低压注塑封装用热熔胶粘剂检测
实验室拥有众多大型仪器及各类分析检测设备,研究所长期与各大企业、高校和科研院所保持合作伙伴关系,始终以科学研究为首任,以客户为中心,不断提高自身综合检测能力和水平,致力于成为全国科学材料研发领域服务平台。
立即咨询低压注塑封装用热熔胶粘剂检测的关键项目解析
低压注塑封装技术广泛应用于电子元器件、汽车电子、传感器等精密器件的保护性封装领域。热熔胶粘剂作为核心封装材料,其性能直接决定了封装件的机械强度、耐候性、密封性及长期可靠性。为确保热熔胶粘剂与基材的兼容性、工艺稳定性和最终产品性能,必须通过系统性检测项目对其物理、化学及工艺特性进行全面评估。
一、物理性能检测
1. 粘度与流动性测试:通过旋转粘度计或毛细管流变仪测量胶粘剂熔融状态下的粘度,确保其适应低压注塑工艺的充填要求。
2. 熔融指数(MI):表征胶粘剂在熔融状态下的流动速度,直接影响封装过程中胶料的分布均匀性。
3. 拉伸强度与断裂伸长率:利用万能材料试验机测试固化后胶层的机械强度,评价其抗拉伸和抗形变能力。
二、化学性能检测
1. 酸碱度(pH值):避免胶粘剂的酸性或碱性物质对封装基材(如金属、塑料)的腐蚀风险。
2. 耐溶剂性:通过浸泡实验验证胶层在特定化学溶剂中的稳定性,确保封装件在复杂环境中的耐受性。
3. 有害物质检测:依据RoHS、REACH等法规,检测卤素、重金属等有害成分含量。
三、工艺适应性检测
1. 熔融温度范围:通过DSC(差示扫描量热法)确定胶粘剂的熔融峰温度,指导注塑工艺参数设定。
2. 固化时间与收缩率:监测胶粘剂从熔融到完全固化的时间及体积变化,防止封装件因收缩应力产生缺陷。
3. 粘结强度测试:采用拉拔试验或剪切试验评估胶粘剂与不同基材(如PCB、金属外壳)的界面结合力。
四、可靠性测试
1. 高低温循环测试:模拟极端温度环境(-40℃~150℃)下的封装结构稳定性。
2. 湿热老化试验:在85℃/85%RH条件下加速老化,评估胶层的防潮性能和长期耐久性。
3. 振动与冲击测试:验证封装件在机械应力下的抗疲劳性能,确保其在汽车、航空航天等领域的适用性。
五、电学性能检测
1. 体积电阻率与介电强度:检测胶层的绝缘性能,防止漏电或短路问题。
2. 介电常数与损耗因子:针对高频电子元件封装,评估胶粘剂对信号传输的影响。
通过上述多维度的检测项目,可全面把控低压注塑封装用热熔胶粘剂的综合性能,为优化配方设计、提升封装工艺质量提供数据支撑,最终保障终端产品的可靠性与使用寿命。
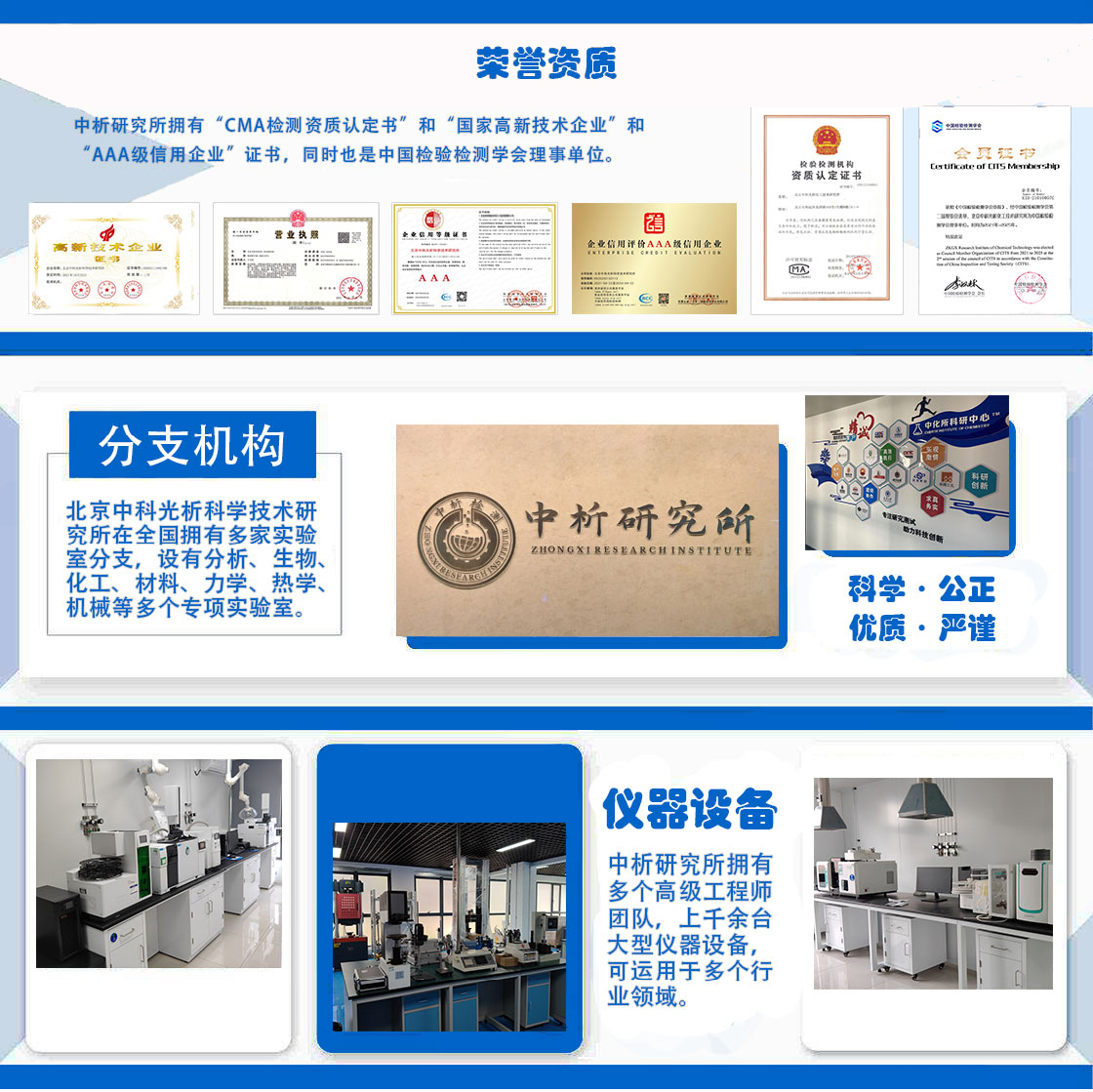
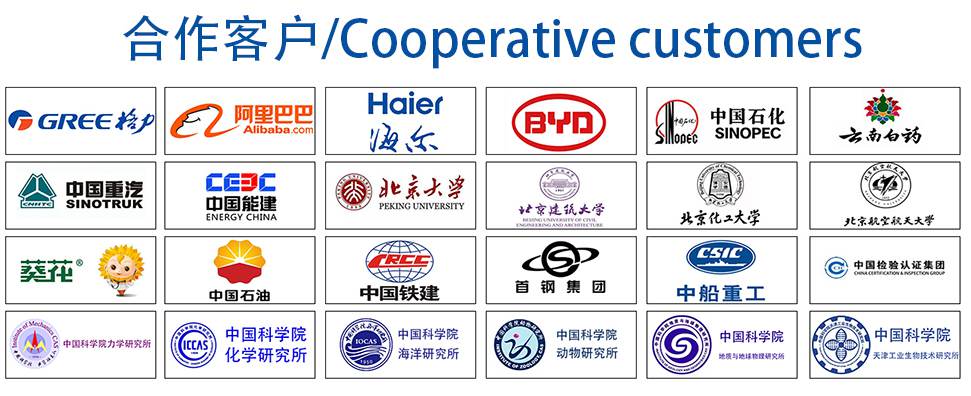