船用柴油机检测项目及重要性解析
船用柴油机作为船舶动力系统的核心设备,其运行状态直接影响航行安全、燃油效率和环保合规性。定期开展系统性检测是保障柴油机高效稳定运转的必要手段,也是国际海事组织(IMO)和船级社强制要求的维护程序。检测项目需覆盖机械性能、排放指标、磨损状态及辅助系统功能等多个维度,通过数据分析和故障预判,可避免因突发故障导致的停航风险或安全事故。
一、核心性能检测项目
1. 燃烧室压力测试 通过压力传感器实时监测气缸内燃烧压力曲线,分析燃油喷射定时、压缩比是否符合设计参数,判断活塞环密封性和气阀闭合状态。
2. 燃油喷射系统检测 包含喷油泵供油压力、喷油器雾化效果及喷油正时校准,使用示波器捕捉喷油波形,及时发现柱塞偶件磨损或针阀卡滞等问题。
3. 压缩压力测试 测量各缸压缩终了压力,对比额定值差异是否超过±5%,用于评估活塞环、缸套及气门组件的磨损情况。
二、排放与环保指标检测
1. 烟气排放分析 使用烟气分析仪检测NOx、SOx、CO和颗粒物浓度,确保符合MARPOL公约Tier III排放标准,尤其关注EGR(废气再循环)或SCR(选择性催化还原)系统的净化效率。
2. 润滑油污染物检测 通过光谱分析润滑油中的金属磨粒、水分和燃油稀释率,判断轴承、缸套等部件的磨损趋势及冷却液泄漏风险。
三、关键部件状态评估
1. 曲轴箱检查 采用内窥镜探查连杆轴承、主轴承的间隙及表面损伤,同步测量曲轴臂距差是否超出0.15mm/m的许可范围。
2. 涡轮增压器检测 检查涡轮叶片腐蚀、轴承振动值及压气机效率,确保增压压力波动不超过标称值的10%。
3. 冷却系统效能测试 评估淡水冷却器温差、海水泵流量及恒温阀启闭精度,防止因散热不良导致的过热拉缸事故。
四、辅助功能与安全装置验证
1. 自动保护系统测试 模拟超速、滑油低压、高温报警等工况,验证紧急停车装置和报警联锁功能的响应可靠性。
2. 振动与噪声监测 使用加速度传感器测量柴油机各部位振动烈度,对比ISO 10816标准判断轴系对中状态和底座刚性。
通过以上系统化检测,可构建完整的柴油机健康档案,结合大数据分析实现预测性维护。建议每500运行小时进行常规检测,大修前需增加缸盖探伤、曲轴磁粉检测等深度项目,确保船舶动力系统始终处于最佳工况。
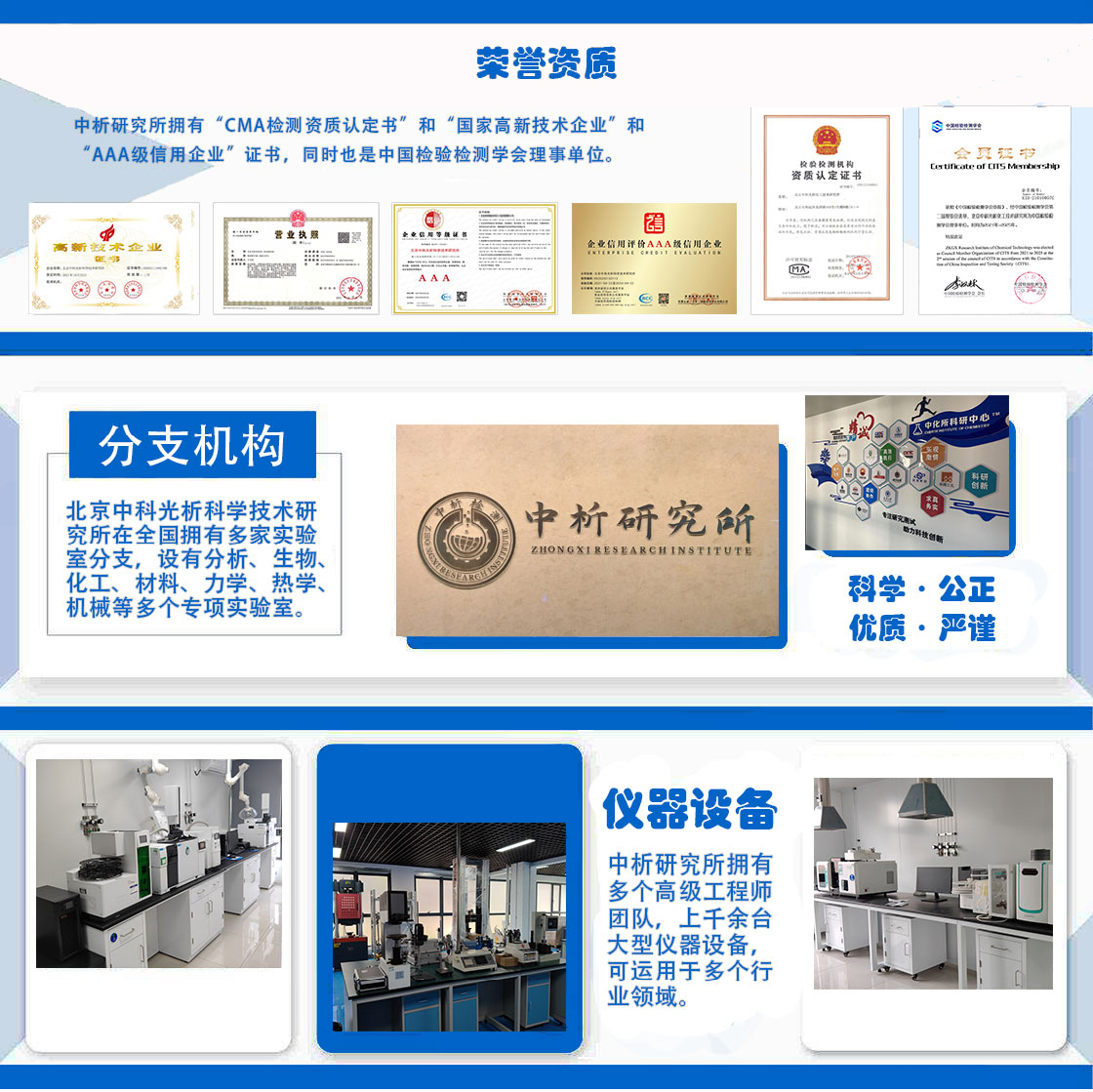
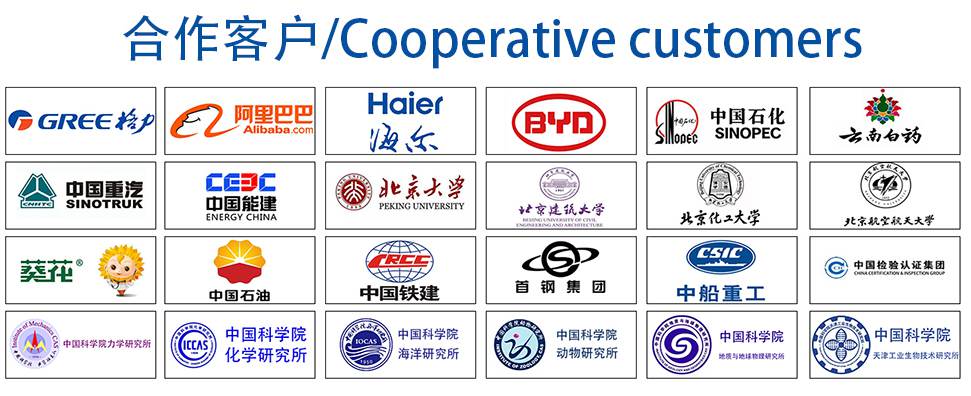