四球摩擦试验机检测原理与应用
四球摩擦试验机是评价润滑剂极压性能和抗磨损性能的核心设备,广泛应用于润滑油、润滑脂、金属加工液及材料摩擦学研究中。其核心原理是通过三个固定钢球与顶部旋转钢球形成点接触摩擦副,在设定载荷、转速和温度条件下模拟极端摩擦工况。通过检测磨痕直径、摩擦系数、烧结负荷等参数,可量化分析材料的抗磨性、极压性及润滑剂效能,为工业设备选油、产品研发和质量控制提供关键数据支撑。
核心检测项目解析
1. 极压性能测试(EP特性)
通过逐级增加载荷直至发生卡咬或烧结,测定最大无卡咬负荷(PB值)、烧结负荷(PD值)及综合磨损值(ZMZ)。该测试反映润滑剂在边界润滑状态下承受极端压力的能力,尤其适用于齿轮油、液压油等重载润滑剂的性能评价,符合ASTM D2596、GB/T 3142等标准。
2. 抗磨损性能检测
在固定载荷下运行30-60分钟,测量底部三球的磨斑直径(WSD)。通过金相显微镜观测磨痕形貌,结合磨痕直径计算磨损体积,评估润滑剂的长期保护性能。该指标对发动机油、导轨油等需持续抗磨保护的油品至关重要。
3. 摩擦系数测定
通过扭矩传感器实时监测摩擦扭矩,结合赫兹接触理论计算动态摩擦系数。该数据可揭示润滑剂的减摩特性,对节能型润滑油开发及摩擦副能效优化具有指导意义,测试方法遵循SH/T 0762标准。
4. 特殊工况模拟检测
包括高温试验(150℃以上)、腐蚀性介质环境测试、往复运动摩擦等扩展项目。通过改造试验腔体或加载特殊运动模式,可针对性评估润滑剂在风电齿轮箱、海洋装备等特殊场景下的适用性。
检测结果的关键价值
四球试验数据可建立润滑剂性能数据库,指导配方优化:PB值提升20%意味着齿轮油承载能力显著增强;磨斑直径减少0.1mm可使轴承寿命延长30%。同时结合扫描电镜(SEM)和能谱分析(EDS),还能揭示添加剂作用机制与失效机理,为下一代高性能润滑材料开发提供理论依据。
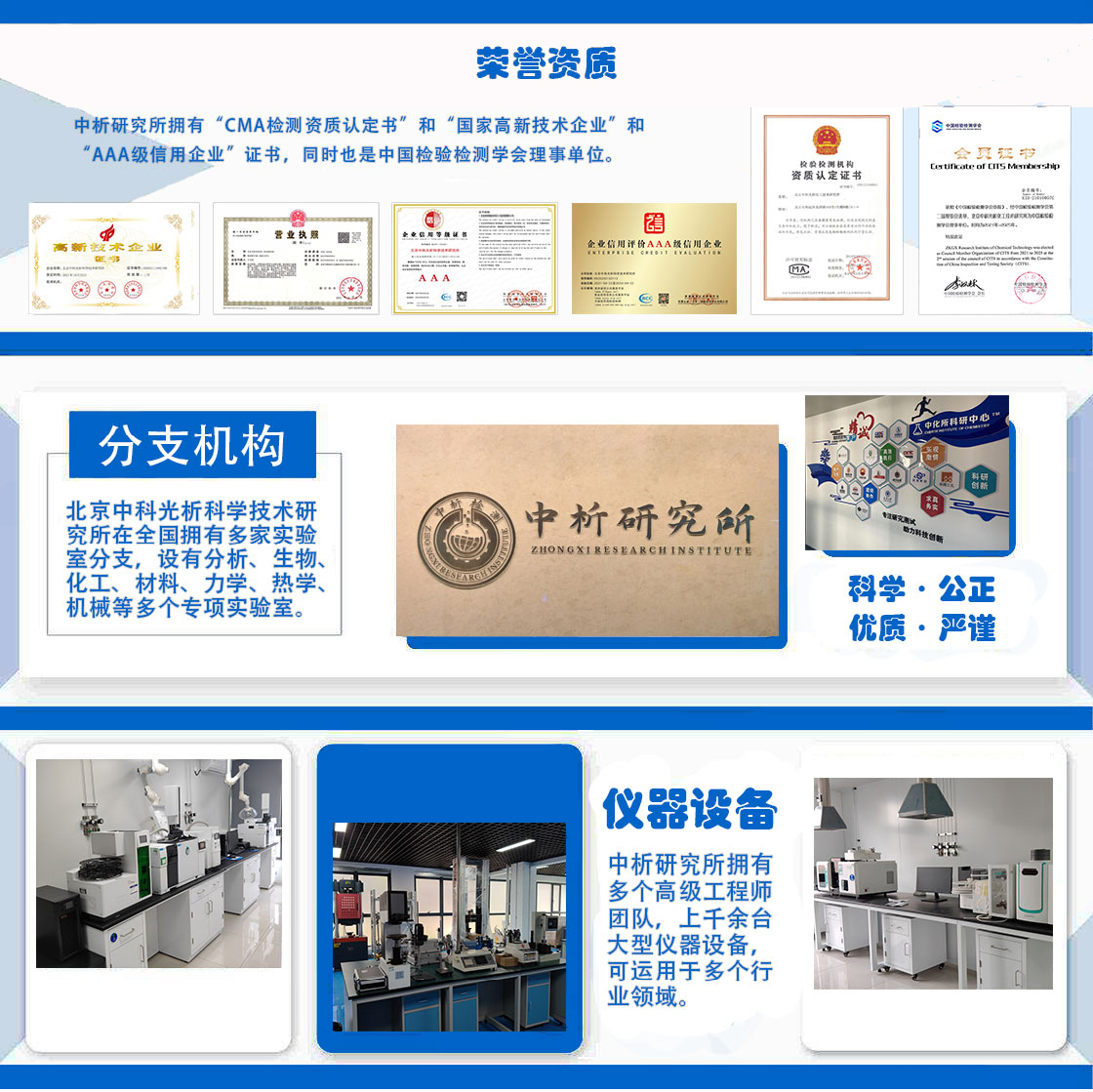
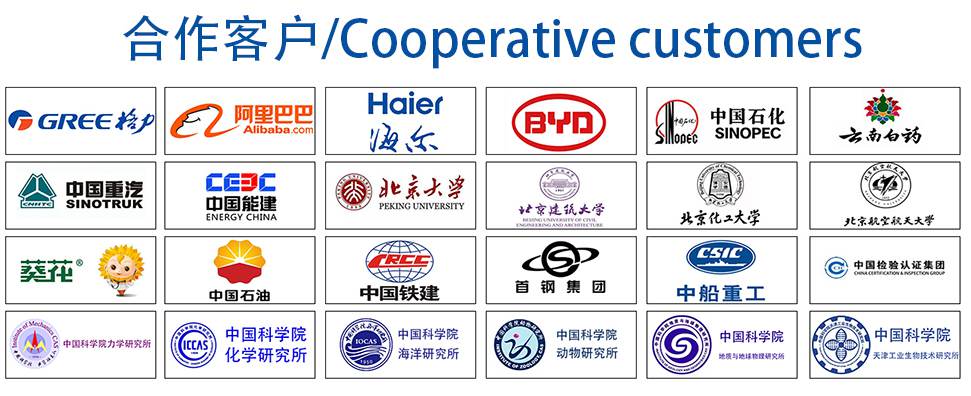