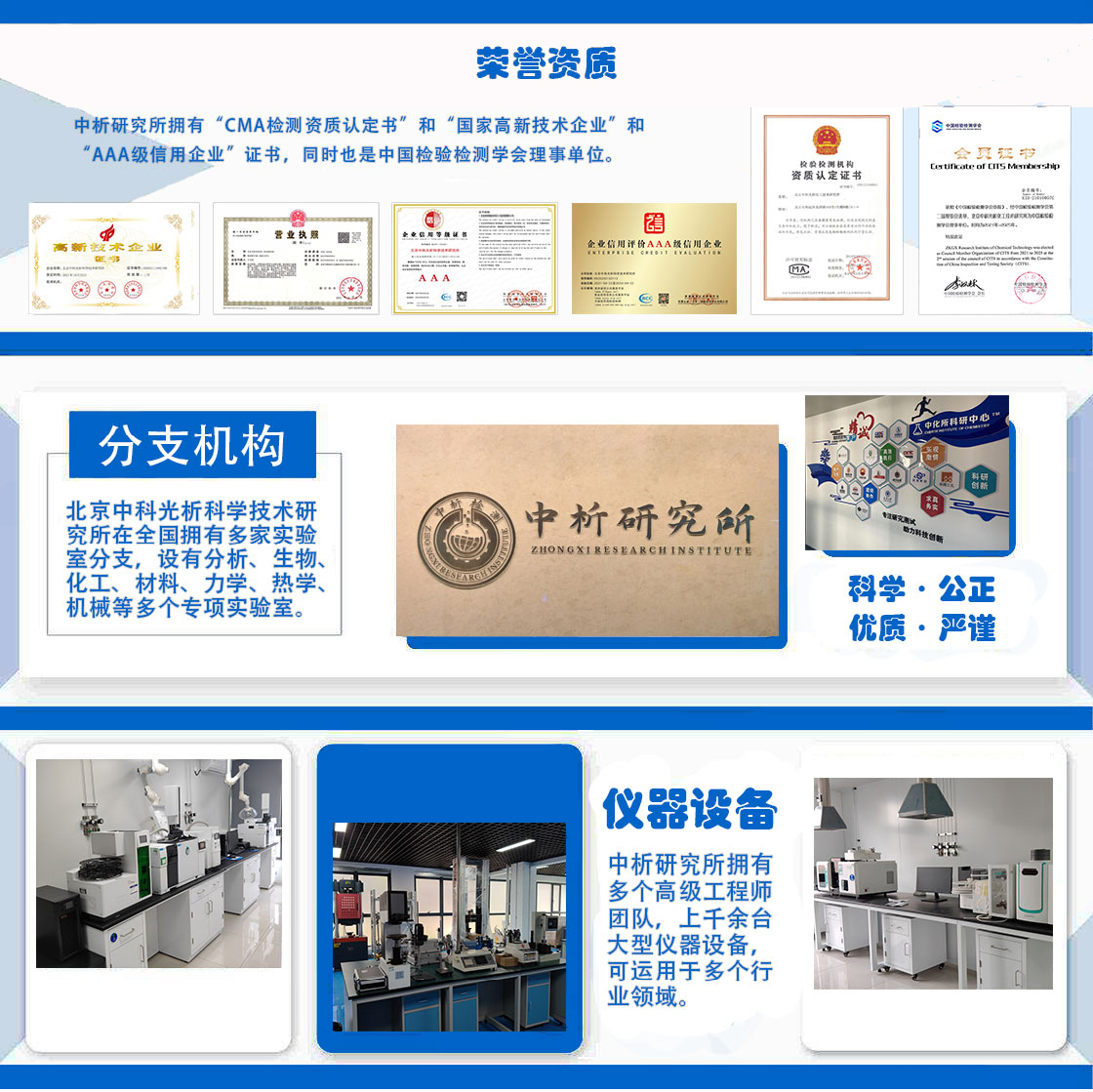
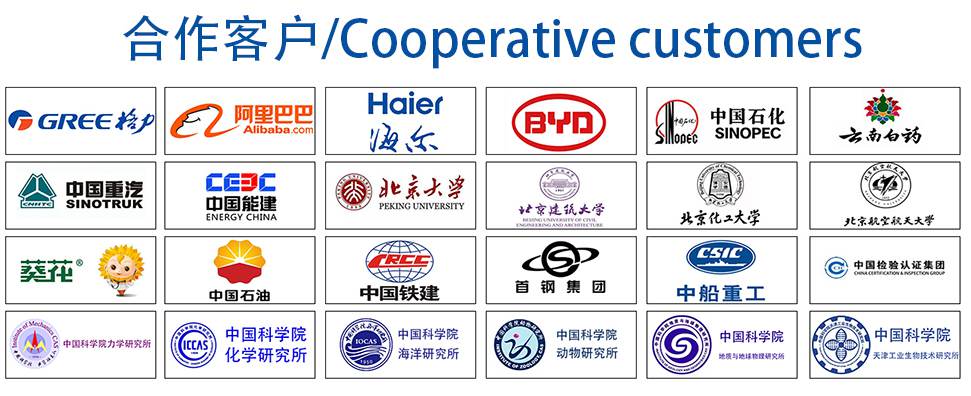