塑料异型材挤出模零件检测流程与关键技术
在塑料异型材生产过程中,挤出模具的精度和稳定性直接决定了型材产品的尺寸精度、外观质量及生产效率。针对挤出模零件的系统化检测是确保模具性能的关键环节,其检测项目需覆盖结构尺寸、表面特性、材料性能和功能适配性等多个维度。通过科学的检测手段和规范的检测流程,可有效预防因模具缺陷导致的型材翘曲、表面划痕、尺寸偏差等质量问题,同时延长模具使用寿命。
核心检测项目及技术要求
1. 尺寸精度检测
使用三坐标测量仪对模头流道宽度、定型模腔截面尺寸等关键参数进行三维测量,公差控制需满足±0.02mm的行业标准。特别关注多段组合式模具的配合间隙,要求滑动部件配合间隙≤0.05mm,固定部位配合间隙≤0.01mm。
2. 表面质量检测
采用表面粗糙度仪(Ra≤0.4μm)评估流道工作面光洁度,同时使用10倍工业放大镜目检是否存在划痕、凹坑或锈蚀。对于氮化处理零件,需通过显微硬度计验证表面硬度是否达到HV800-1000。
3. 材料性能验证
通过金相分析检测模具钢的晶粒度(要求8级以上),使用光谱仪验证材料成分是否符合H13或S7标准。对于真空热处理件,需检测表面脱碳层深度(应<0.02mm)及整体硬度梯度分布。
4. 结构强度测试
运用有限元分析软件模拟模具工作时的应力分布,实际测试中采用应变片测量关键部位的弹性变形量,要求最大变形量不超过0.1mm。对冷却水道进行3MPa水压测试,确保无渗漏且流量均衡。
5. 功能性适配检测
在模拟生产条件下进行模具试运行,使用红外热像仪监测温度场分布(温差≤5℃),通过在线测径仪实时采集型材截面尺寸波动数据。重点验证多孔模具各流道挤出速度的一致性,偏差需控制在±2%以内。
检测实施注意事项
检测环境需保持恒温(23±1℃)、恒湿(50±5%RH)状态,检测前需进行4小时以上环境适应。建议建立模具全生命周期检测档案,将初始检测数据与定期维护检测结果进行趋势分析。对于高精度异型材模具,推荐采用非接触式激光扫描与CAD模型比对技术,实现100%特征点云检测。
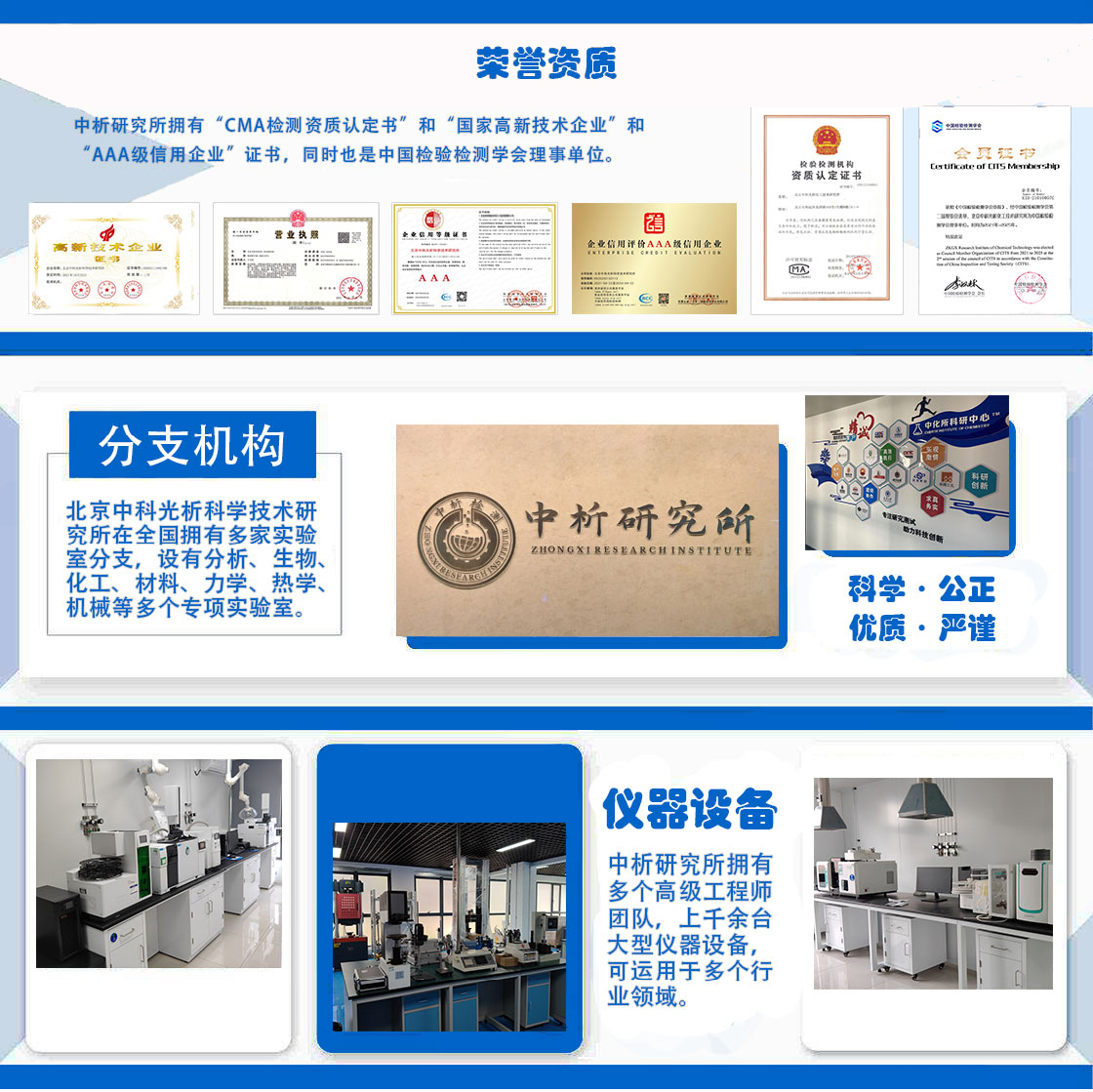
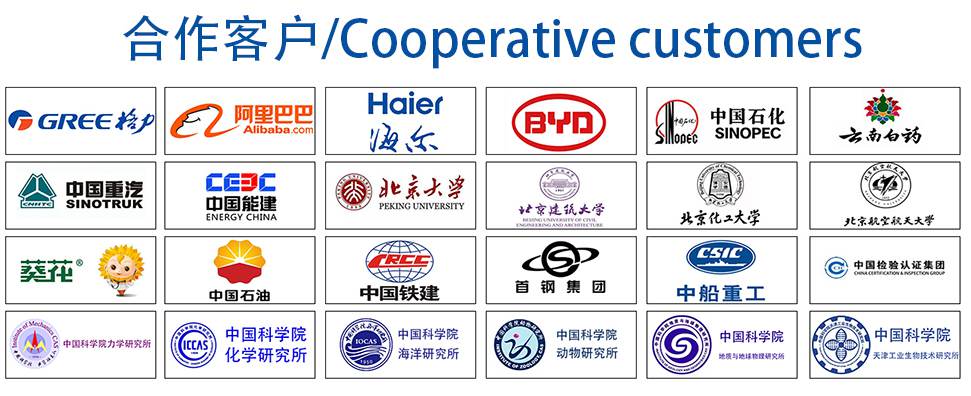