复合材料构件检测的关键技术与应用价值
复合材料因其高强度、轻量化、耐腐蚀等优异特性,在航空航天、轨道交通、新能源装备等领域得到广泛应用。随着复合材料构件向大型化、复杂化方向发展,其质量检测成为保障产品性能与安全性的核心环节。复合材料构件检测通过系统化的技术手段,可精准识别材料内部缺陷、评估结构完整性,并为工艺优化提供数据支持。当前检测技术已从传统的目视检查发展为多模态融合的数字化检测体系,覆盖构件全生命周期管理需求。
1. 结构完整性检测
采用超声相控阵(PAUT)和计算机断层扫描(CT)技术,可实现层合板、蜂窝芯结构等复杂构件的三维成像检测。其中PAUT技术对分层、脱粘缺陷的检出精度可达0.5mm,CT扫描分辨率突破20μm级,能清晰呈现纤维排布状态。同步开展的振动模态分析则通过固有频率变化评估结构刚度损失,特别适用于航空发动机叶片等动态载荷部件的检测。
2. 材料性能测试
通过万能材料试验机进行三点弯曲、层间剪切等力学性能测试,结合数字图像相关法(DIC)实时捕捉应变场分布。热机械分析(TMA)可测定材料的热膨胀系数与玻璃化转变温度,差示扫描量热法(DSC)用于树脂基体固化度检测。针对碳纤维复合材料,采用四探针法测量面内电阻率分布,评估纤维取向均匀性。
3. 缺陷智能识别
基于深度学习的X射线图像处理系统可自动识别孔隙、夹杂等典型缺陷,分类准确率超过98%。红外热像仪结合锁相热成像技术(PT)实现了对分层缺陷的无损检测,检测效率较传统方法提升5倍。最新研发的毫米波成像系统解决了碳纤维材料电磁屏蔽导致的检测盲区问题,对冲击损伤的检测灵敏度达到0.3J能量级。
4. 环境适应性验证
通过盐雾试验箱模拟海洋大气环境,评估复合材料耐腐蚀性能。湿热老化试验中采用动态力学分析(DMA)监测材料储能模量变化。针对航空航天应用,开展真空-热循环复合试验,测试构件在-196℃至300℃极端温度交变下的尺寸稳定性。紫外加速老化试验可预测材料在户外服役20年后的性能衰减规律。
5. 工艺质量评估
采用激光超声技术实时监测树脂传递模塑(RTM)工艺中的纤维浸润状态。基于光纤光栅的固化监测系统可精确控制升温速率,避免残余应力累积。针对自动铺丝工艺,开发了多光谱成像质量监控装置,可同步检测铺层角度误差(≤0.5°)、间隙/重叠缺陷(≤0.2mm)。三维光学扫描系统实现构件尺寸偏差的全场测量,精度达±15μm。
随着智能传感、数字孪生等新技术的融合应用,复合材料构件检测正朝着在线化、智能化方向发展。通过构建检测大数据平台,可实现缺陷预测、工艺优化与寿命评估的闭环管理,为高端装备制造提供更可靠的质量保障体系。
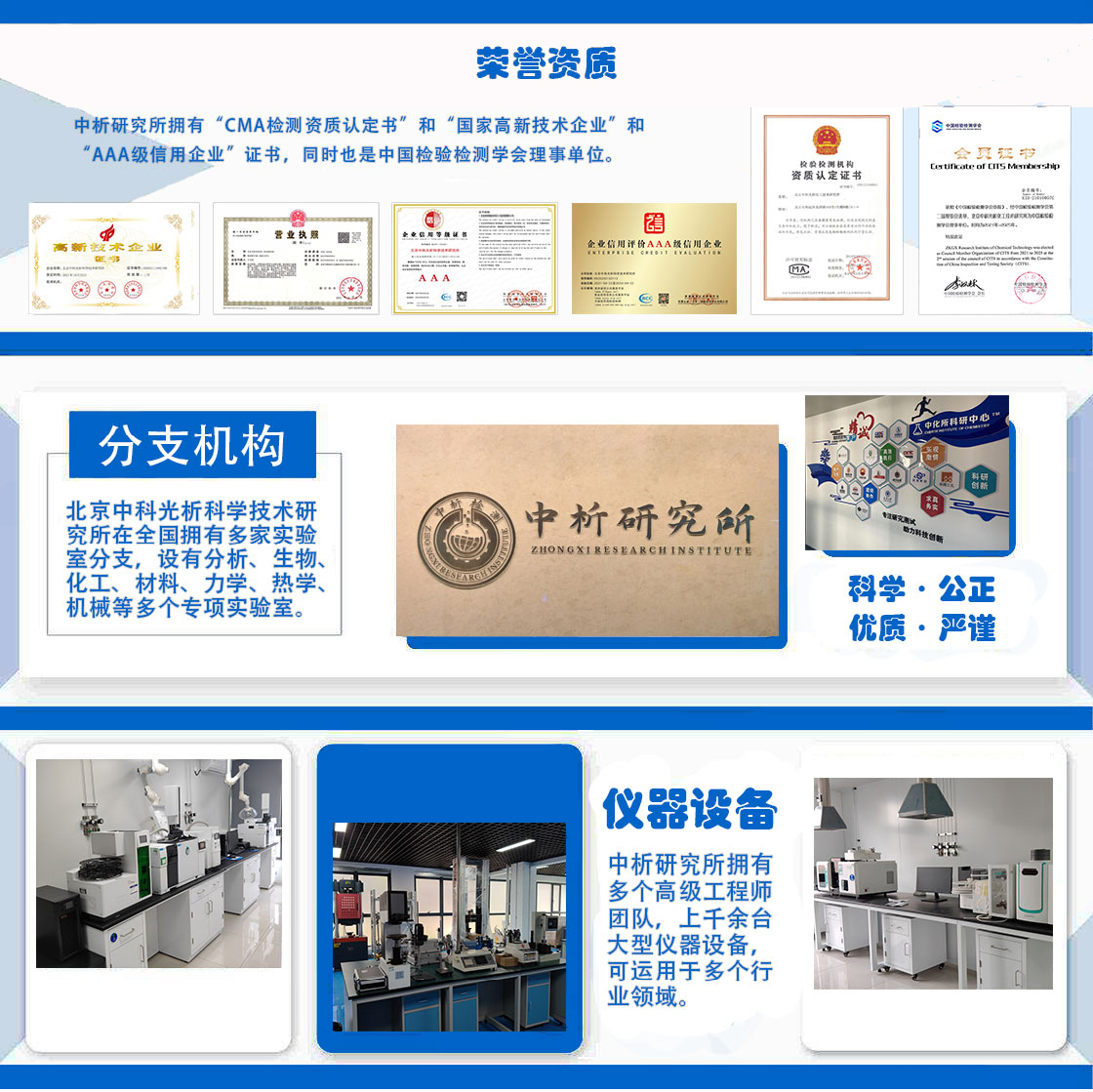
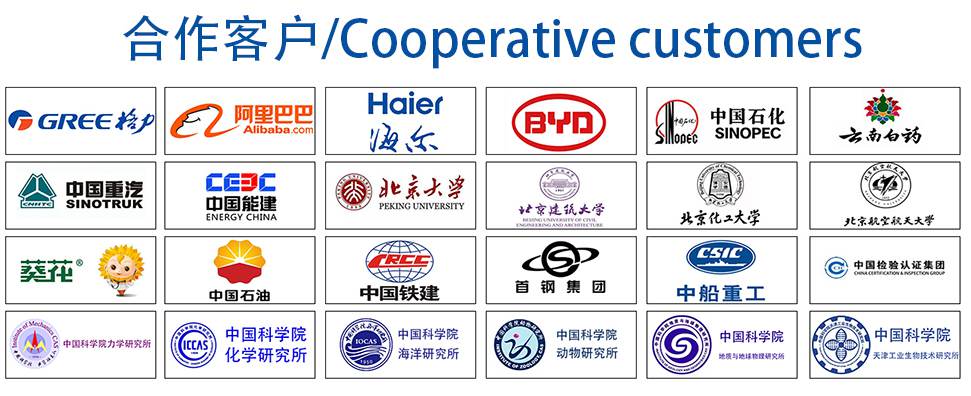