管件检测的重要性与核心内容
在石油化工、能源输送、建筑管道等工业领域,管件作为连接、转向和控制流体的关键部件,其质量直接影响着系统的安全性与使用寿命。据统计,约35%的管道事故由管件质量问题引发,因此管件检测已成为生产流程中不可或缺的环节。通过科学规范的检测手段,不仅能验证管件尺寸精度、材料强度等基础指标,更能发现潜在缺陷,避免因腐蚀、裂纹或焊接缺陷导致的泄漏、爆炸等重大风险。现代检测技术已覆盖从原材料验证到成品验收的全生命周期管理,为工程安全筑起坚实防线。
管件检测核心项目解析
1. 尺寸精度检测
使用三坐标测量仪、光学投影仪对管件的直径、壁厚、弯曲半径等关键几何参数进行微米级测量,确保符合GB/T 12459、ASME B16.9等标准要求,特别是对法兰面平行度、螺纹配合精度等装配关键部位实施100%检测。
2. 力学性能测试
通过万能试验机完成拉伸、弯曲、冲击试验,重点检测屈服强度(≥245MPa)、抗拉强度(≥415MPa)及延伸率(≥30%),模拟管件在高压、震动等极端工况下的承载能力。硬度测试采用布氏/洛氏硬度计,确保材料硬度值在HB 130-180合理区间。
3. 化学成分分析
运用直读光谱仪对碳钢、不锈钢、合金钢等材质的C、Mn、Cr、Ni等元素含量进行精确测定,比对GB/T 699、ASTM A234等标准,防止材料掺杂导致的耐腐蚀性下降。X射线荧光光谱(XRF)可实现现场快速筛查。
4. 无损检测(NDT)
采用超声波探伤(UT)检测壁厚均匀性与内部气孔,磁粉检测(MT)发现表面微裂纹,渗透检测(PT)识别0.01mm级以上开口缺陷。对于高压管件,100%实施射线检测(RT),确保焊接区域无未熔合、夹渣等缺陷。
5. 耐压与气密性试验
根据TSG D7001标准进行1.5倍工作压力的水压试验,保压时间≥30分钟。气体管路需额外进行氦质谱检漏,泄漏率控制在1×10⁻⁶ Pa·m³/s以下,特殊工况下实施-196℃深冷循环试验验证低温密封性。
6. 表面质量评估
使用表面粗糙度仪检测Ra≤3.2μm的标准,内窥镜检查内壁氧化皮残留。防腐涂层需通过划格法测试附着力(≥3级),盐雾试验验证500小时无红锈,电火花检测确保3.5kV电压下无针孔缺陷。
全过程质量管控体系
现代管件检测已形成"原料入厂-过程监控-成品检验-使用跟踪"的四级管理体系。通过MES系统实现检测数据实时上传,运用SPC统计过程控制技术分析质量波动趋势。第三方实验室 认证报告与二维码追溯系统的结合,使每件管件具备完整的"质量身份证",为工程安全提供双重保障。
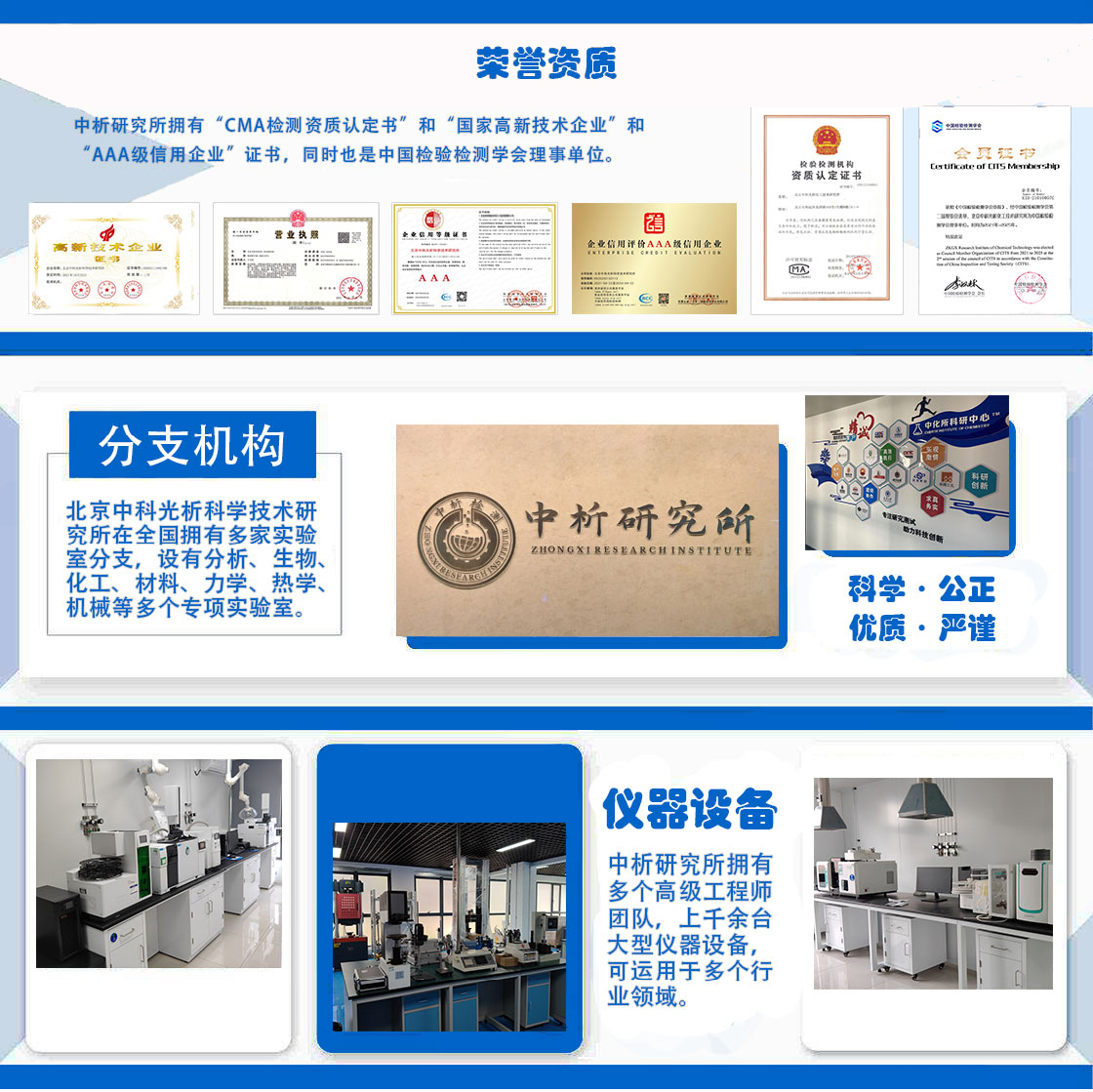
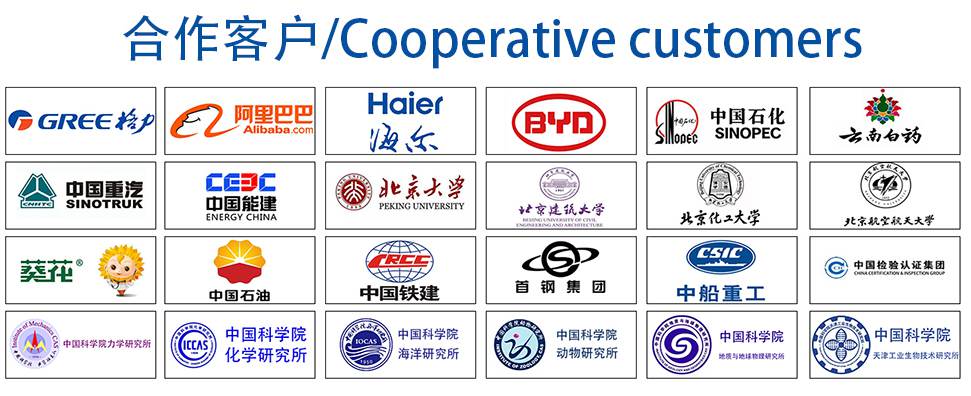