制造安装与在役质量检测的核心意义
在现代工业体系中,制造安装与在役质量检测是保障设备安全性、可靠性和使用寿命的关键环节。无论是新建设备的安装调试,还是运行中设备的定期维护,都需要通过科学系统的检测手段,确保其符合设计规范、行业标准及安全要求。随着工程复杂度的提升和智能化技术的发展,检测项目已从传统的外观检查、尺寸测量,扩展到材料性能分析、无损探伤、动态载荷测试等多维度综合评估。这一过程不仅能够预防潜在故障,更能为设备全生命周期管理提供数据支撑。
制造阶段的核心检测项目
在设备制造与安装阶段,质量检测需贯穿原材料验收、加工工艺控制及装配调试全过程。首先,材料检验涵盖化学成分分析、机械性能测试(如拉伸强度、冲击韧性)以及金相组织观测;其次,焊接工艺需通过射线检测(RT)、超声波检测(UT)等无损检测(NDT)手段验证焊缝质量;此外,关键部件的尺寸精度、形位公差需采用三坐标测量仪或激光扫描技术进行数字化验证。对于压力容器、管道系统等特殊设备,还需进行气密性试验和耐压强度测试,确保安装后的密封性和结构稳定性。
在役阶段的质量监测重点
设备投入使用后,周期性在役检测是保障持续安全运行的核心措施。此阶段需重点关注以下项目:一是腐蚀与磨损监测,通过测厚仪、内窥镜等手段评估壁厚减薄和内部缺陷;二是振动与应力分析,利用传感器实时采集设备运行时的动态参数;三是疲劳损伤检测,结合声发射技术(AE)或磁记忆检测(MMT)识别材料微观裂纹;四是电气系统的绝缘性能测试与热成像检查。对于石化、能源等高风险行业,还需建立在线监测系统(如管道SCADA系统)实现数据实时传输与预警。
检测技术的发展与标准规范
当前,检测技术正向智能化和自动化方向演进。无人机搭载红外热像仪可完成高空设备巡检,人工智能算法可快速识别X光片中的缺陷特征。同时,国际标准(如ISO 9712、ASME B31.3)和国内法规(如TSG 21-2016)对检测流程、人员资质及验收标准进行了严格规范。企业需结合设备类型、工况条件及行业要求,制定针对性的检测方案,并通过数字化平台实现检测数据的归档、分析与决策支持,从而构建完整的质量管理闭环。
结语
制造安装与在役质量检测是工业安全的重要防线,其检测项目的系统性、技术齐全性直接关系到设备运行效率与事故风险控制。未来,随着物联网、数字孪生等技术的深度融合,质量检测将逐步实现从被动排查到主动预防的转型,为工业设备的智能化运维提供更强大的技术保障。
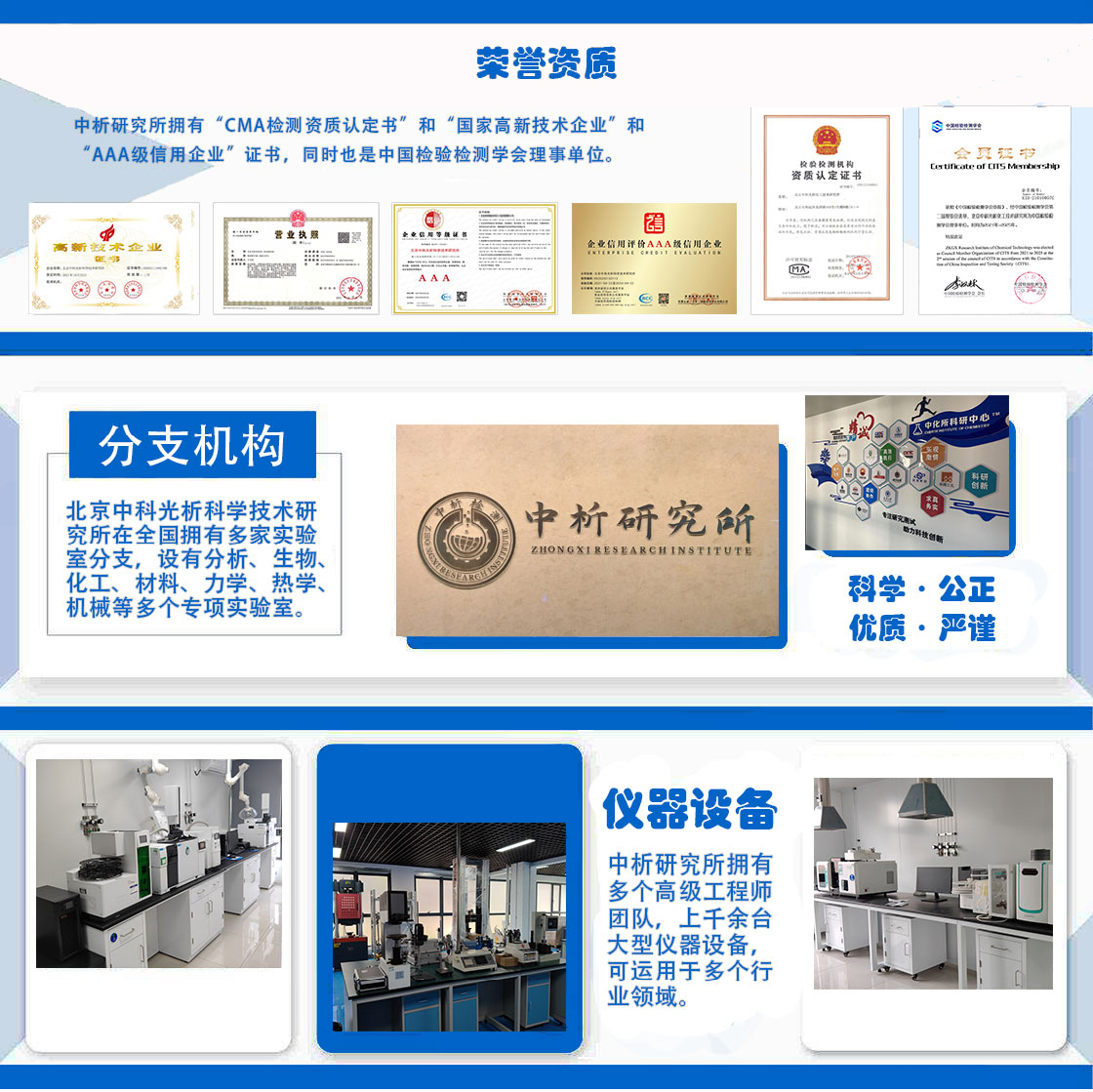
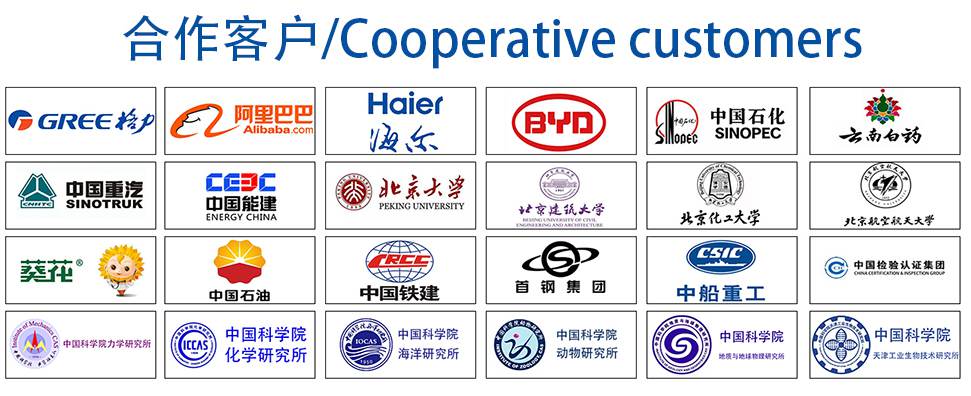