燃料电池堆检测:关键技术与发展现状
燃料电池堆作为燃料电池系统的核心组件,其性能直接影响着能量转换效率、使用寿命和安全性。随着氢能产业的快速发展,燃料电池堆在交通运输、分布式发电等领域的应用日益广泛。为保障其稳定运行,检测技术成为研发、生产和维护环节中不可或缺的一环。燃料电池堆检测涵盖电化学性能、气密性、耐久性、热管理等多个维度,需通过精密仪器和标准化流程实现全生命周期质量监控。本文将重点解析燃料电池堆的关键检测项目及其技术要点。
1. 气密性检测
气密性是燃料电池堆安全运行的基石。检测时需对氢气供应通道、双极板流道及密封元件进行泄漏测试,采用氦质谱检漏法或压力衰减法,精度需达到10⁻⁶ mbar·L/s级别。尤其需关注高温高湿环境下密封材料的形变风险,模拟实际工况下的长期稳定性。
2. 电化学性能检测
通过极化曲线测试评估单电池及整堆的电压-电流特性,分析活化极化、欧姆极化和浓差极化损失。结合电化学阻抗谱(EIS)检测膜电极组件(MEA)的质子传导阻力与电荷转移效率,精准定位性能衰减的微观机制。测试需在恒温恒湿条件下进行,确保数据可比性。
3. 热管理检测
燃料电池堆的温度均匀性直接影响反应效率与寿命。利用红外热像仪监测运行时各单电池的表面温度分布,验证冷却流道设计合理性。同时需测试启停阶段的瞬态热响应能力,防止局部过热导致质子交换膜(PEM)降解。
4. 材料耐久性检测
针对关键部件开展加速老化试验:膜电极需通过干湿循环测试评估机械应力耐受性;双极板进行模拟腐蚀环境下的接触电阻测试;催化剂则需验证抗CO中毒能力。典型测试周期达5000小时以上,结合X射线衍射(XRD)等分析手段量化材料结构变化。
5. 环境适应性检测
模拟极端工况验证整堆可靠性,包括-30℃冷启动性能测试、海拔5000米低气压环境试验、高频振动下的结构完整性测试等。通过多轴振动台与气候模拟舱复现复杂应用场景,确保燃料电池堆在车载、船舶等移动场景中的稳定输出。
6. 安全保护系统检测
重点测试氢气泄漏报警响应时间(≤1秒)、过压保护阀动作精度(±0.05MPa)及故障自诊断系统的误报率。采用故障注入技术模拟短路、反极等异常工况,验证保护电路与软件控制逻辑的可靠性,满足ISO 23273等国际安全标准要求。
随着原位检测技术与数字孪生模型的深度融合,燃料电池堆检测正朝着高精度、智能化的方向发展。建立覆盖设计验证、产线质检到运维监控的全链条检测体系,将成为推动氢能产业规模化应用的关键支撑。
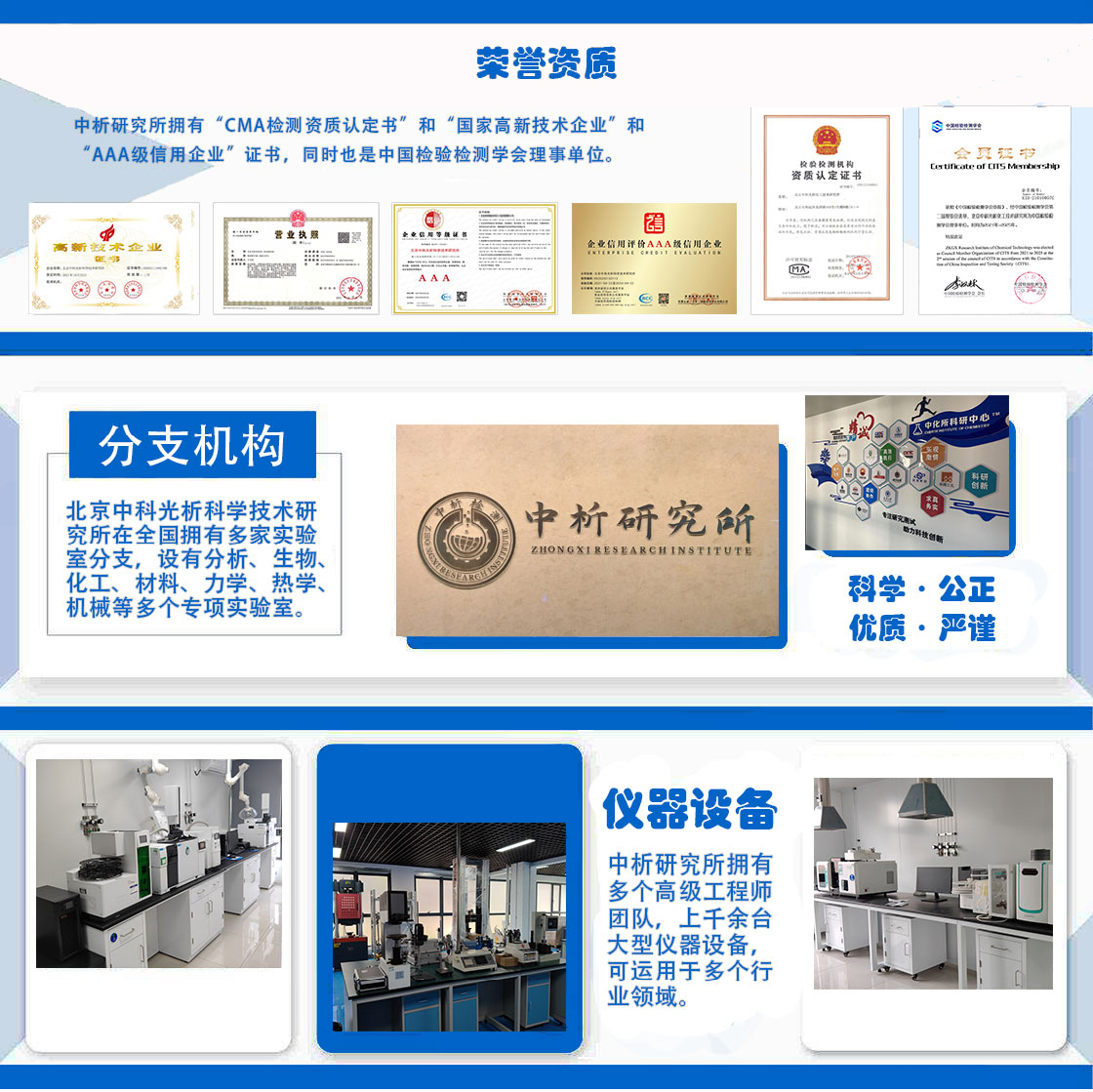
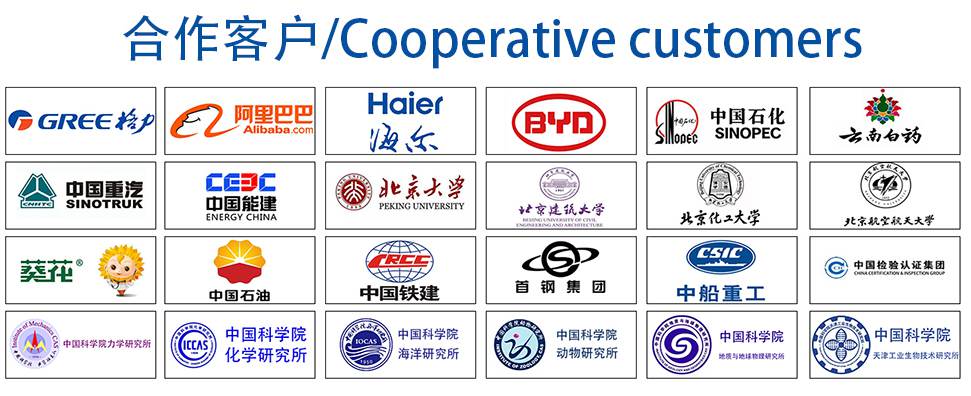