残渣燃料检测的重要性与核心指标
残渣燃料是石油炼制过程中产生的重质残留物,广泛应用于船舶动力、工业锅炉及发电领域。由于其成分复杂且含有硫化物、重金属、灰分等有害物质,残渣燃料的检测对保障设备安全运行、减少环境污染及优化燃烧效率至关重要。随着环保法规的日益严格和能源利用要求的提升,科学系统的残渣燃料检测已成为行业规范中不可或缺的环节。
残渣燃料检测的核心项目
1. 硫含量测定
硫化物是残渣燃料中的主要污染物之一,其燃烧后生成的SOx会加剧酸雨和大气污染。通过X射线荧光光谱法(XRF)或紫外荧光法测定硫含量,可评估燃料是否符合国际海事组织(IMO)的限硫规定(如硫含量上限0.50%)。
2. 粘度与流动性分析
残渣燃料在常温下呈高粘度状态,直接影响泵送、雾化和燃烧效率。检测50℃下的运动粘度(cSt)及倾点指标,可指导燃料预热温度设定,避免管路堵塞或燃烧不充分问题。
3. 灰分与金属含量检测
灰分含量反映燃料中无机杂质的总量,而钒、钠、铝等金属元素会加速设备腐蚀。通过灰分灼烧法(ISO 6245)和ICP-MS技术进行量化分析,可预测燃烧后沉积物对涡轮机、锅炉的损害风险。
4. 闪点与安全性测试
闪点直接关联燃料储存与运输的安全性。采用闭口杯法(ASTM D93)测定最低闪点温度,确保燃料在常温下不因挥发引发爆炸风险,尤其对船舶燃料舱管理具有指导意义。
5. 水分与沉积物检测
水分会降低燃料热值并促进微生物滋生,而沉积物可能堵塞过滤系统。通过离心分离法(ISO 3735)和卡尔费休法测定水含量,结合沉淀物重量分析,可评估燃料的纯净度与稳定性。
检测标准与技术要求
国际通用的检测标准包括ISO 8217(船用燃料规范)、ASTM D396(工业燃料油)及GB/T 17411(中国船用残渣燃料标准)。实验室需配备旋转粘度计、元素分析仪、高温马弗炉等专业设备,同时结合气相色谱(GC)对微量芳烃进行定性定量分析。
检测结果的应用场景
通过系统检测可优化燃料采购决策(如选择低硫低金属燃料)、制定设备维护周期(根据灰分预测积碳速度),并满足IMO 2020限硫令、MARPOL公约等法规要求。对于电厂等大型用户,检测数据还可用于计算碳排放量,支持绿色能源转型。
总结而言,残渣燃料检测是连接能源利用与可持续发展的关键技术环节。通过精准测定关键指标,不仅能延长设备寿命、降低运营成本,更能显著减少污染物排放,助力实现工业领域的环保目标。
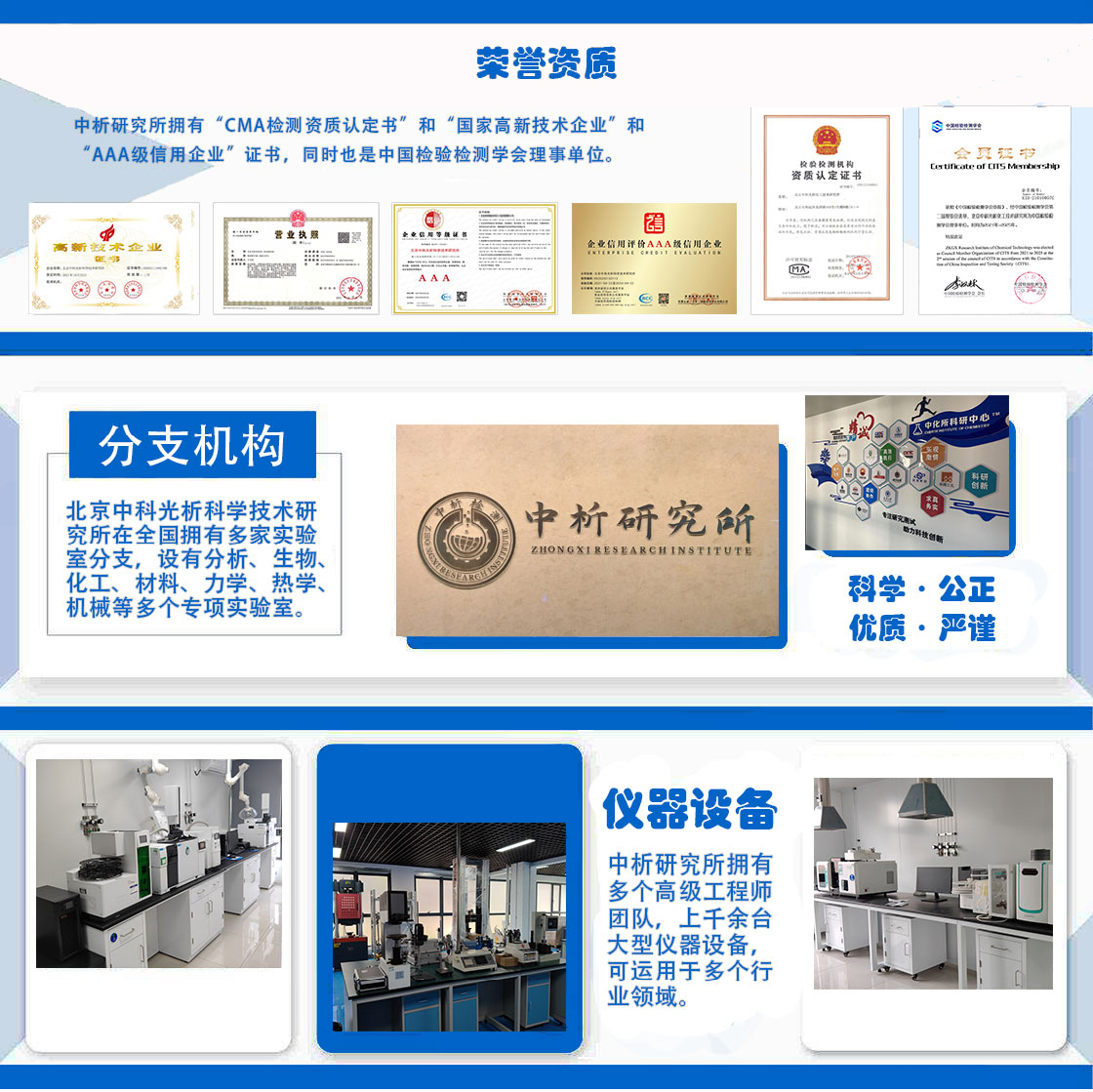
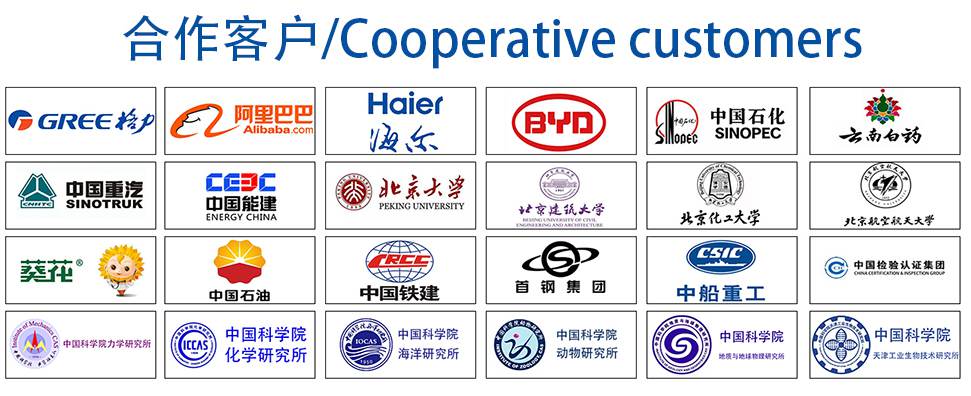