在油气钻采工程中,油管和套管作为井筒结构的重要组成部分,承担着输送油气、保护井壁、隔离地层流体的关键作用。由于长期处于高温、高压、腐蚀性介质等严酷工况下,油管和套管的完整性直接影响油气井的安全性和生产效率。据统计,每年因管材失效导致的井喷、泄漏事故造成的经济损失超百亿美元。开展系统性检测是预防失效风险、延长管材使用寿命的核心手段,涉及几何形状、材料性能、缺陷评估等多个维度的专业化检测项目。
一、几何尺寸与形变检测
通过激光扫描仪、超声波测厚仪等设备,检测管体的外径、内径、椭圆度、弯曲度等几何参数。重点检查螺纹连接部位的锥度、齿高、齿距是否符合API标准,并采用三维成像技术分析管体是否存在局部凹陷、膨胀等机械损伤。
二、壁厚与腐蚀评估
使用电磁涡流检测(ECT)或脉冲涡流(PEC)技术对管体进行全周向扫查,定位壁厚减薄区域。通过超声波相控阵(PAUT)测量剩余壁厚,结合腐蚀速率模型评估管材剩余寿命。对点蚀、沟槽腐蚀等局部缺陷进行三维形貌重建。
三、裂纹与缺陷探伤
采用磁粉检测(MT)检测表面裂纹,利用渗透检测(PT)发现开口缺陷。对于埋藏缺陷,使用全聚焦超声(TFM)或射线检测(DR)技术实现高精度成像。重点关注应力腐蚀裂纹(SCC)、氢致裂纹(HIC)等特定失效模式的特征识别。
四、材料性能测试
通过光谱分析仪验证材料化学成分,开展拉伸试验、冲击试验评估力学性能。利用金相显微镜观察微观组织,检测晶间腐蚀、脱碳等材料劣化现象。对于服役多年的管材,还需进行硬度梯度测试和残余应力分析。
五、连接密封性验证
使用气体增压装置进行气压试验,结合声发射技术监测螺纹连接处的泄漏信号。采用有限元分析模拟不同工况下的密封性能,对特殊螺纹接头进行上卸扣试验,评估重复使用后的密封可靠性。
现代检测技术已形成多维度协同检测体系,例如将智能爬行机器人(PIG)与工业CT结合,可实现整根管体的在线缺陷普查。通过建立数字化检测档案,结合大数据分析可精准预测管材剩余寿命,为油气田的智能化运维提供技术支撑。
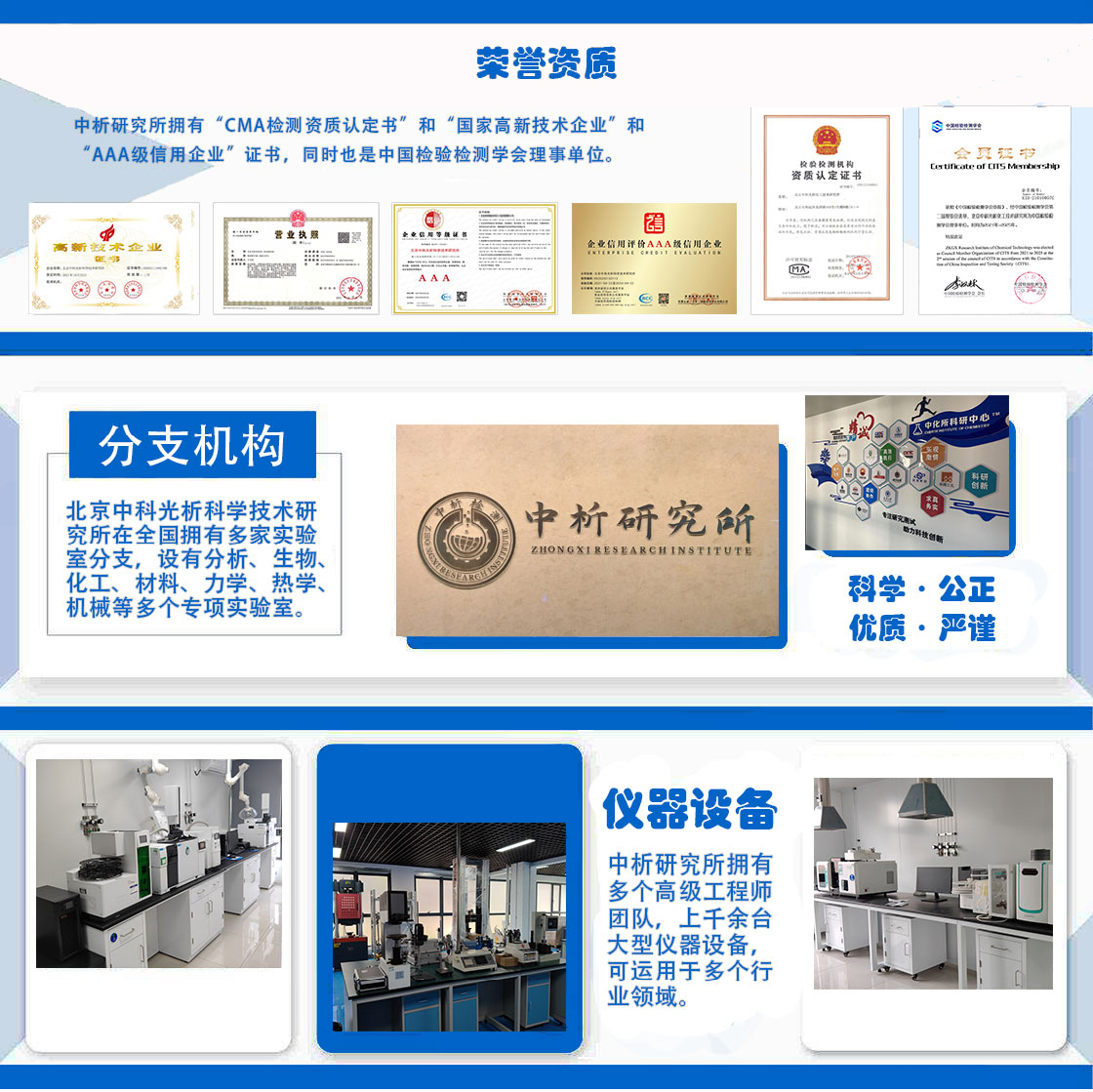
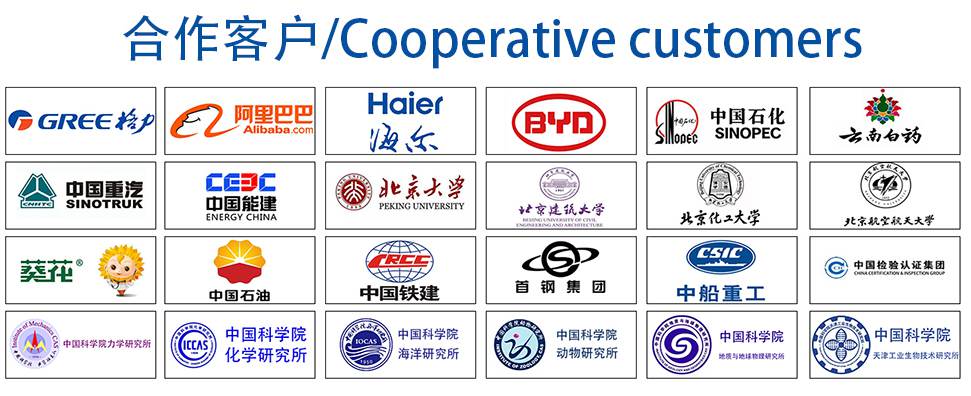