汽车用橡胶密封条检测的重要性
汽车用橡胶密封条作为整车密封系统的核心部件,承担着防水、隔音、减震及防尘等多项功能,直接影响车辆的安全性、舒适性和使用寿命。其材质通常采用三元乙丙橡胶(EPDM)、硅橡胶或PVC复合材料,需具备优异的耐候性、抗老化性和机械强度。随着汽车行业对品质要求的提升,密封条的检测项目已从单一的外观检查发展为涵盖物理性能、化学性能、环境适应性等多维度的综合测试体系。系统化的检测流程不仅能确保产品符合国家标准(GB/T)和行业规范,还能帮助车企优化供应链管理,降低因密封失效导致的售后风险。
关键检测项目及方法
1. 物理性能检测
通过拉伸试验机测定密封条的拉伸强度、断裂伸长率和永久变形率,评估其在装配和使用过程中承受应力的能力。邵氏硬度测试(Shore A)用于验证材料硬度是否满足设计需求,而压缩永久变形试验则模拟密封条长期受压后的回弹性能。
2. 耐候性测试
采用高低温交变试验箱进行温度循环测试(-40℃~120℃),验证密封条在极端环境下的抗脆化、抗收缩能力。紫外线老化试验模拟户外暴晒条件,检测材料表面龟裂、褪色及硬度变化。湿热老化测试(85℃/85% RH)则评估材料在高温高湿环境下的性能稳定性。
3. 密封性能验证
利用气密性检测装置模拟车门闭合状态,通过压力衰减法测量空气泄漏量;水密性测试则使用喷淋系统模拟暴雨场景,观察密封条对水流渗透的阻隔效果。部分高端车型还需进行风噪测试,量化密封条对车内噪音的抑制能力。
4. 环保与化学性能检测
通过气相色谱-质谱联用仪(GC-MS)分析挥发性有机物(VOC)含量,确保符合《汽车内饰件环保标准》。耐油性测试将样品浸入机油、制动液等介质,检测溶胀率变化。重金属迁移测试则依据欧盟REACH法规,防范有害物质析出风险。
5. 外观与尺寸精度控制
采用激光三维扫描仪进行截面轮廓测量,精度可达±0.05mm,确保与车体钣金件的匹配度。表面缺陷检测通过机器视觉系统识别气泡、缺料、毛边等瑕疵,同时使用色差计量化颜色一致性,避免批次间色差问题。
检测标准与行业趋势
目前主要遵循ISO 4637(橡胶密封件试验方法)、SAE J200(汽车密封条分类系统)及各大主机厂企业标准。随着新能源汽车对轻量化需求的提升,检测项目正逐步增加对低密度材料、导电密封(EMI屏蔽)等新型功能的评估,推动检测技术向智能化、高精度方向发展。
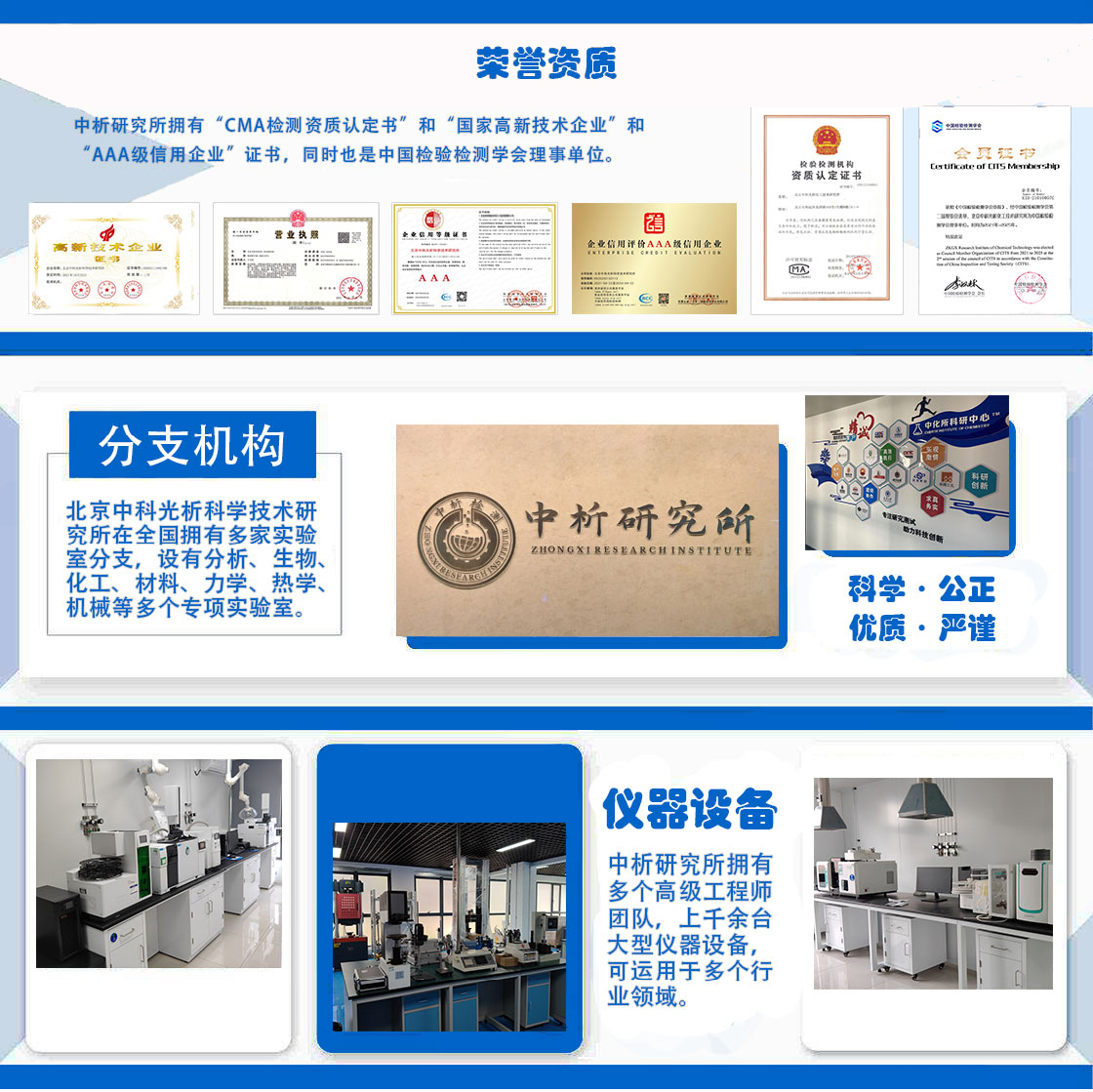
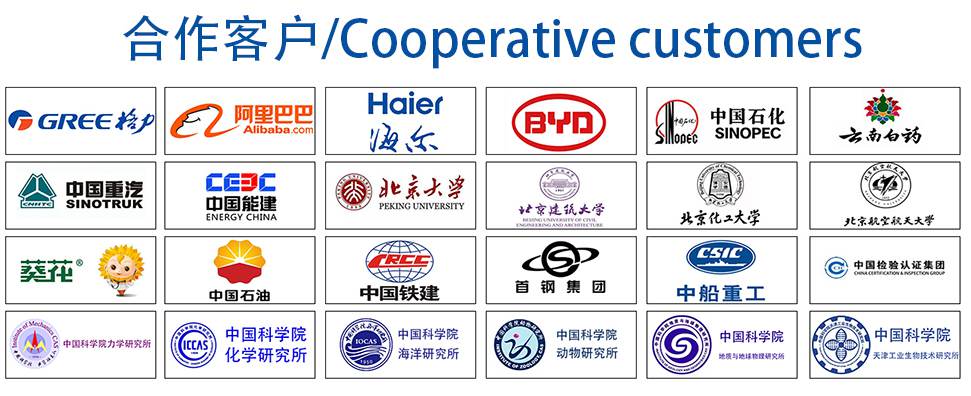