压铸模零件检测的重要性与核心内容
压铸模作为现代制造业中精密金属零部件成型的核心工具,其性能直接影响产品的尺寸精度、表面质量和生产效率。压铸模零件长期处于高温、高压、高速的极端工况下,易发生磨损、变形或疲劳失效,因此定期检测是保障模具寿命和产品质量的关键环节。压铸模零件检测不仅涉及尺寸公差、表面完整性等基础指标,还需重点关注材料性能、配合精度及功能性验证,以确保模具在连续生产中稳定运行。
压铸模零件核心检测项目
1. 尺寸精度检测
使用三坐标测量仪(CMM)或激光扫描仪对模具型腔、顶针孔、导柱导套等关键部位的尺寸进行高精度测量,确保符合设计图纸的±0.01mm误差要求。对于复杂曲面,需结合3D数模对比分析,识别局部变形或加工偏差。
2. 表面质量检测
通过渗透检测(PT)、磁粉检测(MT)或工业内窥镜检查模具表面裂纹、气孔、粘铝等缺陷。采用白光干涉仪测量表面粗糙度(Ra≤0.4μm),避免因表面粗糙导致脱模困难或产品外观不良。
3. 材料性能分析
通过金相显微镜观察模具钢的显微组织,评估热处理工艺是否达标(如H13钢的淬火马氏体比例)。利用硬度计(洛氏HRC或维氏HV)检测表面硬度(通常要求48-52HRC),并配合超声波探伤(UT)检测内部夹杂或微裂纹。
4. 配合精度验证
使用功能规或塞尺检测动模与定模的合模间隙(≤0.03mm),确保分型面密合性。对滑块、斜顶等运动部件进行装配测试,检查行程顺畅度与重复定位精度(重复误差≤0.02mm)。
5. 冷却系统检测
通过气密性试验(0.6MPa保压测试)检查冷却水道是否渗漏,利用流量计测量各回路水流量均匀性(偏差≤5%),避免因冷却不均导致模具热应力集中或产品收缩变形。
6. 涂层与表面处理检测
采用X射线荧光光谱仪(XRF)分析PVD/CVD涂层的成分与厚度(如TiN涂层8-12μm),通过划痕试验评估涂层结合强度(临界载荷≥50N),并利用摩擦磨损试验机模拟实际工况下的耐磨性能。
智能化检测技术的应用趋势
随着工业4.0的发展,在线检测系统(如CCD视觉检测)与数字孪生技术正逐步应用于压铸模监测。通过嵌入传感器实时采集模具温度、压力、振动数据,结合AI算法预测剩余寿命,实现预防性维护。这种闭环检测体系可将模具故障率降低40%以上,显著提升生产效益。
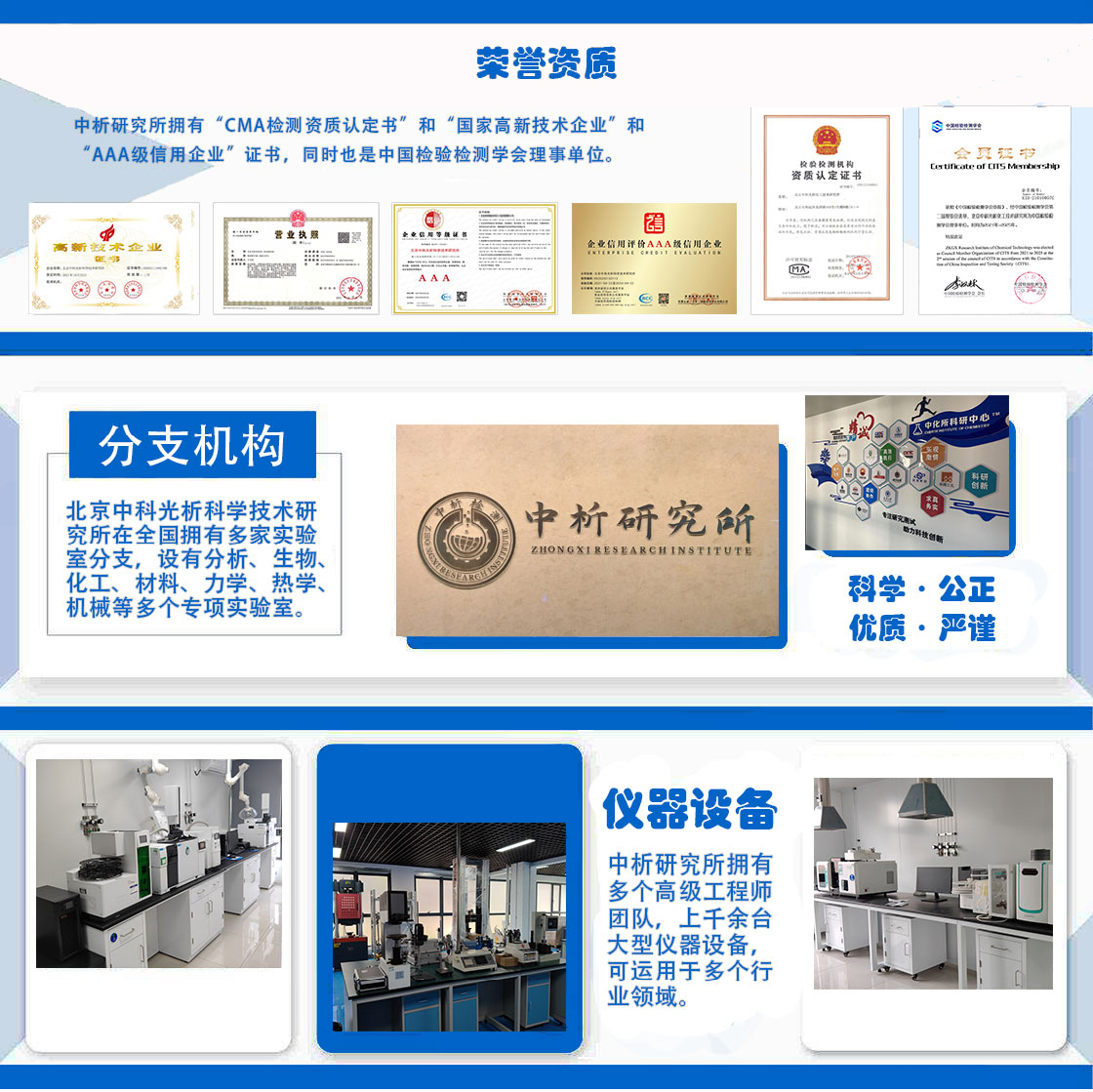
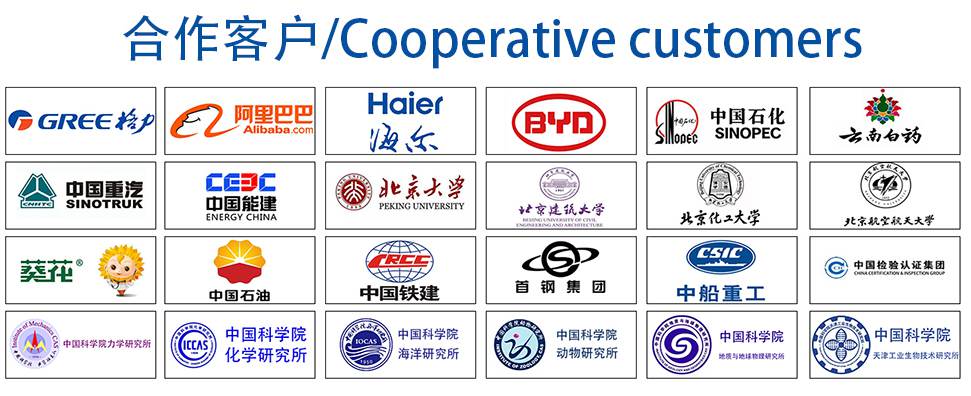