铁路货车承载鞍及弹性定位件检测概述
铁路货车作为货物运输的核心装备,其转向架系统的稳定性直接关系到列车运行安全与效率。承载鞍和弹性定位件作为转向架的关键部件,承担着传递载荷、缓冲振动及定位轮对的重要功能。承载鞍通过机械连接将车体重量均匀分布到轮轴上,而弹性定位件则通过橡胶或高分子材料的弹性变形吸收轨道冲击能量,维持轮对几何位置的稳定性。随着铁路货车运行里程增加、载重压力提升以及复杂环境的影响,这些部件易出现疲劳裂纹、塑性变形、老化失效等问题。因此,开展系统化、标准化的检测工作成为保障铁路货运安全的核心环节。
核心检测项目及技术要点
1. 承载鞍检测项目:
• 尺寸精度检测:使用三维激光扫描或专业量具测量鞍面圆弧半径、导框间隙等关键尺寸,误差需控制在±0.5mm以内
• 裂纹缺陷检测:采用磁粉探伤(MT)或超声波探伤(UT)技术排查表面及内部裂纹,重点检查应力集中区域
• 磨损量评估:通过对比原始图纸数据,测量鞍体与侧架接触面的磨损深度,单边磨损超过3mm需强制更换
• 材料性能测试:抽样进行硬度测试(HBW)、冲击韧性试验,确保材料未发生脆化或强度衰减
2. 弹性定位件检测项目:
• 橡胶层老化检测:使用邵氏硬度计测量橡胶硬度变化,对比初始值偏差超过15%判定失效
• 金属骨架腐蚀检测:采用工业内窥镜观察内部结构,结合测厚仪检查钢板锈蚀程度
• 压缩永久变形测试:通过压力试验机模拟长期载荷,变形量超过标准值20%即需更换
• 粘接强度试验:使用拉力试验机检测橡胶与金属界面的剥离强度,确保不低于5MPa的行业标准
齐全检测技术应用
当前行业正推进智能化检测转型,包括:
• 数字图像处理技术:通过高精度CCD相机捕捉部件表面状态,AI算法自动识别微裂纹
• 动态特性检测系统:利用激振设备测试弹性定位件在不同频率下的动态刚度曲线
• 在线监测装置:安装光纤传感器实时监测承载鞍应力分布状态
• 三维重建比对:基于点云数据建立数字化模型,实现服役件与设计模型的毫米级偏差分析
检测标准与周期管理
严格执行TB/T 3475.1《铁路货车转向架技术条件》和GB/T 21563《轨道交通装备可靠性、可用性、可维修性和安全性规范》要求,建立三级检测体系:
• 日常检查:每次编组作业时进行目视检查(周期≤72小时)
• 定期检测:结合年修/段修计划开展全面检测(周期1-2年)
• 状态修检测:基于大数据分析的预测性维护体系,实现关键部件的全生命周期管理
常见问题与处理建议
典型故障案例表明:
• 承载鞍裂纹多发生于导框转角处,建议采用圆角强化工艺
• 弹性定位件早期失效多因橡胶配方问题,应加强原材料入厂检测
• 冬季低温环境下弹性元件性能下降明显,需针对性调整检测阈值
• 重载列车建议缩短50%检测周期,并增加动态特性检测项目
通过构建涵盖设计验证、生产质检、运用维护的全流程检测体系,可有效提升铁路货车关键部件的可靠性,为新时代重载铁路运输安全提供坚实保障。
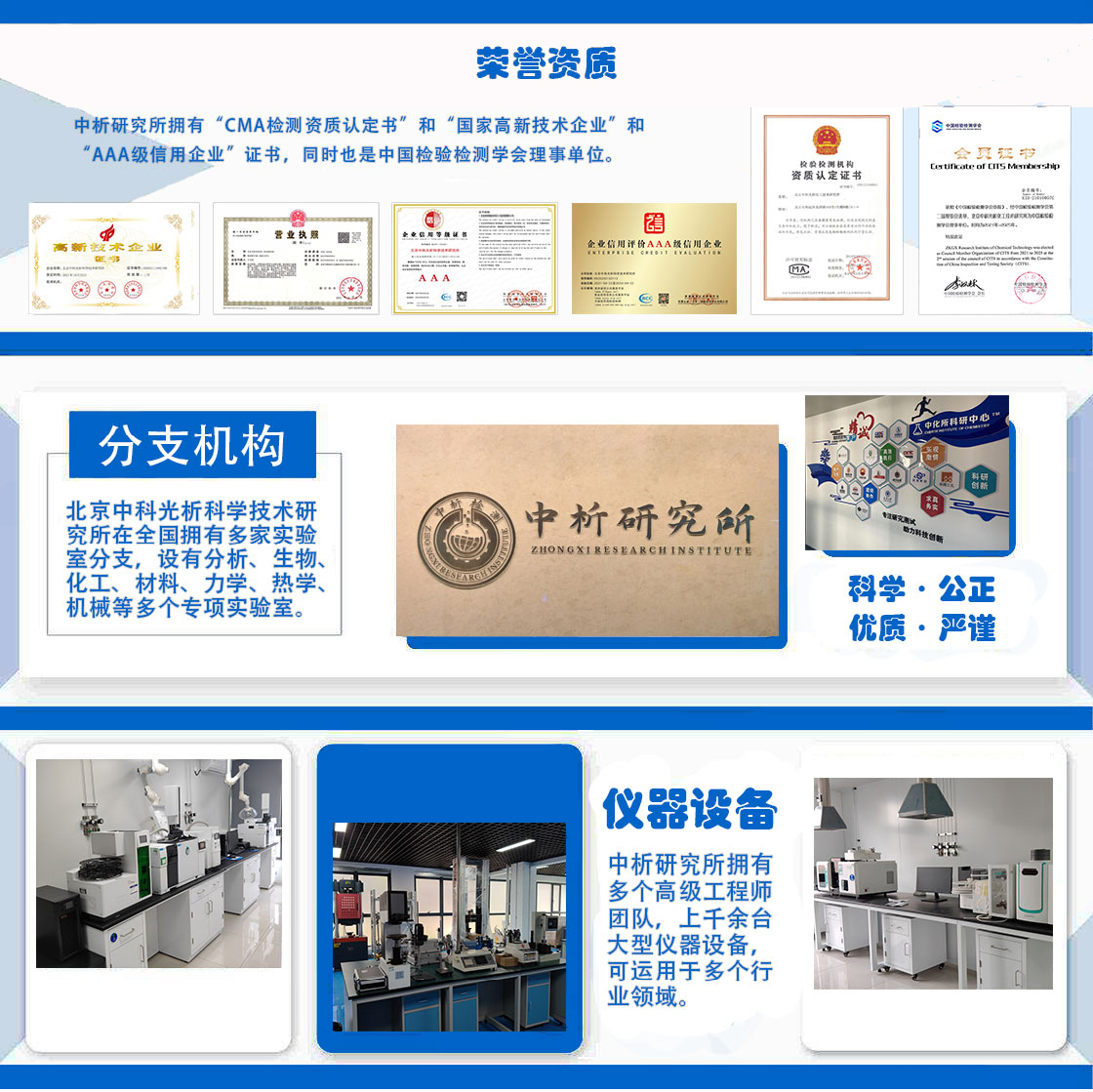
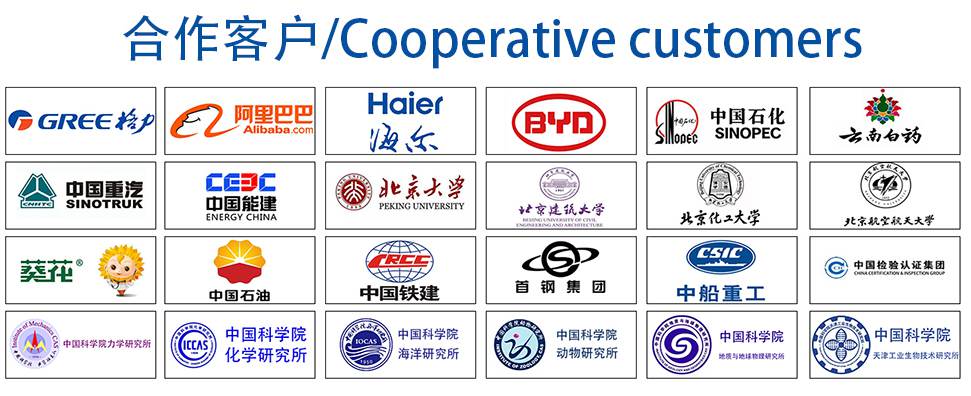