电磁轭磁粉探伤仪检测原理与意义
电磁轭磁粉探伤仪是一种基于磁粉检测原理的无损检测设备,广泛应用于金属材料表面及近表面缺陷的检测。其核心原理是利用电磁轭产生的交变磁场对被测工件进行磁化,当工件存在裂纹、气孔或夹杂等不连续性缺陷时,磁场会在缺陷处形成漏磁场,吸附磁粉形成可见磁痕,从而直观显示缺陷位置和形貌。该方法对铁磁性材料(如碳钢、铸铁、合金钢等)的检测具有灵敏度高、操作便捷和成本低的优势,是工业领域质量控制、设备维护和安全隐患排查的重要手段。
电磁轭磁粉探伤仪检测项目分类
电磁轭磁粉探伤仪的检测项目可分为设备性能检测和实际应用检测两大类:
1. 设备性能检测
• 提升力测试:通过测量电磁轭在极间距下的磁极提升力,验证磁场强度是否符合标准要求(如AC磁轭≥44N,DC磁轭≥177N);
• 灵敏度测试:使用标准试片(如A1型30/100试片)验证设备对微小缺陷的识别能力;
• 绝缘性能检测:检查设备电路对地绝缘电阻(通常要求≥2MΩ);
• 电流稳定性测试:监测磁化电流在连续工作时的波动范围。
2. 实际应用检测
• 焊缝检测:用于压力容器、管道焊接接头的表面裂纹检测;
• 铸锻件检测:发现铸造气孔、锻造折叠等缺陷;
• 在役设备检测:对机械部件(如齿轮、轴类)进行疲劳裂纹检查;
• 返修件检测:验证缺陷修复后的质量符合性。
检测流程与标准规范
典型检测流程包括:表面预处理→磁悬液施加→磁化操作→磁痕观察→退磁处理→结果记录。需遵循NB/T 47013.4-2015《承压设备无损检测 第4部分:磁粉检测》和GB/T 26951-2011《焊缝无损检测 磁粉检测》等标准,重点控制以下参数:
• 磁化时间:单次通电1-3秒,避免过热;
• 磁极间距:控制在75-200mm范围内;
• 磁悬液浓度:荧光磁粉1-3g/L,非荧光磁粉10-25g/L;
• 观察条件:白光强度≥1000lx,荧光检测时环境照度≤20lx。
常见问题与质量控制要点
检测过程中需注意:
• 伪磁痕识别:区分由划痕、锈蚀等引起的非相关显示;
• 磁场方向控制:采用交叉磁化法确保全方位检测;
• 检测覆盖率:保证相邻磁化区域重叠≥25%;
• 环境温度影响:-10℃~50℃范围内需进行仪器校准。
电磁轭磁粉探伤仪检测作为常规无损检测手段,其有效性依赖于规范的检测流程、合格的设备性能和操作人员的技术水平。定期进行设备校准(推荐周期12个月)和人员资格认证(按ISO 9712要求),可确保检测结果的准确性和可靠性,为工业设备安全运行提供有力保障。
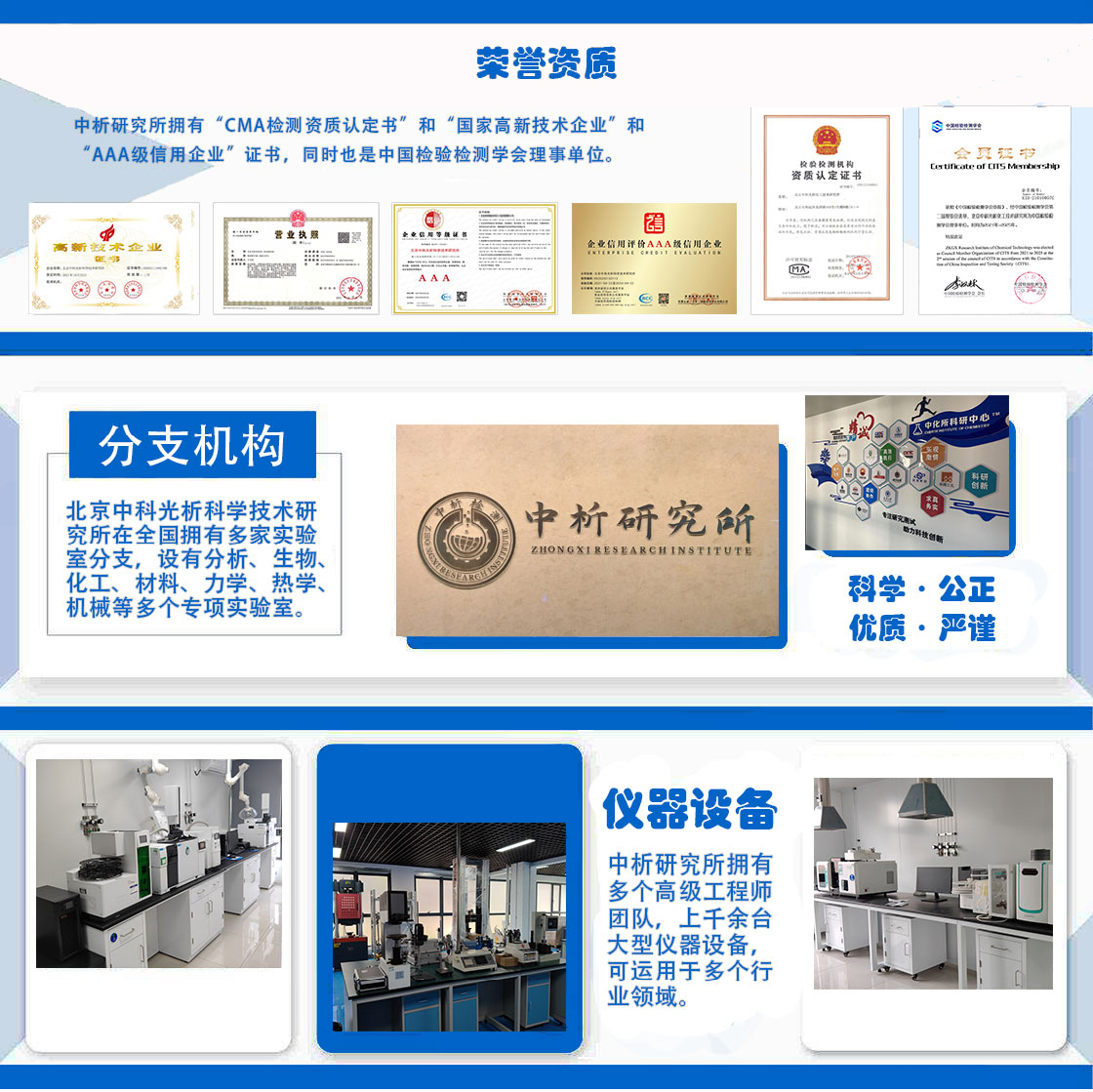
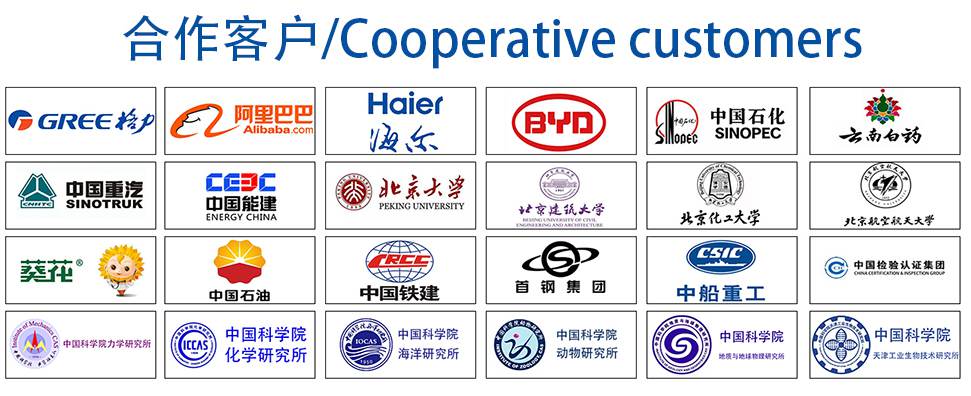