自行车链轮和曲柄检测:保障骑行安全与性能的重要环节
自行车链轮和曲柄是驱动系统的核心部件,直接影响骑行效率、稳定性及安全性。随着骑行运动普及和高端自行车需求增长,对链轮与曲柄的质量检测要求日益严格。专业检测不仅能够提前发现材料缺陷、加工误差或安装问题,还能通过数据化分析优化传动效率,延长零部件使用寿命。尤其在竞技自行车、长途旅行车等场景中,严格的检测流程可避免因部件断裂或磨损导致的意外事故,同时提升骑行的舒适性和动力输出精度。
关键检测项目与技术标准
1. 尺寸精度检测
使用三坐标测量仪(CMM)对链轮齿距、曲柄臂长进行微米级检测,确保符合ISO 4210标准要求。重点关注链轮BCD(螺栓圆周直径)公差±0.2mm,曲柄Q-factor(脚踏间距)偏差不超过±1.5mm。
2. 表面硬度与耐磨性测试
通过洛氏硬度计(HRC)检测链轮齿面硬度(通常要求45-52HRC),曲柄轴心部位需达到25-30HRC。利用摩擦磨损试验机模拟5000公里骑行磨损,检测表层氮化处理或镀层附着力。
3. 动态平衡检测
在专用动平衡机上以200-120rpm转速范围测试曲柄组,要求不平衡量≤15g·mm。对于碳纤维曲柄需额外检测树脂分布均匀性,避免高速运转时共振现象。
4. 极限载荷测试
依据EN 14766标准进行静载试验,曲柄需承受3倍人体重量(≥300kg)的垂直载荷持续60秒无变形。链轮组需通过120N·m扭矩循环测试50000次,检测齿形磨损和裂纹扩展情况。
5. 材料成分分析
采用直读光谱仪检测铝合金曲柄的6061-T6或7075-T6材质配比,链轮铬钼钢需含Cr 1.0-1.2%、Mo 0.15-0.25%。碳纤维部件需通过CT扫描验证叠层结构和孔隙率(<2%)。
6. 组装配合度检测
使用扭矩传感器验证中轴与曲柄的配合精度,装配扭矩误差需控制在±5%范围内。通过激光对中仪确保链轮与飞轮的平面度偏差≤0.1mm,减少链条横向应力。
智能化检测技术应用趋势
当前主流检测机构已引入AI视觉检测系统,通过深度学习算法自动识别链轮齿形异常。同步采用数字孪生技术建立3D仿真模型,预测不同骑行场景下的应力分布,检测效率较传统方式提升40%以上。
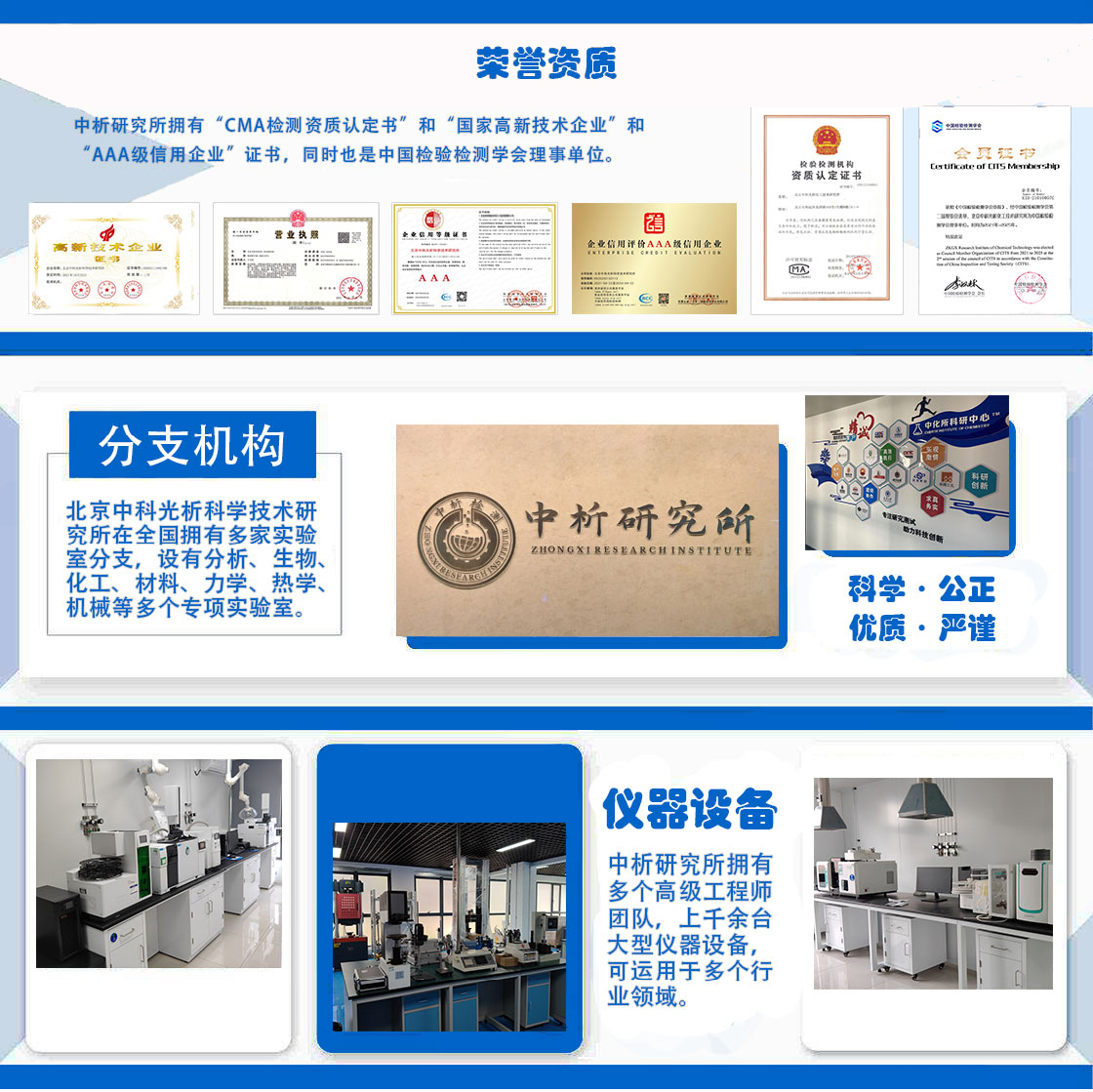
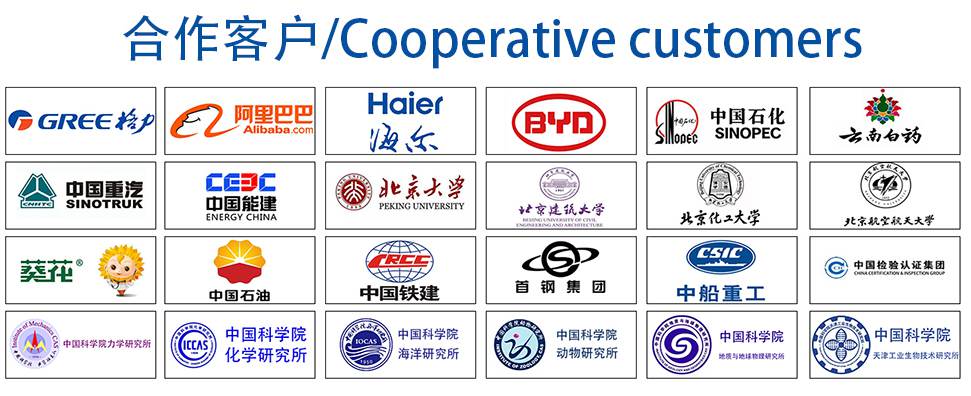