锻模检测的重要性与应用场景
锻模作为金属塑性成型的核心工具,广泛应用于汽车、航空航天、能源装备等制造领域。其质量直接关系产品精度、模具寿命及生产安全性,据统计,因锻模缺陷导致的工业事故中有72%可通过系统性检测避免。锻模检测通过科学手段对模具材料性能、几何精度、表面状态及服役性能进行全面评估,是保障锻压工艺稳定性和产品质量的关键环节。在模具全生命周期管理中,从原材料验收、热处理后检验到定期维护检测均需专业项目的支撑。
核心检测项目分类与技术指标
锻模检测体系包含四大类关键项目:材料性能检测涵盖硬度测试(HRC/HV)、冲击韧性(KV2/J)及拉伸强度(Rm/MPa);尺寸检测要求型腔公差控制在±0.05mm以内,配合三坐标测量与激光扫描技术;表面完整性检测包含粗糙度Ra≤0.8μm、裂纹检测(磁粉/渗透探伤)及残余应力分析;服役性能测试则涉及热疲劳试验(≥5000次循环)、耐磨性评估(失重率≤0.1%)等专项检测。
齐全检测技术应用进展
随着工业4.0发展,锻模检测呈现智能化趋势。三维X射线断层扫描(CT)可重构模具内部缺陷三维模型,检测精度达5μm;声发射技术实现模具服役过程中的实时状态监控,裂纹扩展检出灵敏度提高40%;基于机器视觉的表面缺陷自动识别系统,检测效率较人工提升6-8倍。这些技术突破使模具缺陷检出率从传统85%提升至98%以上。
检测标准与质量控制体系
行业检测遵循ASTM E18(硬度测试)、ISO 12107(疲劳试验)等国际标准,国内依据GB/T 13320-2018《锻模技术条件》建立质量控制体系。企业应建立包括首检、巡检、终检的三级检测制度,关键模具建议实施全尺寸检测+20%抽样复检的强化方案。通过建立检测大数据平台,可实现模具失效模式分析预测,将预防性维护效率提升30%以上。
常见问题与解决方案
针对模具龟裂问题,建议增加热疲劳试验频次并采用脉冲涡流检测技术;尺寸超差应核查热处理变形补偿参数,引入逆向工程修正技术;表面粘模现象需加强粗糙度检测,采用白光干涉仪进行纳米级表面形貌分析。通过建立检测-分析-改进的闭环管理系统,可将模具平均使用寿命延长40-60%。
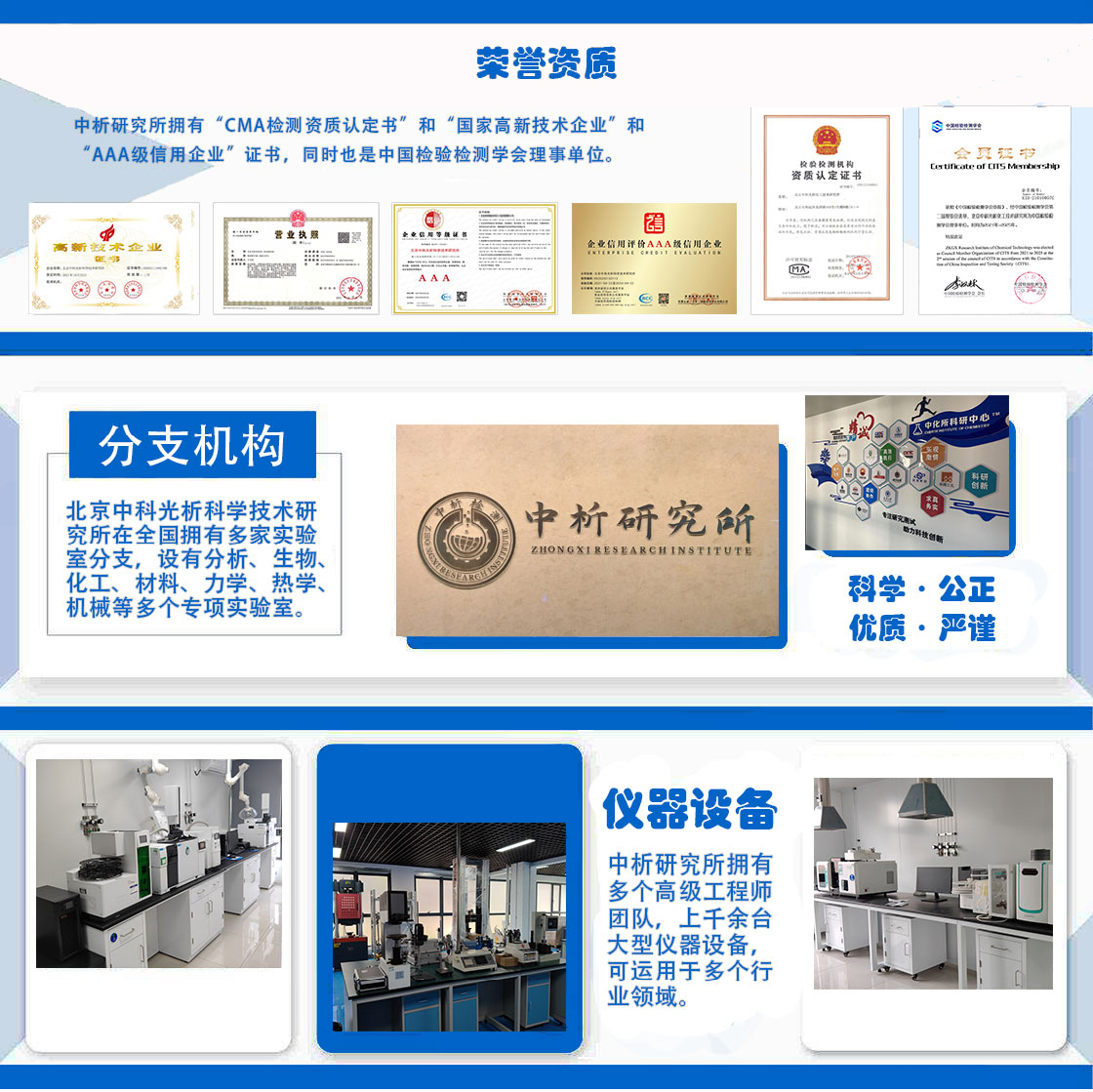
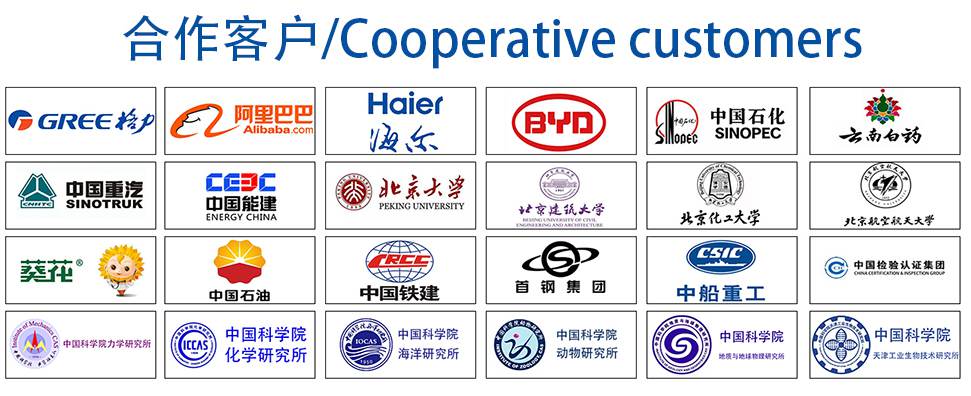