金属材料及制品(无损检测)检测的重要性
在工业制造、航空航天、能源化工、轨道交通等领域,金属材料及制品的质量直接关系到设备的安全性、可靠性和使用寿命。无损检测(Non-Destructive Testing,NDT)作为一种在不破坏材料或制品结构的前提下,对其物理性能、内部缺陷及表面状态进行检测的技术,已成为现代工业质量控制的必备手段。通过无损检测,企业能够提前发现裂纹、气孔、夹杂物等潜在缺陷,避免因材料失效引发的重大事故,同时优化生产工艺,降低生产成本。
核心检测项目与技术方法
无损检测涵盖多种技术手段,不同方法适用于不同场景和缺陷类型。以下是金属材料及制品无损检测的主要项目及其应用特点:
1. 射线检测(RT)
射线检测利用X射线或γ射线穿透金属材料,通过成像设备记录材料内部结构的变化,适用于检测焊缝、铸件中的气孔、夹渣、未熔合等缺陷。其优势在于直观呈现缺陷形态,但需注意辐射防护和操作规范。
2. 超声波检测(UT)
超声波检测通过高频声波在材料中的传播特性,分析反射波信号来定位内部缺陷的尺寸、位置和类型。该方法特别适用于厚壁容器、锻件和复合材料的检测,具有灵敏度高、检测深度大的特点。
3. 磁粉检测(MT)
磁粉检测利用磁场作用在金属表面形成磁痕,显露出铁磁性材料表面或近表面的裂纹、折叠等缺陷。其操作简便、成本低,广泛应用于轴类、齿轮等零部件的日常检验。
4. 渗透检测(PT)
渗透检测通过毛细作用使显像剂吸附于材料表面开口缺陷中,适用于非多孔性金属的表面裂纹检测。无需复杂设备,但对表面清洁度要求较高,常用于不锈钢、铝合金等非磁性材料的检测。
5. 涡流检测(ET)
涡流检测基于电磁感应原理,通过分析导电材料中涡流场的变化,检测表面及近表面的裂纹、腐蚀等缺陷。适用于管材、棒材的快速在线检测,可实现自动化操作。
6. 相控阵超声检测(PAUT)
作为超声波检测的进阶技术,相控阵超声通过电子控制声束角度和聚焦深度,显著提升检测效率和精度。尤其适用于复杂几何形状工件的检测,如焊接接头、涡轮叶片等。
检测标准与设备要求
为确保检测结果的准确性与可比性,金属材料无损检测需严格遵循国际标准(如ISO 9712、ASTM E1444)或行业规范。检测设备需定期校准,操作人员需持有专业资质证书。例如,射线检测需配备数字成像系统(DR/CR),磁粉检测需使用符合ASTM E709标准的磁化设备。
结语
随着智能制造和工业4.0的推进,无损检测技术不断向自动化、数字化方向发展。通过科学选择检测方法并严格执行标准流程,企业能够有效控制金属材料及制品的质量风险,为高端装备制造和工程安全保驾护航。
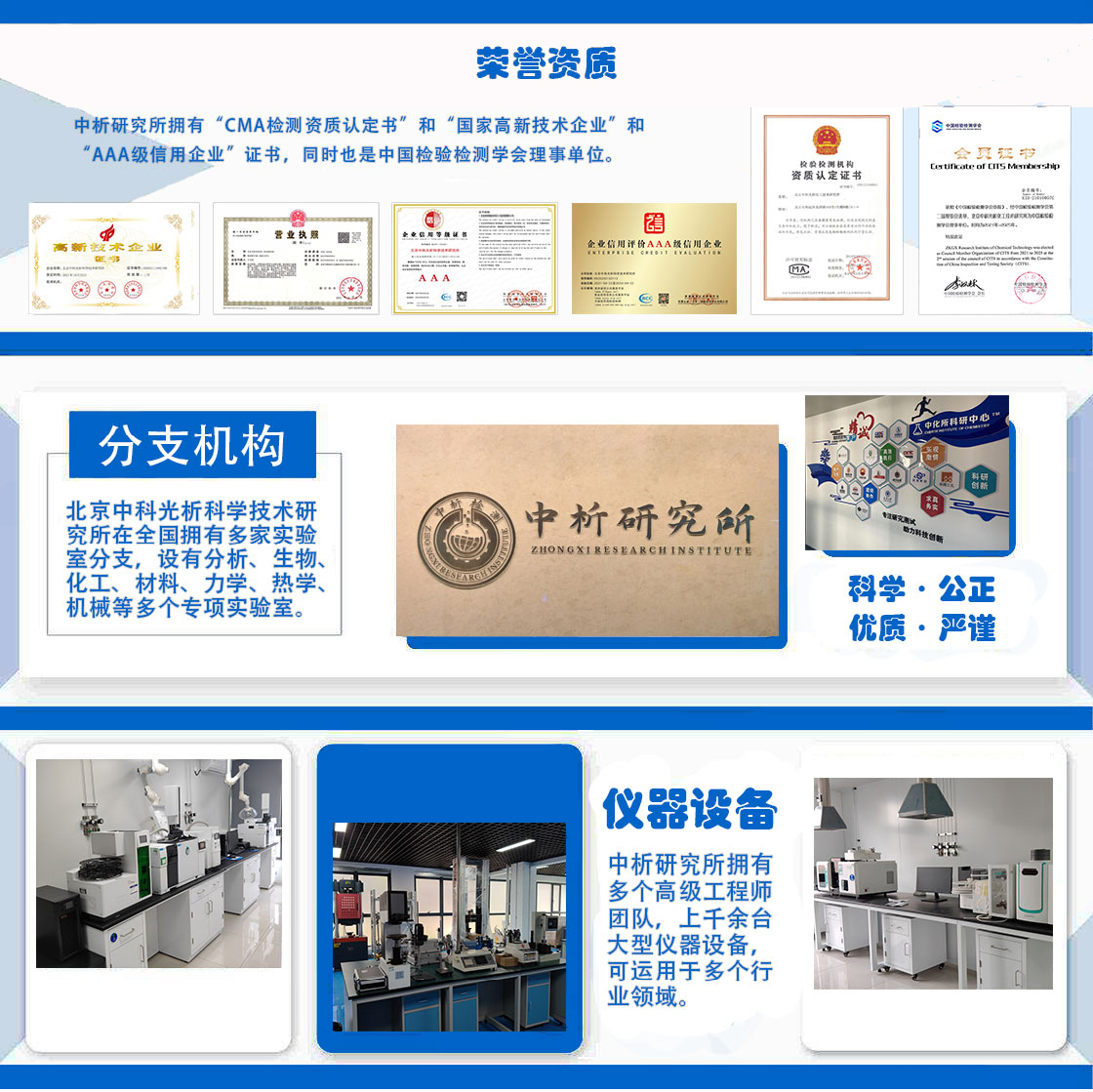
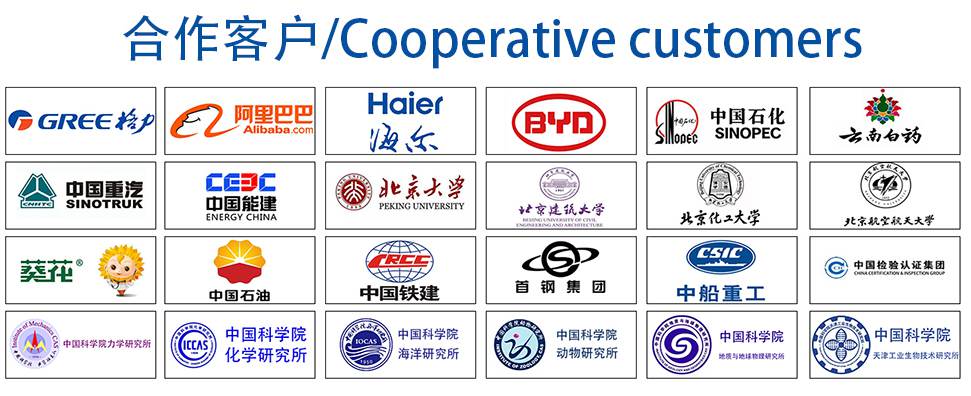