商用车空气悬架用空气弹簧橡胶气囊技术规范检测概述
空气弹簧橡胶气囊作为商用车空气悬架系统的核心部件,其性能直接影响车辆的行驶安全性、乘坐舒适性及使用寿命。橡胶气囊需在复杂工况下承受动态载荷、温度变化和化学腐蚀等因素,因此需通过严格的技术规范检测,确保其力学性能、密封性、耐久性及环境适应性符合行业标准。目前,国际上主流的检测标准包括ISO 1431(耐臭氧老化试验)、GB/T 20028(橡胶制品静态性能测试)以及行业专用的QC/T 791-2020《汽车空气悬架用空气弹簧技术条件》,这些标准为气囊的研发、生产及质量管控提供了科学依据。
针对商用车空气悬架的特殊需求,技术规范检测需覆盖从原材料到成品的全流程,重点关注橡胶材料的抗疲劳特性、气囊结构设计的合理性,以及装配后的系统协调性。检测项目通常分为静态性能测试、动态疲劳试验、环境模拟试验和功能性验证四大类,下文将详细解析关键检测内容。
关键检测项目及技术要求
1. 静态力学性能检测
静态性能是气囊承载能力的基础指标,包括拉伸强度、断裂伸长率、硬度(邵氏A型)及压缩永久变形率等。检测时需模拟气囊在不同充气压力(0.3-0.8MPa)下的形变状态,要求拉伸强度≥18MPa,断裂伸长率≥400%,压缩永久变形率≤20%(70℃×24h条件下)。同时需验证气囊的刚度曲线是否与悬架系统匹配,避免因刚度突变引发车辆振动。
2. 动态疲劳寿命试验
动态疲劳测试模拟车辆行驶中的高频振动和载荷变化,通过液压伺服试验机对气囊施加周期性压缩-拉伸载荷(频率2-3Hz,振幅±20mm)。根据QC/T 791标准,商用车气囊需通过≥50万次循环试验,试验后气囊外观无裂纹、分层,气密性保持率≥95%。对于高负荷工况的牵引车或工程车辆,部分企业要求疲劳寿命达到100万次以上。
3. 气密性与耐压性检测
气密性是空气弹簧的核心功能指标,检测包括静态保压试验和动态泄漏率测试。静态试验要求气囊在1.2倍额定工作压力下保压30分钟,压降≤5%;动态试验则在交变载荷下监测气压波动,泄漏率需≤0.2kPa/min。耐压测试需验证气囊在极限压力(≥2.5MPa)下的抗爆裂能力,确保无结构性破坏。
4. 环境适应性试验
橡胶材料的耐候性直接影响气囊的长期可靠性,检测项目涵盖: - 高低温交变试验:-40℃至+80℃循环100次,气囊无硬化、龟裂; - 耐臭氧老化:50pphm臭氧浓度下暴露96h,表面无可见裂纹; - 耐介质腐蚀:浸泡于柴油、润滑油等介质48h后,体积膨胀率≤10%。 部分严苛工况还需模拟盐雾腐蚀(500h)与砂石冲击试验,验证防护层的耐久性。
5. 尺寸与装配匹配性检测
通过三维扫描或激光测量仪对气囊的安装孔径、法兰平面度及总成高度进行精密检测,公差需控制在±1.5mm以内。装配测试需验证气囊与减震器、导向臂等部件的匹配性,确保无干涉且动态运动轨迹符合设计要求。
检测设备与质量控制体系
规范的检测需依托专业设备,包括多通道疲劳试验机、高低温湿热试验箱、臭氧老化箱及激光泄漏检测仪等。企业需建立从原材料进厂(如橡胶配方硫化曲线检测)到成品出厂的全流程质量追溯体系,并结合有限元分析(FEA)优化气囊结构设计,以满足商用车对高载荷、长寿命的严苛需求。
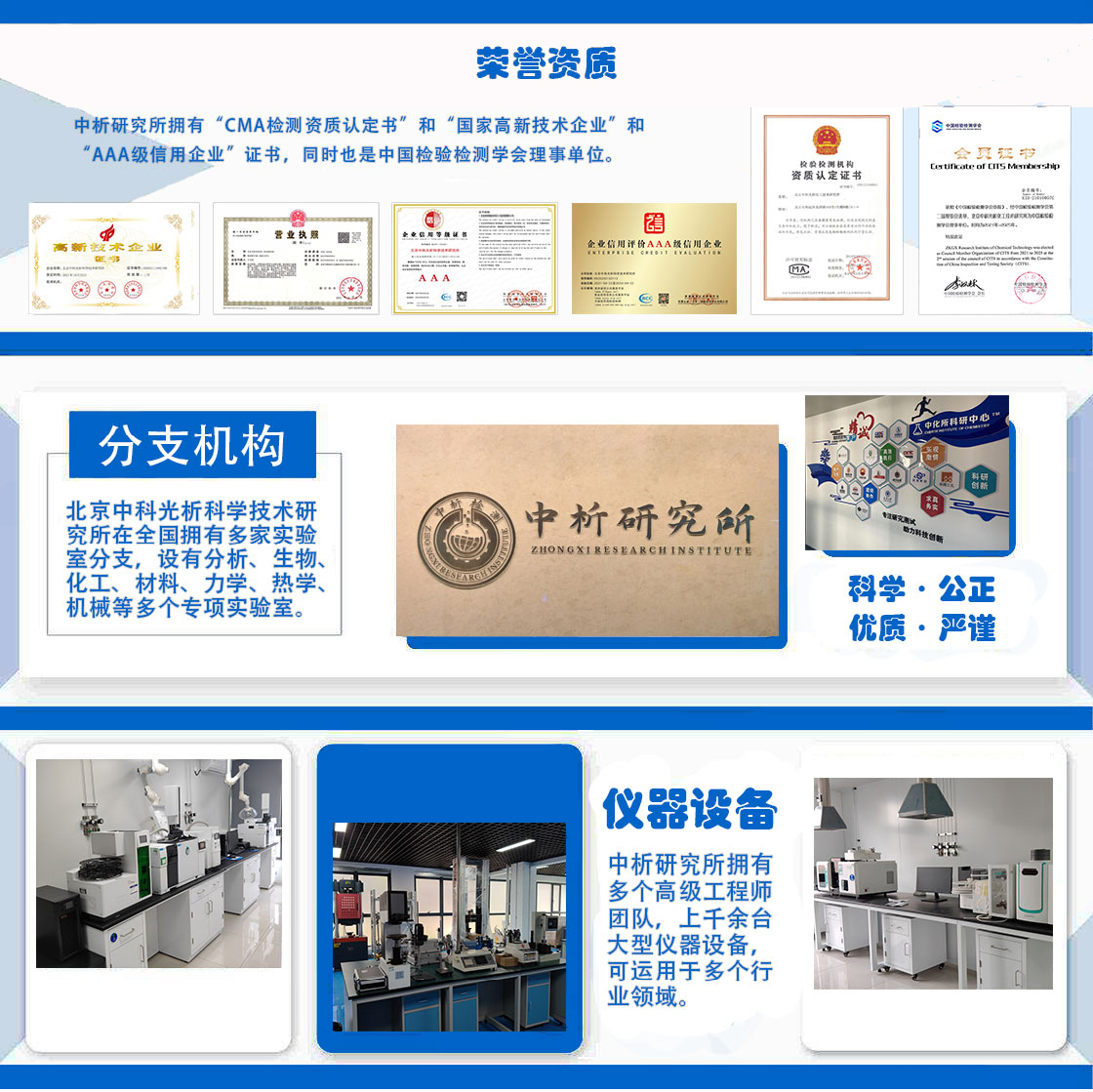
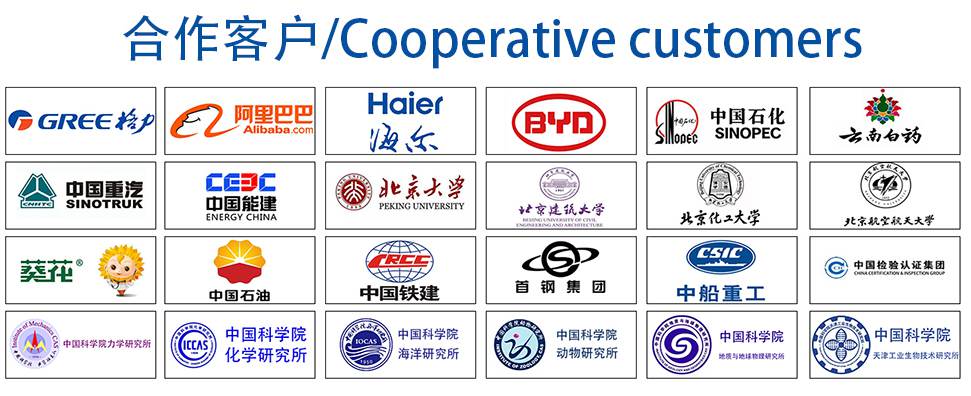