功能测量检测:保障系统性能与可靠性的关键技术
在当今高度依赖技术系统的工业制造、电子产品开发及智能化设备应用领域,功能测量检测已成为确保产品性能达标、系统稳定运行的核心环节。通过科学规范的检测手段,工程师能够精确评估被测对象的实际功能表现,验证其是否符合设计指标、行业标准及用户需求。这项技术不仅涉及硬件系统的物理参数测量,还包含软件功能的逻辑验证,在智能制造、自动驾驶、医疗设备等关键领域具有不可替代的重要性。
功能测量检测的核心项目
完整的检测体系通常包含以下关键项目:
1. 功能验证测试(FVT):通过预设场景模拟验证设备/软件的基本功能实现情况,包括输入输出响应、异常处理能力等。采用自动化测试框架可提升测试覆盖率至95%以上。
2. 性能参数测量:针对系统响应时间、吞吐量、资源占用率等关键指标进行量化检测。如工业机器人需检测重复定位精度(通常要求±0.02mm)、最大负载下的工作稳定性等。
3. 环境适应性测试:包括温度循环测试(-40℃~85℃)、振动测试(5Hz~2000Hz)、电磁兼容(EMC)等,确保设备在极端条件下的功能可靠性。
齐全检测技术手段
现代检测系统融合多项创新技术:
自动化测试平台:基于LabVIEW、TestStand等工具构建的自动化测试系统可实现7×24小时连续测试,测试效率提升300%以上。
机器视觉检测:采用高分辨率工业相机(500万像素以上)配合深度学习算法,实现微米级尺寸测量和表面缺陷检测。
虚拟仿真测试:通过数字孪生技术建立设备虚拟模型,可在产品原型阶段完成80%以上的功能验证。
典型行业应用场景
不同领域对检测要求呈现差异化特征:
汽车电子:需满足ISO 26262功能安全标准,重点检测ECU控制精度(±0.5%)、CAN总线通信可靠性等。
医疗设备:严格执行IEC 60601标准,检测项目包括生命体征监测精度(如血氧饱和度±2%)、设备电磁辐射值等。
工业物联网:着重检测传感器数据采集精度(0.1%F.S.)、网络传输时延(<50ms)、边缘计算响应速度等关键指标。
检测质量保障要点
为确保检测结果的有效性,需特别注意:
1. 量值溯源体系:定期对检测设备进行计量校准,建立完整的测量不确定度评估报告。
2. 测试用例管理:采用需求追溯矩阵(RTM)确保测试用例100%覆盖设计规范要求。
3. 数据分析深度:运用大数据分析技术,从海量测试数据中挖掘潜在质量风险,缺陷预测准确率可达85%以上。
随着人工智能和5G技术的深度融合,功能测量检测正朝着智能化、无线化、云端化的方向发展。建立完善的检测体系不仅能有效降低产品召回风险,更能通过持续的质量改进提升企业核心竞争力。选择检测方案时应综合考虑测试对象特性、行业标准要求和全生命周期成本,实现质量与效益的最佳平衡。
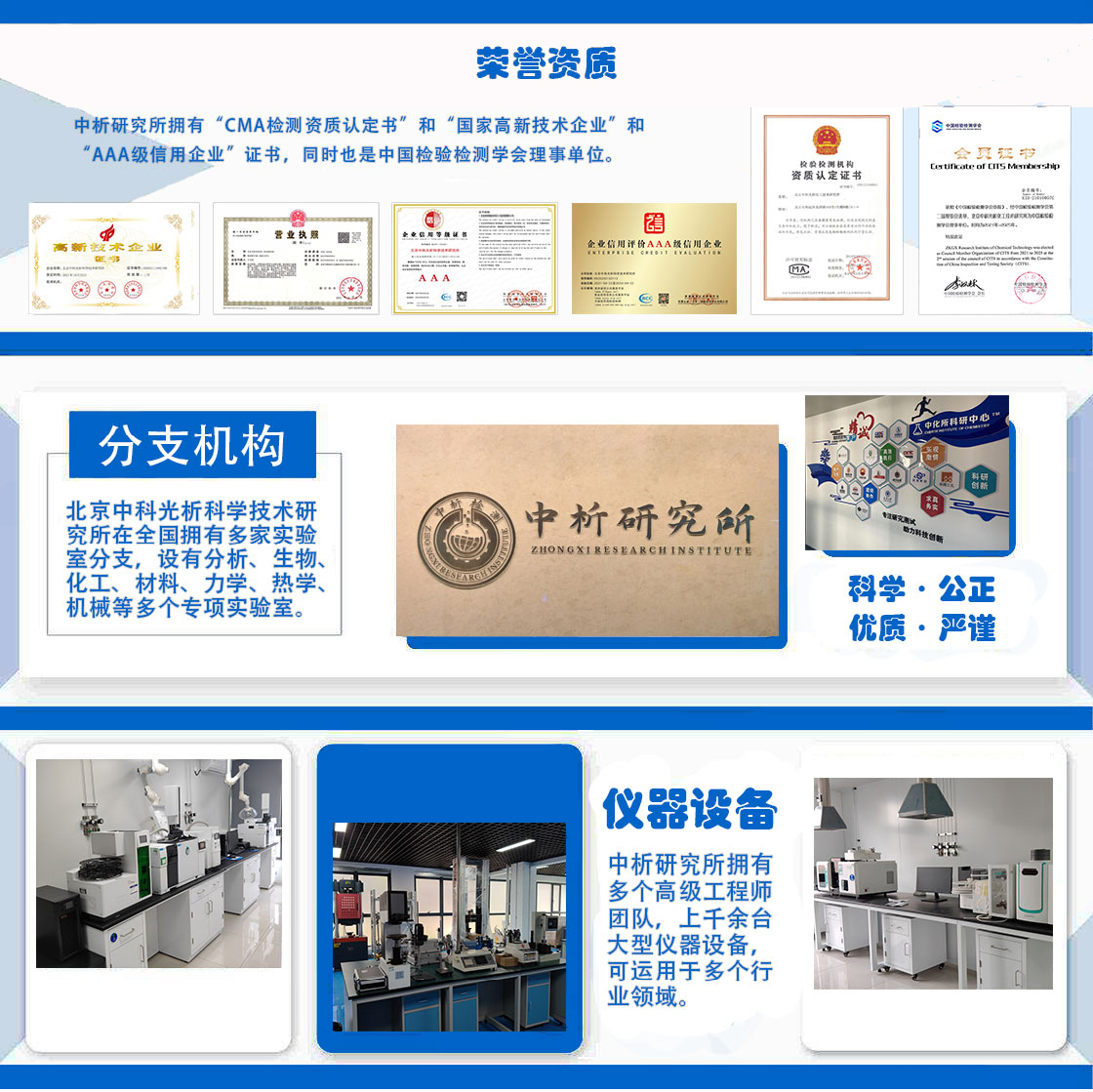
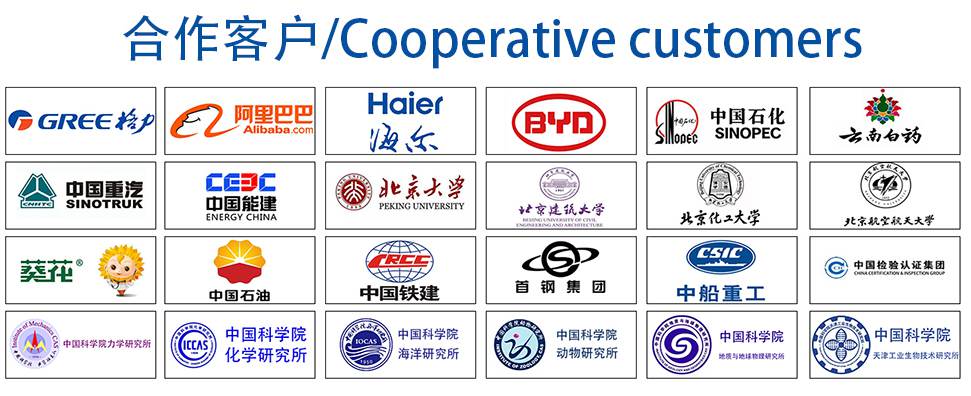