破拆机具检测的重要性与内容解析
破拆机具作为应急救援、建筑施工和灾害处置领域的核心装备,其性能直接关系到作业效率与人员安全。由于破拆机具通常面临高负荷、高频率使用场景,定期开展系统性检测是保障设备可靠性、延长使用寿命的关键环节。专业检测不仅能发现潜在故障隐患,还可通过数据化评估为维护保养提供科学依据,从而避免因设备失效导致的工程延误或安全事故。
核心检测项目分类
针对破拆机具的特性,检测项目需覆盖机械性能、安全防护和动力系统三大维度,具体可分为以下七大检测模块:
1. 动力系统检测
对液压动力单元、燃油发动机或电动机进行工况测试,包含动力输出稳定性、转速波动范围、油路/电路密封性等12项参数测量,重点关注异常振动和过热现象。
2. 液压传动检测
使用压力传感器检测液压管路工作压力,配合流量计测量油液循环效率,评估液压泵、控制阀和执行机构的同步精度,确保最大冲击力达到设计标准的98%以上。
3. 刀具组件检测
采用三维成像技术分析刀头磨损形态,测量硬质合金刀尖洛氏硬度值,同时检测刀臂结构件的抗疲劳强度,对于累计作业超500小时的刀具需进行金相组织分析。
4. 安全防护检测
验证急停装置响应时间(≤0.5秒)、过载保护触发阈值和防护罩抗冲击性能,使用模拟负载测试设备在120%额定功率下的自动停机功能可靠性。
5. 控制系统检测
通过信号发生器模拟各类工况,检测电子控制模块的信号处理精度和抗干扰能力,重点核查多模式切换时的逻辑闭锁功能,确保操作指令传输误差率低于0.3%。
6. 整机性能测试
在标准试验台架上进行连续破拆作业模拟,记录单位时间破拆效率、能耗指数和温升曲线,通过对比出厂参数判定性能衰减程度,建立设备健康状态评估模型。
7. 环境适应性检测
在高温(+60℃)、低温(-30℃)、潮湿(RH95%)等极端环境下测试设备启动性能和工作稳定性,验证密封件耐候性和金属部件的防腐蚀能力。
通过上述系统化检测流程,可建立破拆机具全生命周期管理档案。建议每季度开展常规检测,累计作业达200小时后进行深度保养检测,同时建立检测数据云端分析平台,实现设备状态的智能预警与预测性维护。
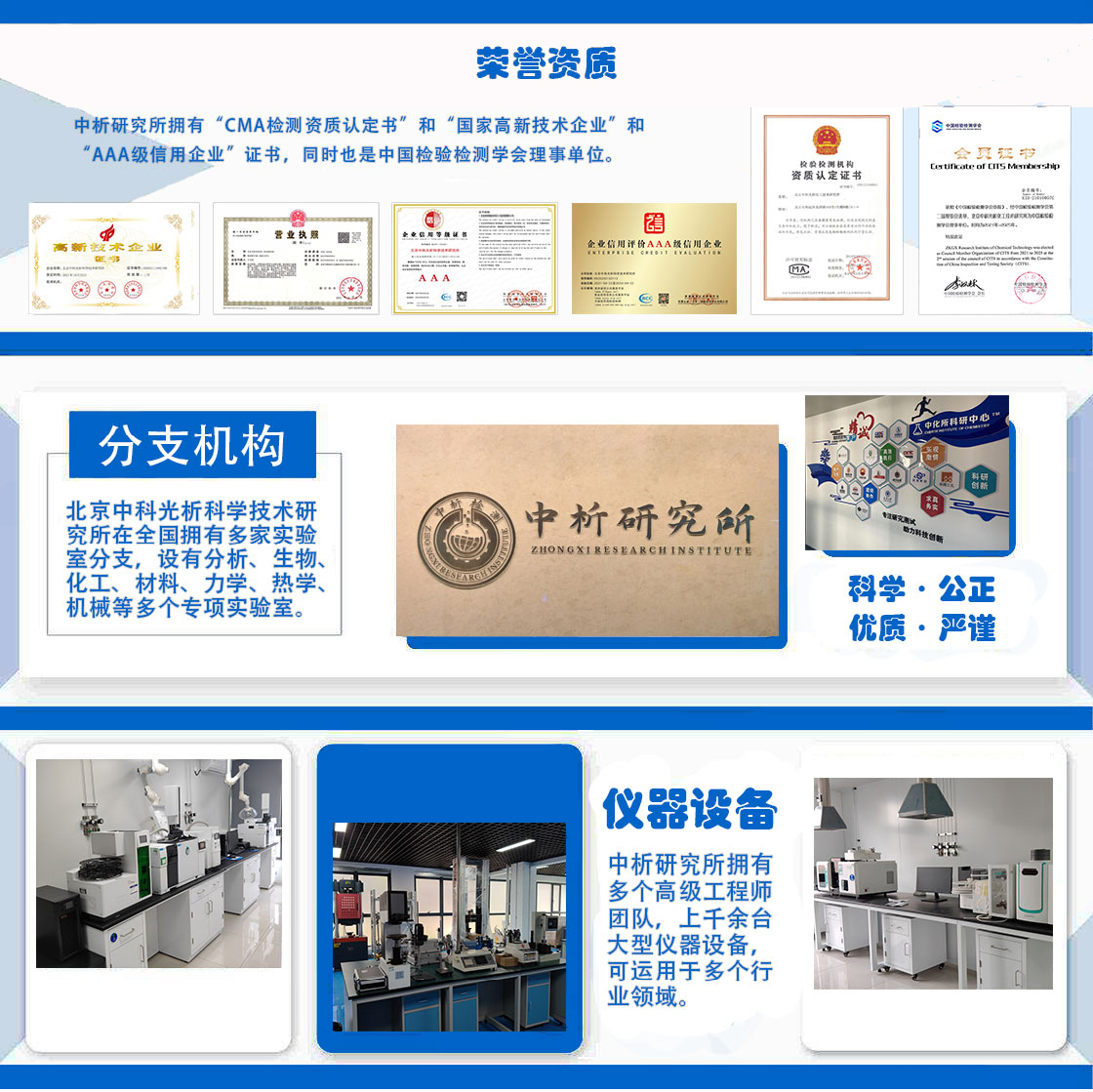
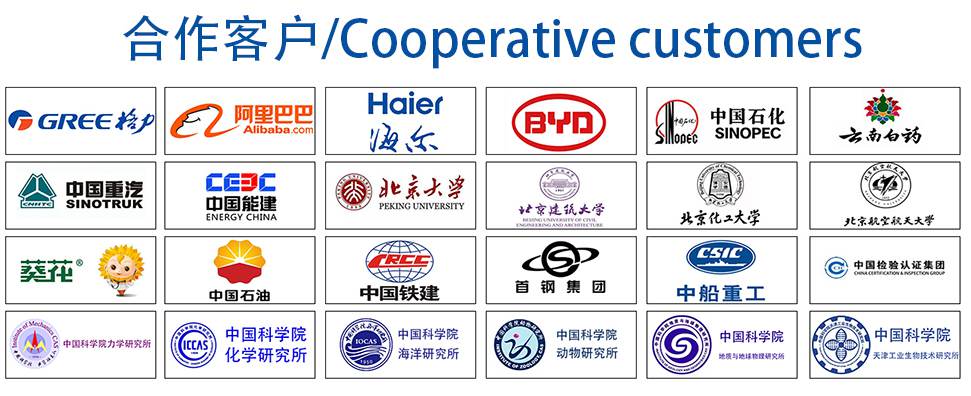