钢的熔焊检测:关键项目与技术要求
钢的熔焊检测是确保焊接结构安全性和可靠性的核心环节,广泛应用于船舶制造、压力容器、桥梁工程及重型机械等领域。熔焊过程中可能因材料特性、工艺参数或操作不当产生气孔、裂纹、未熔合等缺陷,这些缺陷会直接影响构件的承载能力和使用寿命。因此,通过系统化的检测项目对焊接接头的质量进行全面评估,成为现代工业质量控制体系中不可或缺的步骤。
一、无损检测(NDT)项目
1. 目视检测(VT):作为最基础的检测手段,通过放大镜或工业内窥镜检查焊缝表面是否存在咬边、凹陷、飞溅等可见缺陷,同时验证焊缝尺寸是否符合设计要求。
2. 射线检测(RT):利用X射线或γ射线穿透焊缝,通过胶片或数字成像系统检测内部气孔、夹渣、未焊透等缺陷,尤其适用于厚度较大构件的三维缺陷定位。
3. 超声波检测(UT):通过高频声波在材料中的传播特性,精确检测焊缝内部裂纹、未熔合等平面型缺陷,具有灵敏度高、可实时成像的特点。
4. 磁粉检测(MT):对铁磁性材料表面及近表面裂纹检测效果显著,通过磁化后施加磁粉观察磁痕分布,可快速发现微小线性缺陷。
5. 渗透检测(PT):适用于非多孔材料的表面开口缺陷检测,通过显像剂吸附渗透液形成指示痕迹,操作简便且成本较低。
二、破坏性检测项目
1. 拉伸试验:截取焊接接头试样进行拉伸,测定抗拉强度、屈服强度及断后延伸率,验证焊缝金属与母材的力学匹配性。
2. 弯曲试验:通过正弯、背弯或侧弯试验评估焊缝的塑性和界面结合质量,检测未熔合或脆性相的存在。
3. 冲击试验:在低温环境下对焊缝热影响区进行夏比冲击测试,评估材料抗脆断能力,尤其适用于低温压力容器用钢。
4. 硬度测试:采用维氏或洛氏硬度计测量焊缝区、热影响区及母材的硬度梯度,判断焊接热循环对材料性能的影响。
三、化学成分与金相分析
1. 光谱分析:使用直读光谱仪检测焊缝金属的C、Mn、Si等元素含量,确保符合材料标准要求。
2. 金相显微镜检测:通过微观组织观察分析焊缝区晶粒尺寸、相组成及夹杂物分布,评估焊接工艺的合理性。
3. 腐蚀试验:针对特殊用途钢材(如不锈钢),进行晶间腐蚀或应力腐蚀试验,验证焊缝的抗腐蚀性能。
四、特殊工况附加检测
对于核电、深海设备等极端环境应用场景,需增加疲劳试验、蠕变试验及断裂韧性测试,同时结合数字射线成像(DR)和相控阵超声波(PAUT)等齐全技术实现高精度缺陷表征。
通过上述检测项目的系统实施,可全面掌握钢的熔焊接头质量状态。现代检测技术已逐步向自动化、智能化方向发展,如AI辅助的缺陷识别系统和在线监测平台的应用,显著提升了检测效率和结果可靠性,为工程安全提供坚实保障。
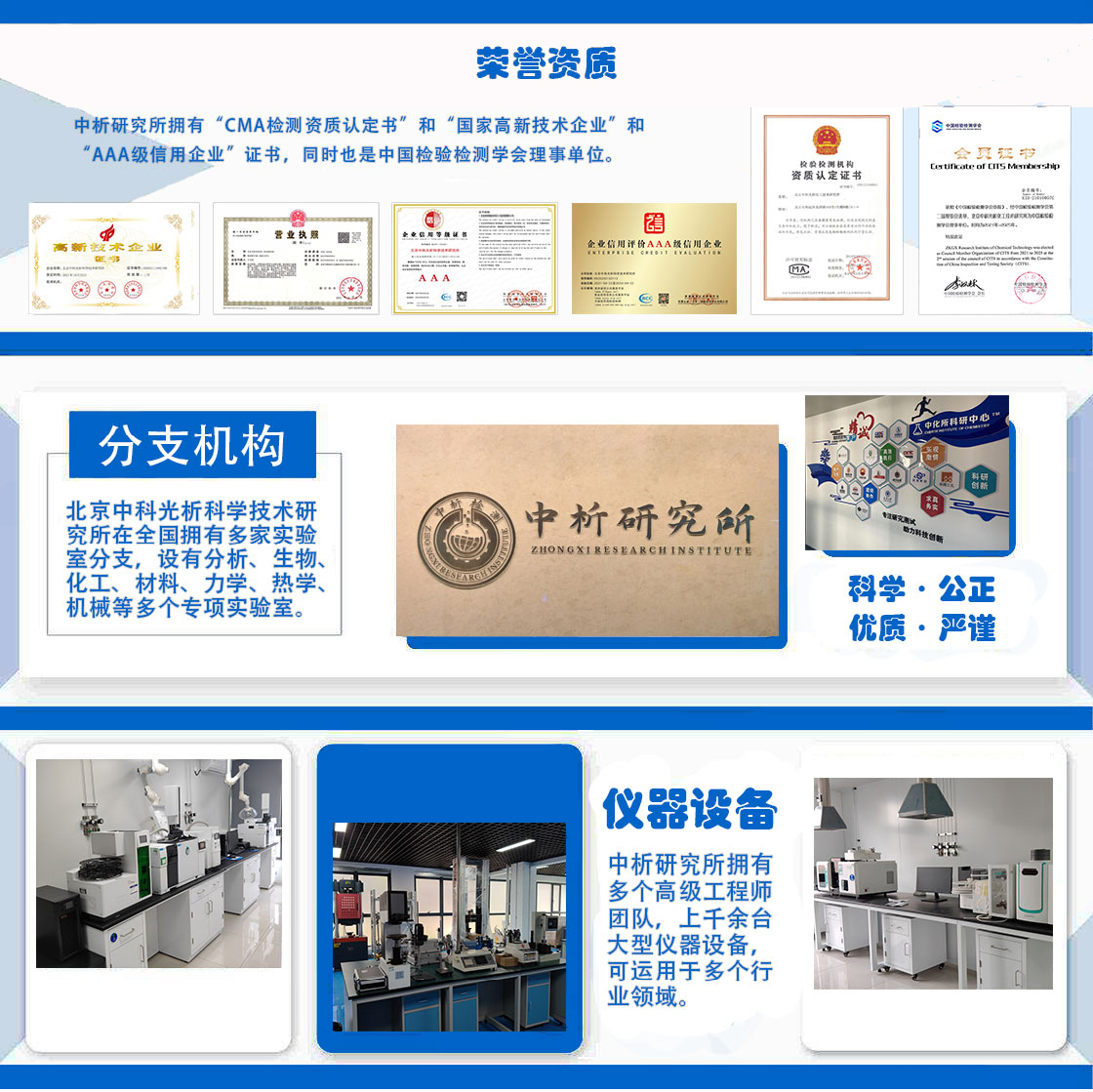
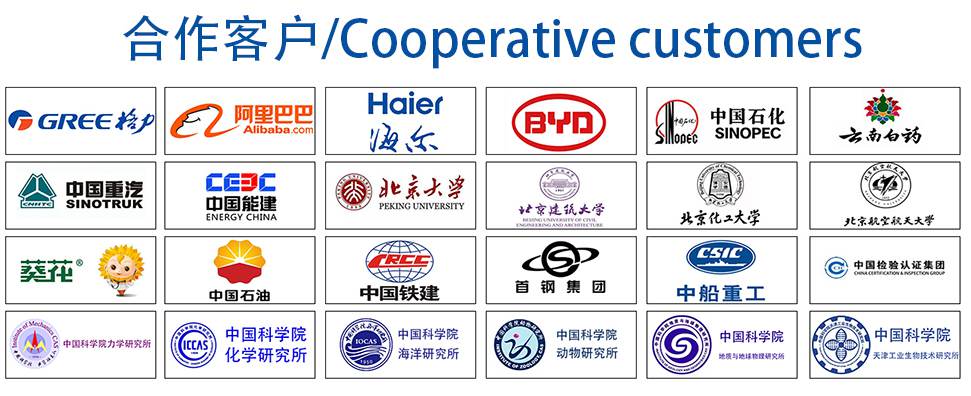