钢轨及钢轨焊接接头检测的重要性
钢轨作为铁路运输系统的核心承载部件,直接关系列车运行的安全性与轨道结构的稳定性。在长期高负荷、复杂环境(如温度变化、振动冲击)的作用下,钢轨本体及焊接接头易产生疲劳裂纹、磨耗、变形等缺陷。焊接接头作为钢轨连接的关键环节,其质量直接影响轨道连续性,若存在未熔合、气孔或夹杂等问题,可能引发断轨事故。因此,对钢轨及焊接接头进行系统性检测是铁路运维中不可或缺的工作,需结合无损检测、理化分析等手段,确保其性能符合国家标准(如TB/T 2344、TB/T 1632)。
主要检测项目及方法
1. 外观及几何尺寸检测
通过目视观察、量具测量等方式检查钢轨表面是否存在裂纹、压痕、锈蚀及焊接接头错边、焊瘤等缺陷。同时对轨头宽度、轨腰厚度、轨底平整度等关键尺寸进行精度验证,确保符合轨道几何形位要求。
2. 超声波探伤检测
利用多通道超声波探伤仪对钢轨本体及焊缝区域进行内部缺陷扫描,可检测深度超过1mm的纵向裂纹、横向裂纹及夹杂物。通过调整探头频率(通常2-5MHz)和入射角度,实现轨头、轨腰、轨底的全覆盖检测,灵敏度需满足TB/T 2658标准。
3. 硬度与金相分析
采用维氏硬度计测量钢轨母材、热影响区及焊缝的硬度值,评估焊接工艺是否造成组织劣化。结合金相显微镜观察显微组织(如珠光体含量、晶粒度),判断是否存在过烧、未回火马氏体等异常情况,确保材料性能一致性。
4. 力学性能试验
对焊接接头进行拉伸试验(检测抗拉强度≥880MPa)、冲击试验(-20℃下冲击功≥35J)及弯曲试验(弯曲角度≥120°无裂纹),验证其动态承载能力和韧性指标。试验需严格遵循GB/T 2651-2008规范。
5. 残余应力检测
使用X射线衍射法或盲孔法测量焊接区域的残余应力分布,评估应力集中风险。对高速铁路等关键区段,要求纵向残余应力不超过材料屈服强度的30%,横向应力需控制在更低水平。
6. 服役状态监测
采用轨道检测车定期进行动态巡检,通过激光轮廓扫描、声学检测等技术,实时监测钢轨波磨、侧磨及焊缝平顺度变化,建立缺陷发展预测模型,为预防性维护提供数据支持。
检测周期与标准
根据线路等级制定差异化检测方案:高铁正线每3月进行一次综合检测,普通线路每6-12月检测一次。对探伤发现的Ⅱ级及以上缺陷需立即处理,并建立全生命周期档案,实现质量追溯。
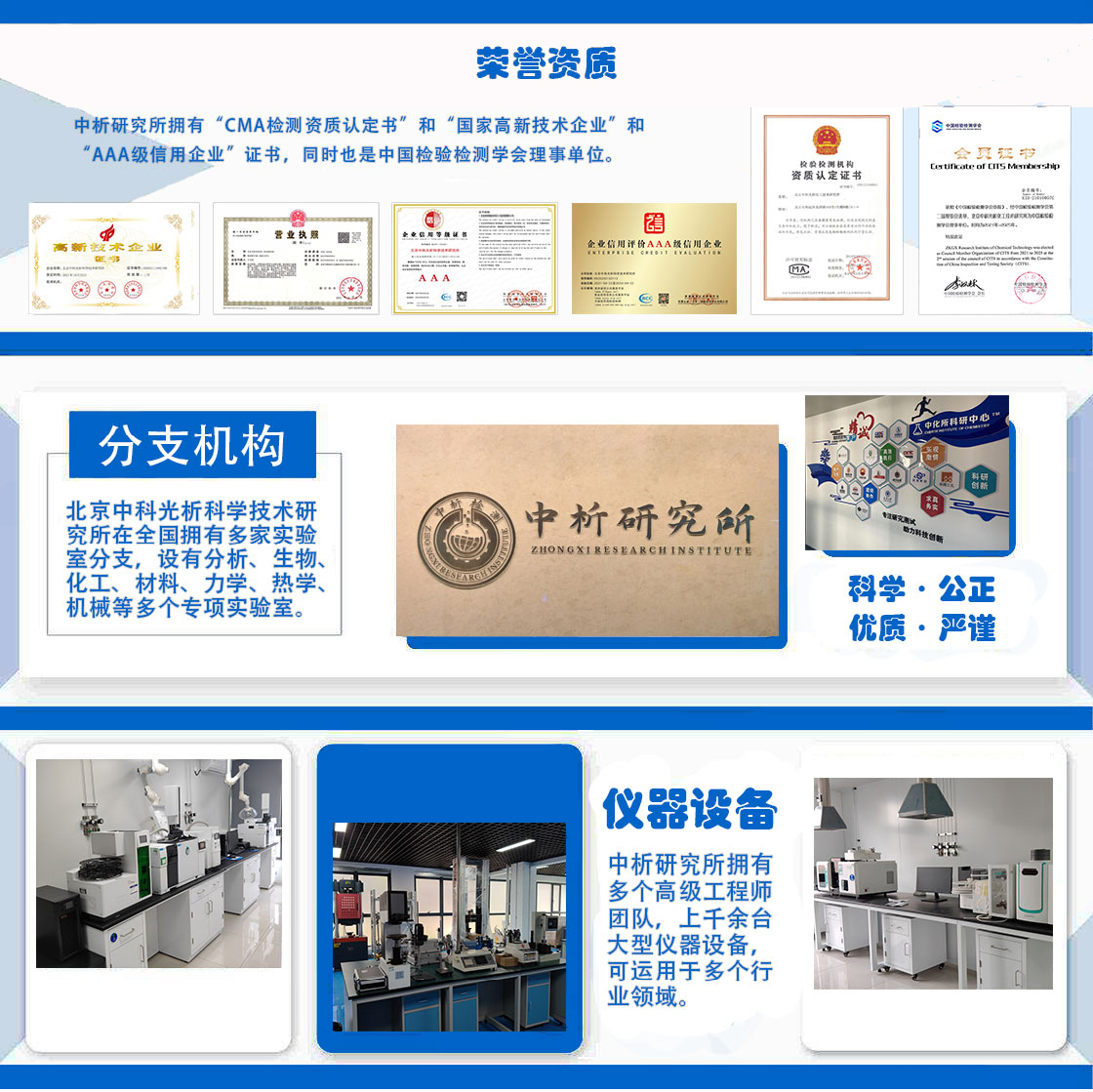
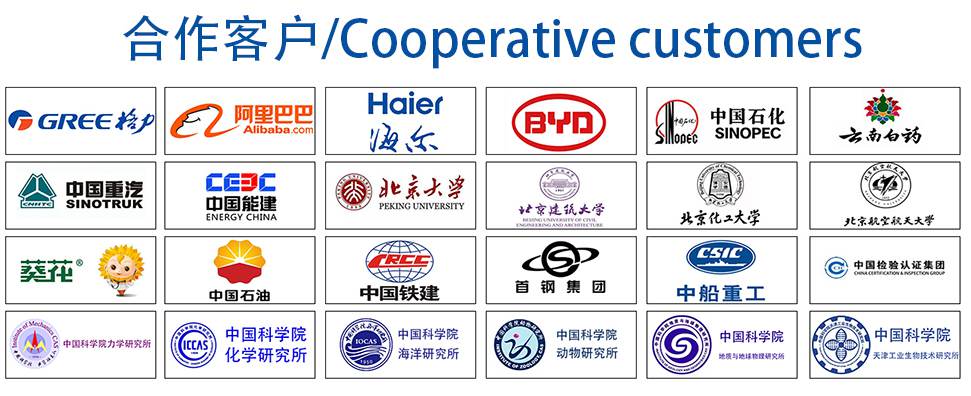