机械设备检测:保障生产安全与运行效率的核心手段
在工业生产、能源开发、交通运输等领域,机械设备作为核心生产力载体,其运行状态直接影响企业经济效益与人员安全。据统计,每年因设备故障导致的直接经济损失超过千亿美元,其中60%以上可通过有效检测提前规避。机械设备检测通过系统性技术手段,对设备的结构完整性、性能参数、磨损程度及潜在风险进行科学评估,已成为现代企业设备管理体系中不可或缺的环节。它不仅涵盖设备全生命周期管理,更涉及振动分析、温度监测、润滑油检测等30余项专业检测技术,形成从基础目视检查到智能诊断的多维度防护体系。
关键检测项目分类与技术解析
1. 结构完整性检测
采用磁粉探伤(MT)、超声波检测(UT)等无损检测技术,重点检查设备承力部件是否存在裂纹、腐蚀或变形。例如压力容器焊缝检测需达到ASME标准要求的0.5mm精度,涡轮叶片检测则要求实现三维裂纹定位。
2. 动态性能检测
通过振动频谱分析系统(FFT)监测设备运转时的振动烈度,精确诊断转子不平衡、轴承磨损等故障。齐全设备可捕捉20000Hz高频振动信号,配合ISO10816标准进行状态分级,实现0.01mm级位移量检测。
3. 热力学状态监测
使用红外热像仪进行温度场扫描,可发现电气接头过热、轴承缺油等异常。重点区域温升监测需满足NB/T47013标准,检测精度可达±1℃。某化工厂通过此项检测提前3个月发现压缩机缸体过热隐患,避免200万元损失。
4. 润滑系统诊断
油液铁谱分析可检测5μm级磨损颗粒,光谱分析能测定15种金属元素含量。采用PQ指数评估润滑油污染度,当磨粒浓度超过ISO4406标准18/16级时应立即采取维护措施。
5. 智能预测性检测
集成物联网传感器的在线监测系统,可实现振动、温度、压力等20余项参数的实时采集。某发电集团应用大数据分析后,设备故障预警准确率提升至92%,年维修成本降低37%。
检测技术发展趋势与创新应用
随着AI技术的突破,基于深度学习的视觉检测系统可自动识别设备表面缺陷,检测效率提升5倍以上。数字孪生技术构建的设备虚拟模型,能模拟极端工况下的应力分布,预判潜在故障模式。2023年某航空企业应用声发射检测技术,成功在发动机叶片断裂前300小时发出预警,标志着检测技术进入智能预测新时代。
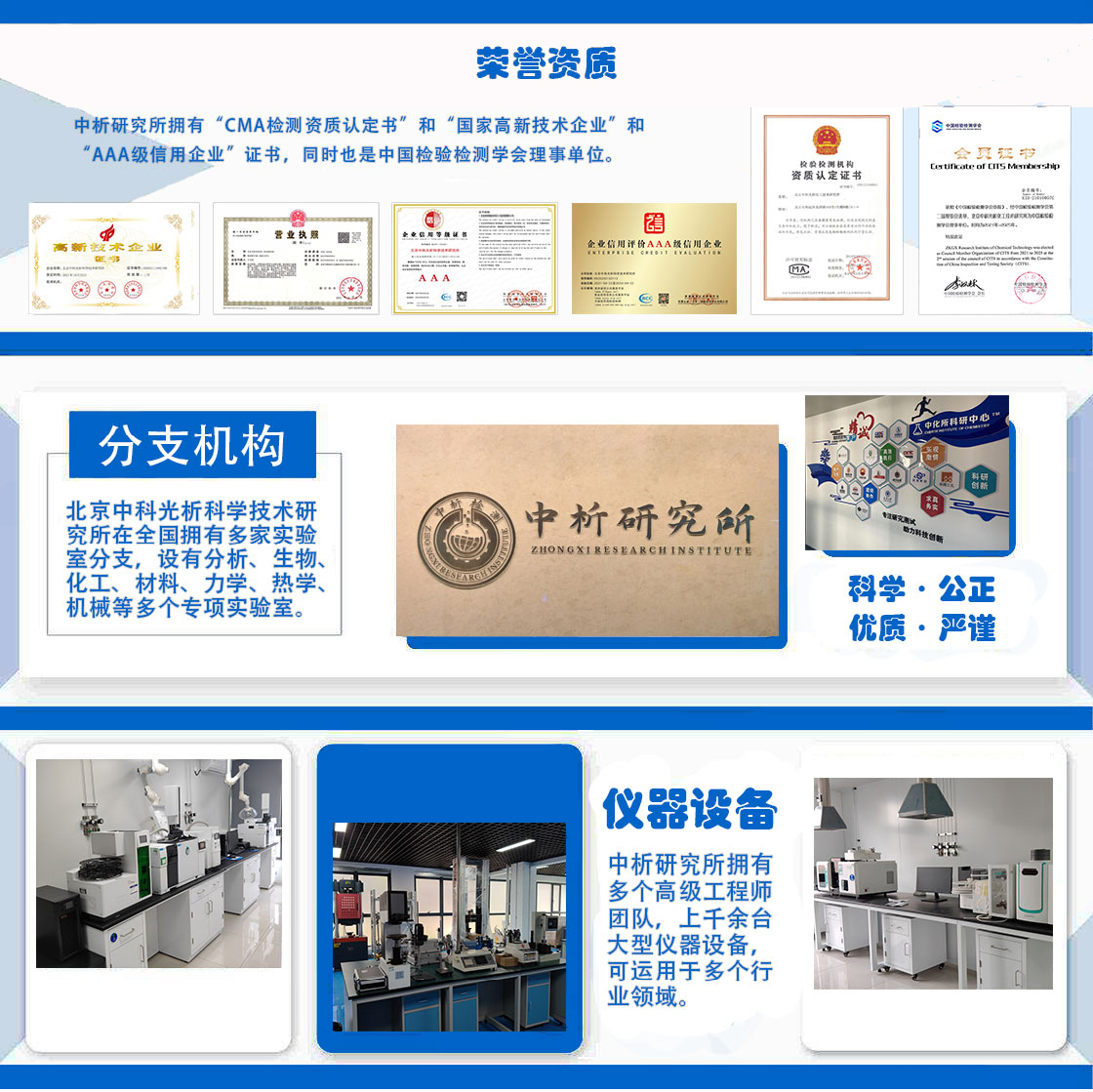
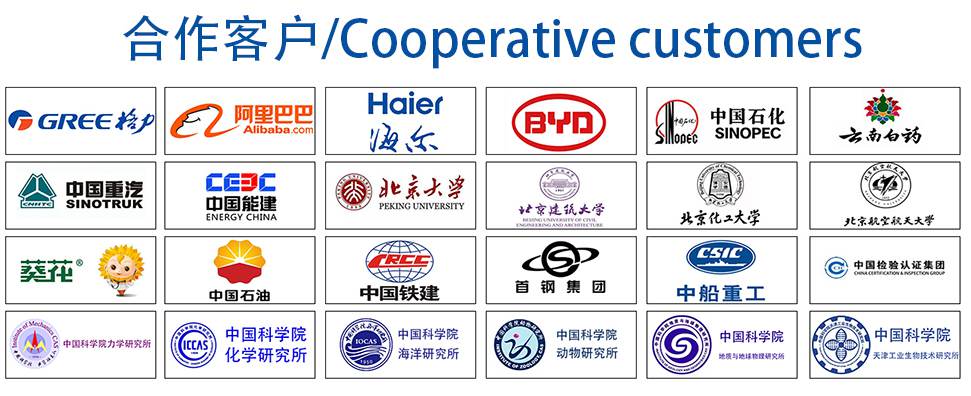