泵(参数)检测的重要性与应用场景
泵作为工业生产、水利工程、石油化工等领域的关键设备,其性能参数直接决定了系统的运行效率与安全性。泵参数检测是通过科学方法对泵的流量、扬程、功率、效率、振动、温度等关键指标进行系统性评估的过程,旨在确保设备符合设计标准、运行稳定且能耗可控。随着行业对能效和可靠性的要求日益提高,定期检测泵的性能参数已成为设备维护、故障预防及优化升级的重要环节。未达标的泵可能导致能源浪费、系统故障甚至安全隐患,因此建立规范的检测体系对保障生产安全、降低运维成本具有重要意义。
核心检测项目及方法
1. 性能参数检测
包括流量(Q)、扬程(H)、轴功率(P)和效率(η)的测定。通过流量计、压力传感器及扭矩仪等设备,结合标准测试规程(如GB/T 3216、ISO 9906),在额定工况下进行实测并绘制性能曲线。重点关注实际值与设计值的偏差是否在允许范围内。
2. 机械参数检测
涵盖振动、轴承温度、噪音等指标。使用振动分析仪、红外测温仪和声级计,检测泵体各关键部位的振动幅度、频率及温升情况。异常振动可能提示转子不平衡或轴承磨损,而温度超标则需排查润滑系统或冷却装置故障。
3. 电气参数检测
针对电机驱动的泵,需测试电流、电压、功率因数及绝缘电阻。通过电能质量分析仪和兆欧表,评估电机负载状态及绝缘性能,防止因电气故障引发设备损坏。
4. 密封性检测
检查机械密封、填料密封的泄漏量,采用目视观察结合泄漏率检测仪,确保密封系统在高压工况下的可靠性。对于化工泵,还需额外检测介质渗漏对环境的污染风险。
5. 材料与耐腐蚀性分析
通过金相显微镜、硬度计及化学分析仪,评估泵体材料(如不锈钢、铸铁)的微观结构、硬度及耐腐蚀性能,预防因材料劣化导致的失效事故。
检测标准与数据处理
检测过程需严格遵循行业标准(如API 610、ANSI/HI 9.6.7),将实测数据与设计参数进行比对,分析偏差原因。利用专业软件生成检测报告,提出改进建议,例如叶轮修正、密封更换或运行参数优化,最终实现泵效提升与寿命延长。
结语
泵参数检测是设备全生命周期管理的关键环节,通过多维度、多指标的精准测量,能够有效预防突发故障并优化能源利用效率。企业应结合工况特点制定检测计划,优先选择具备CMA/ 资质的检测机构,为泵的安全、经济和环保运行提供技术保障。
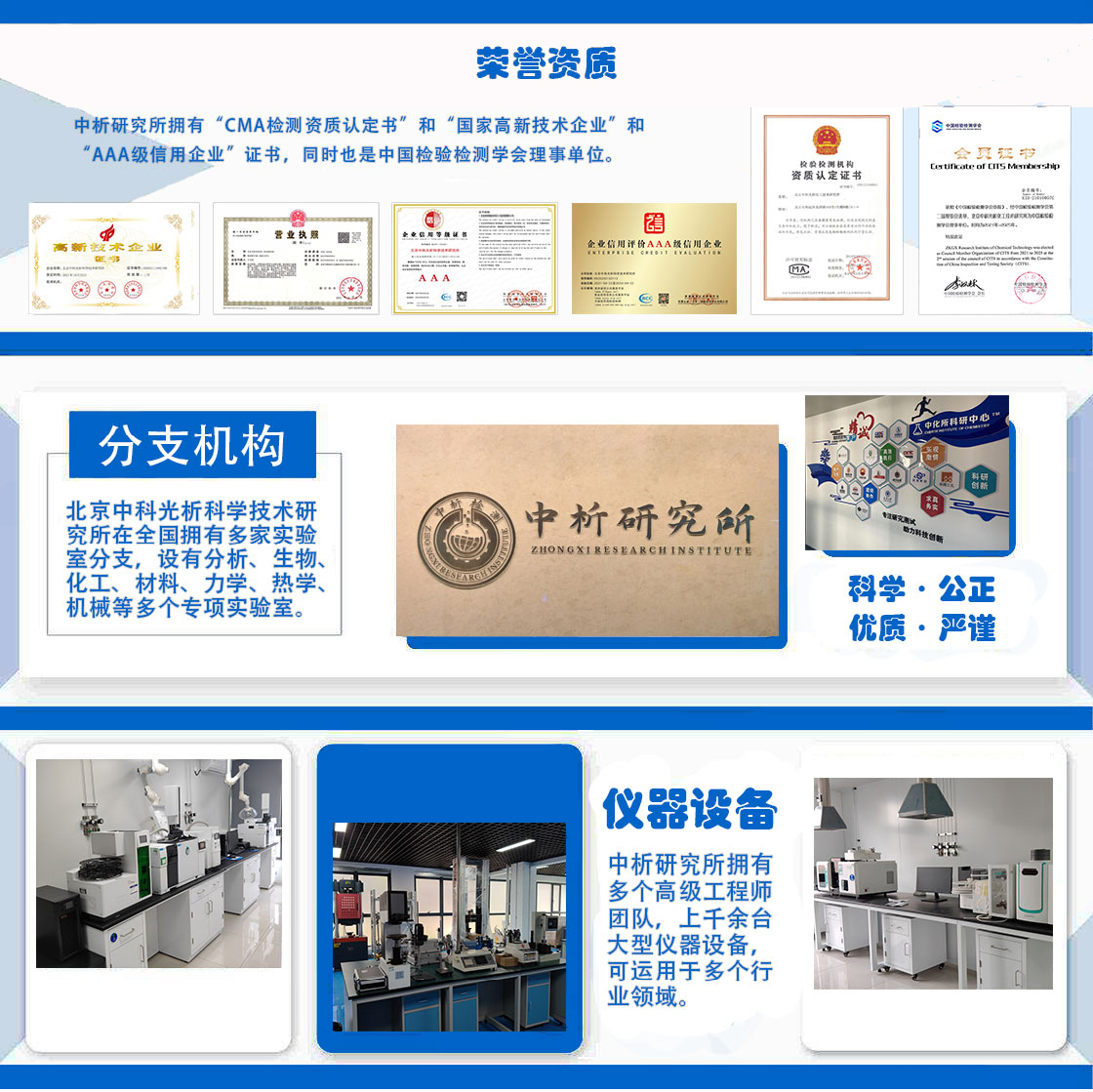
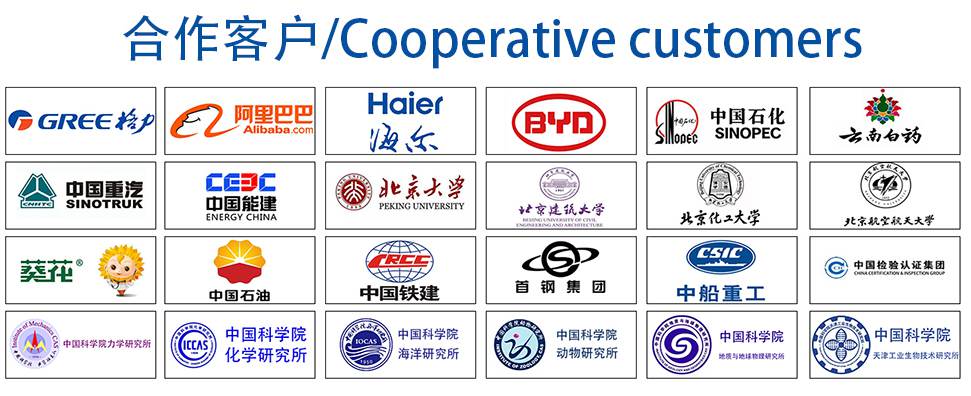