表面硫化时间检测概述
表面硫化时间检测是橡胶制品、密封材料及轮胎制造等工业领域的核心工艺控制环节,其目的是通过监测材料在硫化反应中的时间参数,确保产品达到理想的物理性能和化学稳定性。硫化过程涉及交联反应的时间控制,若时间不足会导致材料强度低、弹性差,而过度硫化则可能引发脆化或变形。现代工业中,检测项目覆盖硫化起始点判定、硫化速率分析、最佳硫化时间确定等多个维度,直接影响成品合格率和生产效率。
关键检测项目及技术要求
1. 硫化起始点检测:通过实时监测材料弹性模量变化,使用硫化仪测定扭矩上升的临界点。检测需保持温度波动≤±0.5℃,确保数据准确性。
2. 正硫化时间测定:采用MDR(移动模腔流变仪)记录扭矩平台期的持续时间,要求频率1.67Hz、振幅±0.5°的标准测试条件,重复性误差需控制在3%以内。
3. 后硫化效应评估:通过DSC(差示扫描量热法)检测残余硫化反应热,评估材料在模压后的持续交联风险,测试温度范围需覆盖-50℃至300℃。
齐全检测方法与设备应用
当前主流技术包含三类检测体系:在线红外光谱法可实时分析硫键形成程度;门尼粘度仪通过转子扭矩变化间接推算硫化进程;而基于AI的预测系统则整合温度、压力等多参数建立动态模型,实现硫化时间智能优化。新型无转子流变仪(RPA)的应用,使测试周期从40分钟缩短至15分钟,测试精度达0.1Nm。
行业标准与质量控制
检测过程需严格遵循ASTM D5289、ISO 6502等国际标准,实验室需定期进行设备校准和人员能力验证。某轮胎企业的测试数据显示,精确控制硫化时间可使产品耐磨性提升18%,动态生热降低12%,这凸显了精准检测对产品性能的关键作用。
未来技术发展趋势
随着工业4.0的推进,基于物联网的分布式检测系统正在兴起,通过部署多个微型传感器实时采集硫化数据。纳米压痕技术的引入,使得在10μm尺度上分析表面硫化程度成为可能。据统计,采用智能检测系统后,某密封件厂商的废品率从5.2%降至1.7%,验证了技术创新带来的显著效益。
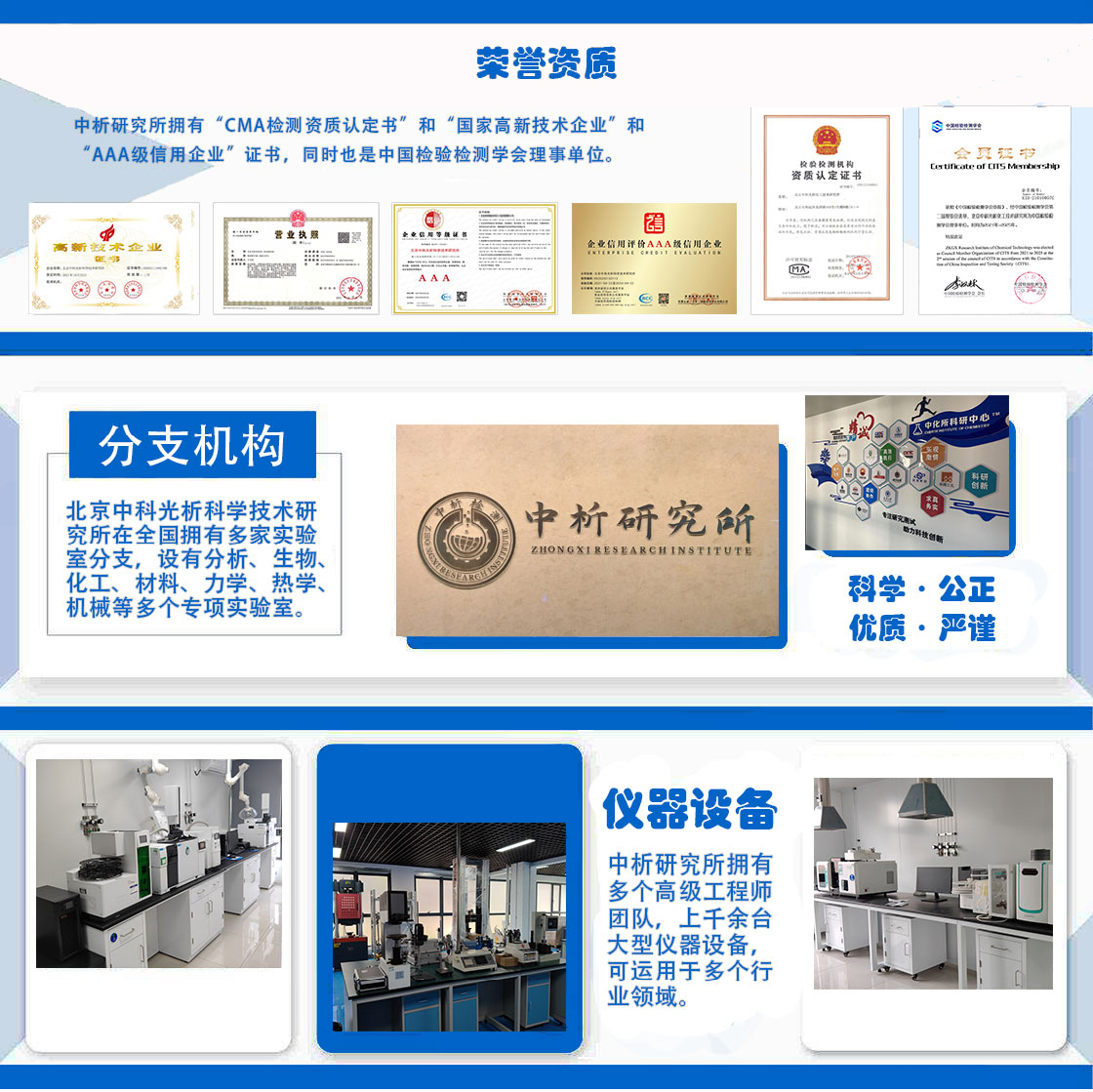
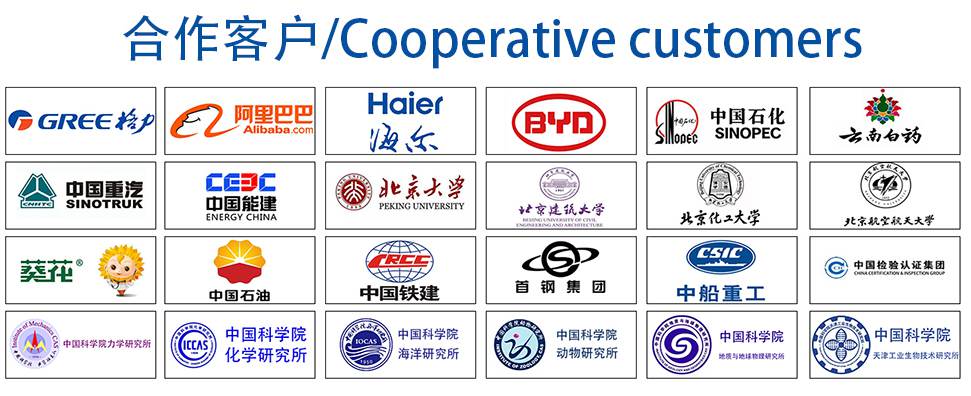