汽车用弹簧检测的重要性及核心关注点
汽车弹簧作为车辆悬挂系统、减震装置及动力传递的核心部件,其性能直接影响车辆安全性、舒适性与耐久性。在复杂工况下,弹簧需承受反复压缩、拉伸和冲击载荷,对材料的抗疲劳性、弹性模量及尺寸精度要求极高。随着汽车轻量化与电动化趋势的推进,弹簧检测项目从传统的物理性能测试向智能化、多维度分析延伸,涵盖材料学、力学、环境模拟等多个领域。行业统计显示,约15%的车辆故障与弹簧失效相关,凸显了系统性检测的必要性。
核心检测项目与技术解析
1. 材料性能检测
通过光谱分析仪检测弹簧钢的化学成分(C、Si、Mn等元素含量),使用万能试验机测试抗拉强度(≥1600MPa)、屈服强度及断后伸长率。金相显微镜观察材料晶粒度(通常要求8级以上),确保无夹杂、脱碳等冶金缺陷。
2. 尺寸精度验证
采用三坐标测量仪进行全尺寸检测,重点控制自由高度公差(±0.3mm)、弹簧外径偏差(±1%)、总圈数误差及端面平整度。对悬架弹簧需额外检测节距均匀性,偏差需控制在0.1mm/m以内。
3. 疲劳寿命测试
在电磁谐振试验机上模拟10^7次循环加载,载荷范围为设计值的20%-120%。行业标准要求200万次循环后刚度衰减≤5%,且无可见裂纹。齐全设备可同步监测温度场变化,建立疲劳寿命预测模型。
4. 表面质量评估
使用3D表面轮廓仪检测粗糙度Ra值(目标≤0.8μm),探伤仪排查微裂纹。对防腐涂层进行划格法附着力测试(0级为合格),盐雾试验需达到480小时无红锈要求。
5. 动态特性分析
在液压伺服试验台进行动态刚度测试,频率范围覆盖1-50Hz。通过模态分析获取固有频率,确保与整车共振频率错开±3Hz以上。电动车型需额外检测电磁场对弹簧特性的影响。
6. 环境适应性验证
包括-40℃低温脆性试验、150℃高温蠕变测试,以及湿热交替(85℃/85%RH)环境下的性能保持率评估。针对新能源汽车,需增加电解液腐蚀等特殊工况模拟。
智能化检测技术发展趋势
目前主流厂商已引入机器视觉自动分选系统,检测效率提升300%以上。基于大数据的预测性维护系统可通过实时监测弹簧形变量,提前预警潜在失效。未来将深度融合数字孪生技术,实现全生命周期性能仿真与优化。
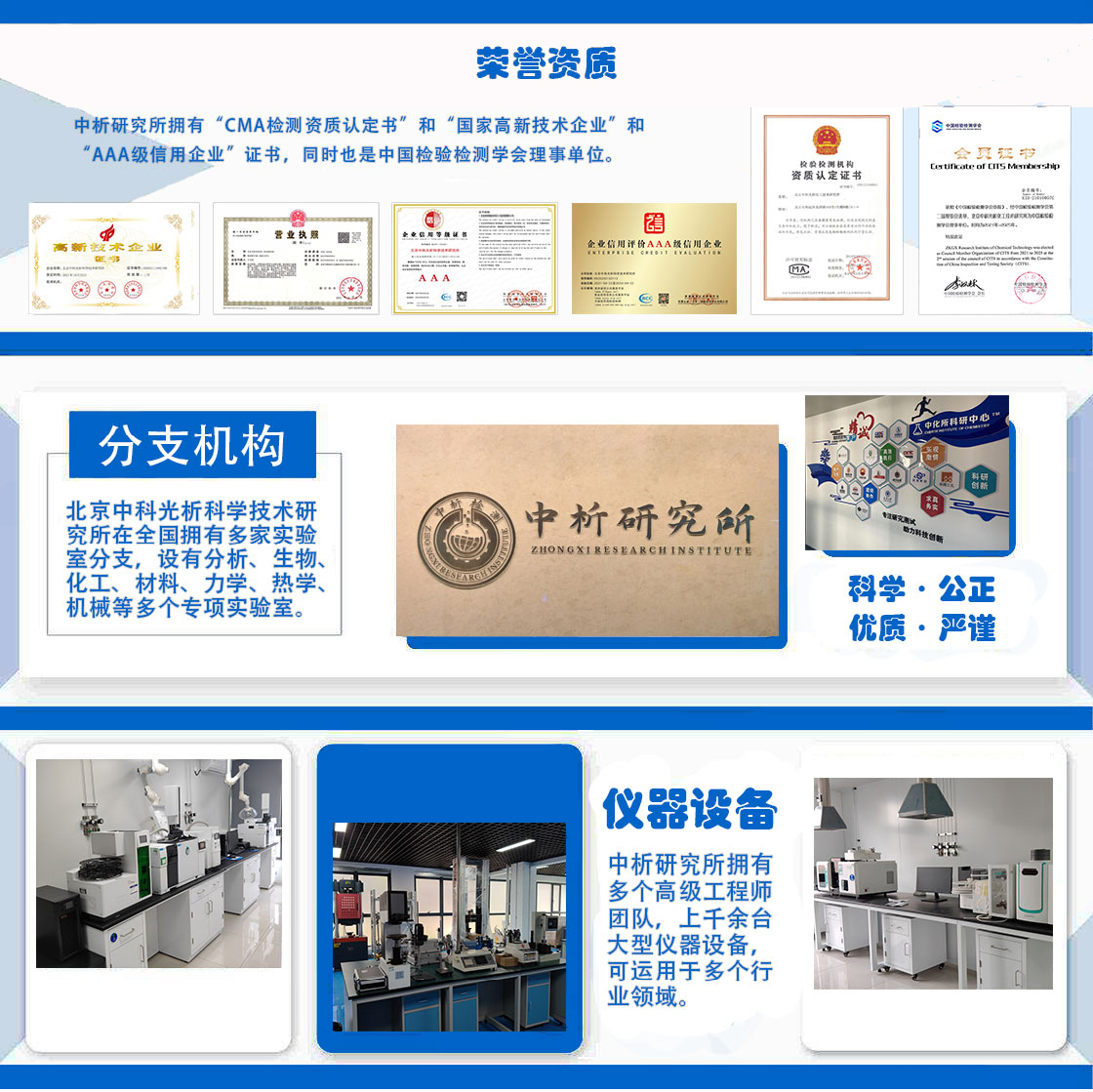
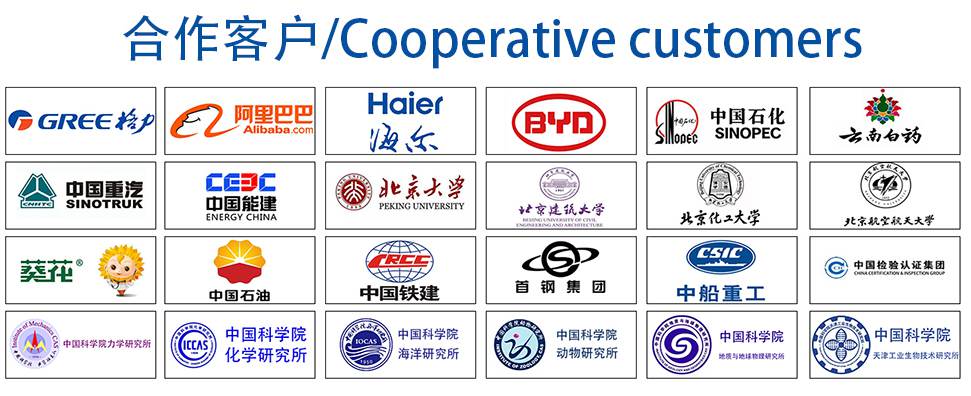