材料及制品检测的重要性及核心内容
材料及制品的检测是保障产品质量、安全性和性能的关键环节。无论是金属、塑料、陶瓷、复合材料,还是建筑构件、电子元件、医疗器械等工业制品,其物理、化学、力学及环境适应性的表现直接影响最终产品的可靠性。通过科学系统的检测手段,企业能够验证材料的合规性、优化生产工艺,同时规避因材料缺陷导致的安全风险和经济损失。随着制造业的精细化发展和国际标准的不断升级,材料检测已成为从研发到生产全流程中不可或缺的技术支撑。
核心检测项目分类
1. 物理性能检测
物理性能检测涵盖材料的密度、硬度、导热系数、导电性、热膨胀系数等基础特性。例如,通过显微硬度计测量金属表面的硬度值,可判断其抗磨损能力;利用热分析仪检测高分子材料的热稳定性,则能为高温环境下的应用提供数据支持。
2. 化学成分分析
通过光谱分析(如XRF、ICP-OES)、色谱法(GC-MS)等技术,精确测定材料的元素组成及杂质含量。例如,在合金制造中,确保镍、铬等关键元素的配比符合标准,直接影响材料的耐腐蚀性和机械强度。
3. 力学性能测试
包括拉伸试验、压缩试验、弯曲试验和冲击试验等,用于评估材料的强度、韧性、弹性模量等指标。以汽车零部件为例,动态疲劳测试可模拟长期受力环境,验证材料的耐久性。
4. 耐腐蚀性与环境适应性检测
通过盐雾试验、湿热试验、紫外线老化测试等模拟极端环境条件,分析材料在潮湿、高温、酸碱介质中的抗腐蚀能力。例如,海洋工程材料需通过长期盐雾暴露测试以验证其使用寿命。
5. 微观结构与表面分析
借助扫描电镜(SEM)、原子力显微镜(AFM)等设备,观察材料的晶粒结构、孔隙率及表面形貌。此类分析有助于揭示材料失效机制,并为工艺改进提供微观层面的依据。
6. 功能性专项检测
针对特定应用场景开展专项测试,如电子材料的绝缘性、医疗材料的生物相容性、食品接触材料的有害物质迁移量检测等。此类检测需严格遵循行业法规(如FDA、RoHS)要求。
检测技术的发展趋势
随着人工智能与物联网技术的渗透,材料检测正向自动化、智能化方向升级。例如,基于机器视觉的缺陷识别系统可实现高速在线检测;大数据平台则能整合历史检测数据,优化材料性能预测模型。未来,跨学科技术融合将进一步推动检测精度与效率的提升。
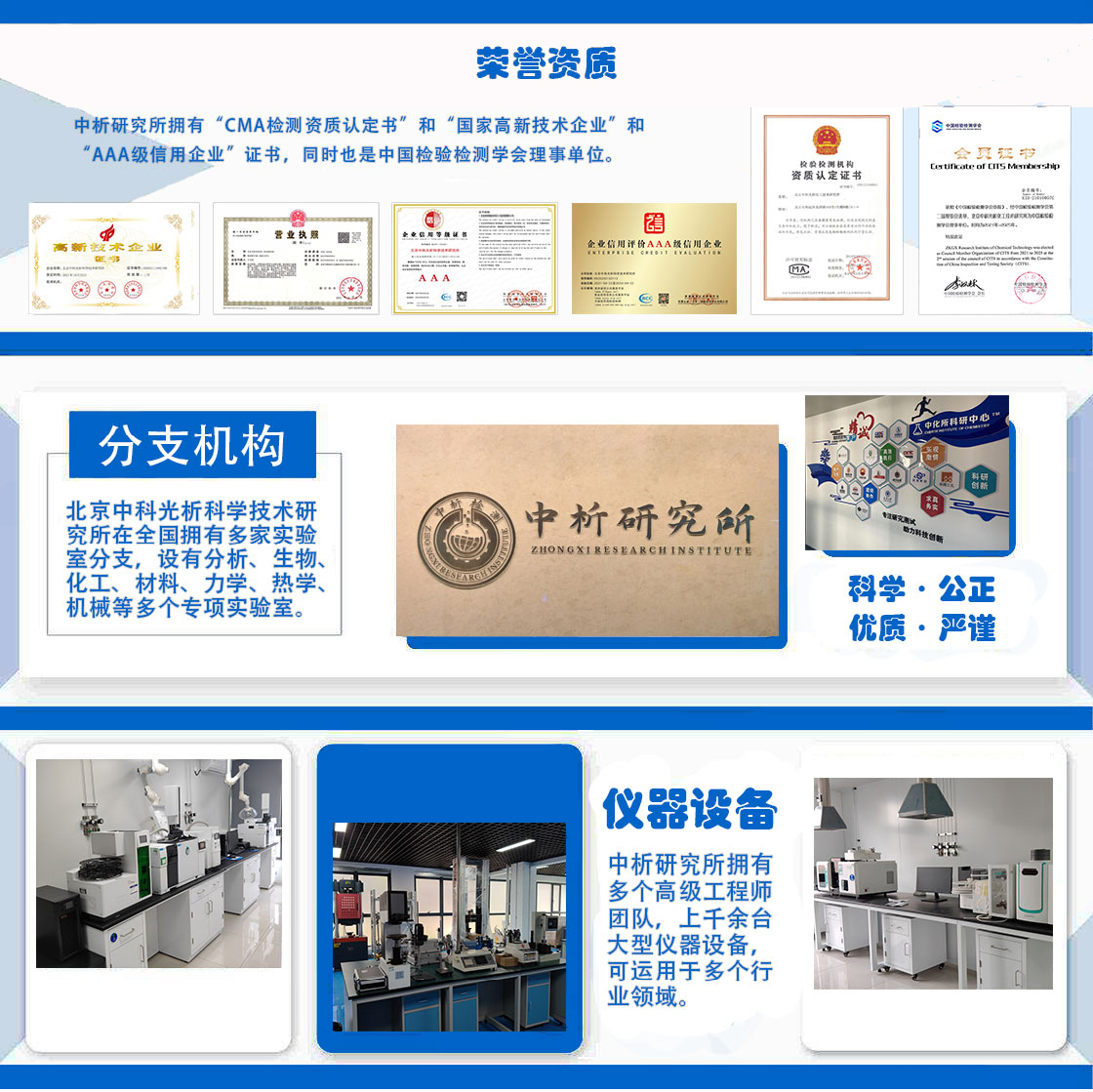
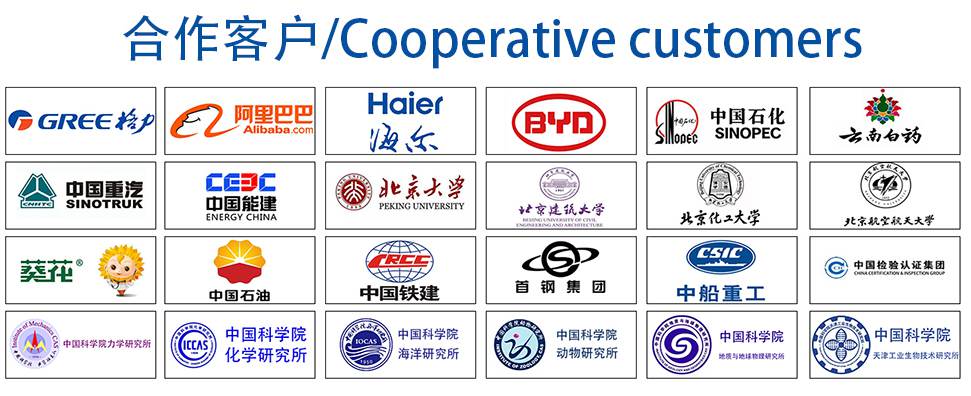