钢结构节点检测的重要性与必要性
钢结构节点作为建筑或桥梁等工程中的核心连接部位,承担着传递荷载、协调结构变形的重要作用。其性能直接影响整体结构的稳定性、安全性和耐久性。由于节点通常处于复杂应力状态,且在施工或使用过程中可能受到焊接缺陷、材料老化、环境腐蚀等因素影响,节点失效已成为钢结构事故的主要诱因之一。因此,通过科学系统的检测手段对钢结构节点进行全面评估,是保障工程安全、预防潜在风险的关键环节。节点检测不仅能发现既有问题,还能为维修加固提供数据支持,同时满足国家规范(如GB 50205、JGJ/T 483等)对施工质量验收和运维管理的强制性要求。
钢结构节点检测的主要项目
1. 焊缝质量检测
采用超声波探伤(UT)、磁粉检测(MT)或射线检测(RT)技术,对节点焊缝的内部缺陷(如气孔、夹渣)及表面裂纹进行无损检测,结合目视检查确认焊缝尺寸、咬边、未熔合等表观质量。对于重要节点需进行焊缝力学性能抽检,包括拉伸试验和冲击韧性测试。
2. 螺栓连接状态检查
通过扭矩扳手复验高强度螺栓的预紧力,检查螺栓缺失、松动或断裂情况,评估垫片安装规范性和防松措施有效性。对锈蚀严重区域需采用硬度测试或光谱分析判断螺栓材质退化程度。
3. 节点变形与位移测量
使用全站仪、激光扫描仪或三维摄影测量技术,量化节点区域的实际变形量,比对设计允许偏差值。重点关注拼接节点错位、法兰盘翘曲等异常现象,必要时进行应力应变监测。
4. 防腐与防火涂层检测
利用涂层测厚仪、附着力测试仪评估防护层厚度均匀性及粘结强度,通过电化学阻抗谱(EIS)分析涂层劣化程度。对于防火涂料需进行耐火极限验证试验,检查膨胀层完整性。
5. 材料性能验证
通过现场取样或便携式光谱仪对节点部位钢材进行化学成分分析,确认材料牌号符合设计要求。硬度测试、金相显微镜观察可辅助判断材料是否存在过热损伤或疲劳劣化。
6. 连接板与加劲板检查
检查连接板孔位偏差、边缘撕裂及加劲板焊接质量,使用应变片监测应力集中区域的荷载分布情况。对于复杂节点可采用有限元分析验证受力合理性。
7. 节点区域疲劳评估
针对承受循环荷载的节点,采用声发射技术捕捉裂纹萌生信号,结合断裂力学理论计算剩余疲劳寿命。动态应变测试可获取实际应力幅值,用于S-N曲线校核。
8. 环境影响因素分析
评估腐蚀介质(如氯离子、二氧化硫)浓度对节点部位的侵蚀风险,检测湿度、温度波动引起的材料膨胀差异。对处于特殊环境(海洋、化工区)的节点需增加腐蚀速率监测。
9. 数字化检测技术应用
引入三维激光扫描建立节点BIM模型,通过点云数据对比发现细微变形;利用数字孪生技术模拟节点在不同工况下的响应,实现缺陷可视化定位与风险预测。
检测实施与结果判定
检测工作应遵循"先外观后内部、先无损再有损"的流程原则,结合目视检查、仪器检测和计算分析多维验证。检测数据需与设计文件、验收标准进行对比,对不达标项目需明确整改措施。最终形成包含缺陷分布图、安全评级及维护建议的综合性检测报告,为钢结构全生命周期管理提供依据。
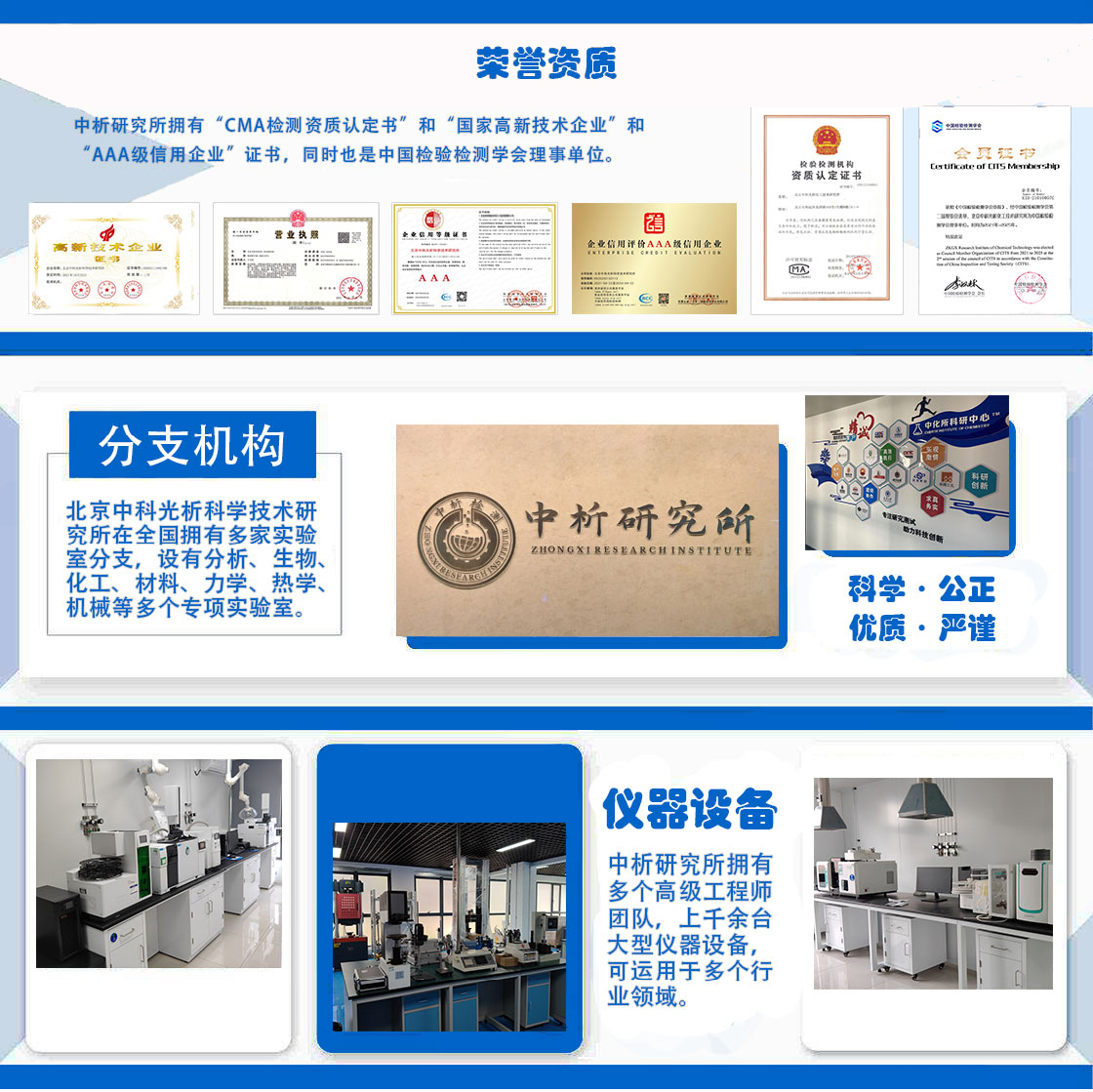
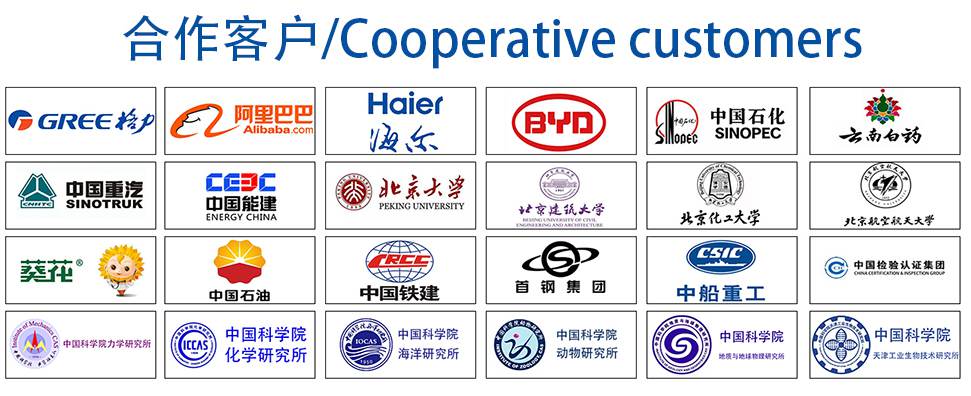