非腐蚀性气体输送用管线管内涂层检测
实验室拥有众多大型仪器及各类分析检测设备,研究所长期与各大企业、高校和科研院所保持合作伙伴关系,始终以科学研究为首任,以客户为中心,不断提高自身综合检测能力和水平,致力于成为全国科学材料研发领域服务平台。
立即咨询非腐蚀性气体输送用管线管内涂层检测的重要性
在非腐蚀性气体(如天然气、氮气、惰性气体等)输送过程中,管线管内涂层的主要功能是提升流体传输效率、减少摩擦损失,并防止管道内壁因长期摩擦或气体杂质引起的轻微磨损。尽管气体本身不具备强腐蚀性,但涂层若存在缺陷或失效,仍可能导致管道寿命缩短、维护成本增加,甚至引发微小泄漏风险。因此,对管线管内涂层进行系统化检测是保障输送安全、延长管道使用寿命的重要环节。
核心检测项目及方法
针对非腐蚀性气体输送用管线管内涂层的检测,需重点关注以下关键项目:
1. 涂层外观完整性检测
通过目视检查或内窥镜技术,评估涂层表面是否存在裂纹、气泡、剥落或异物嵌入等缺陷。对于长距离管线,可采用智能清管器(PIG)搭载高清摄像设备进行全管段扫描,确保涂层整体均匀性。
2. 涂层厚度测量
使用磁性测厚仪或超声波测厚仪,在管道内壁随机选取多点进行厚度检测。要求涂层厚度符合设计规范(通常为200-500μm),且同一区域内厚度波动不超过±10%。
3. 附着力测试
通过划格法(ASTM D3359)或拉拔试验(ASTM D4541)评估涂层与基材的结合强度。非腐蚀性环境下的附着力应达到≥5MPa,确保涂层在气体压力波动下保持稳定。
4. 孔隙率检测
采用低压湿海绵法(ISO 29601)或高压电火花检测仪,检查涂层是否存在贯穿性孔隙。对于非腐蚀性气体管线,孔隙率须严格控制在≤3个/平方米的范围。
5. 耐磨性与硬度测试
通过泰伯磨耗试验(ISO 5470)和邵氏硬度计(ASTM D2240)评估涂层的机械耐久性,确保其能承受气体流动产生的持续摩擦及可能的固体颗粒冲刷。
6. 耐化学性验证
尽管输送介质为非腐蚀性气体,仍需模拟管道运行温度下的耐水汽、微量酸性杂质(如H2S)等环境,通过浸泡试验或盐雾试验观察涂层是否出现软化或渗透现象。
检测频次与质量控制
建议在新管线投产前进行全项目检测,运行阶段每3-5年结合智能清管器进行在线监测。对于检测出的局部缺陷,需采用专用修补材料进行针对性修复,并通过复检确认修复效果。通过系统化的检测流程,可有效保障非腐蚀性气体输送管线的高效、安全运行。
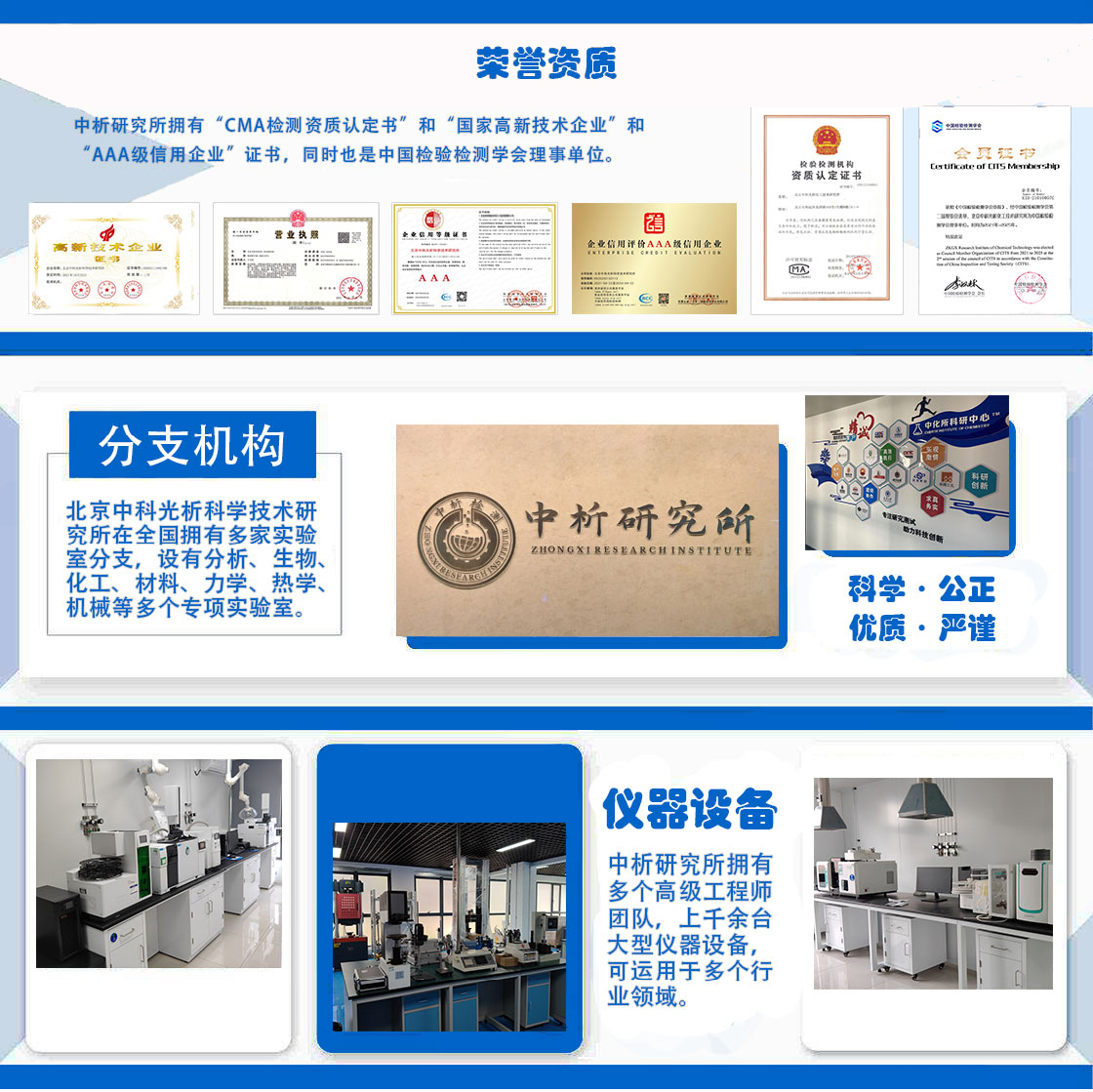
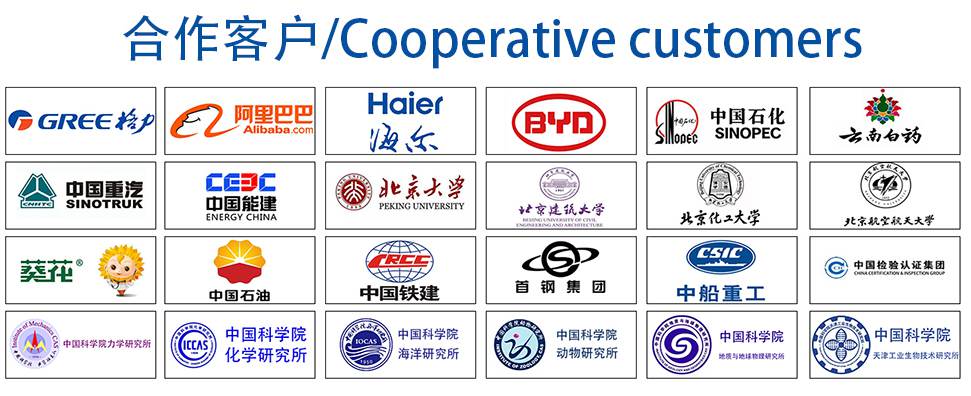