机车车辆用橡胶弹性元件检测的重要性与主要内容
橡胶弹性元件是机车车辆悬挂系统、减震装置及连接部件中的关键组件,其性能直接影响车辆的运行稳定性、乘坐舒适性和安全性。随着铁路运输高速化、重载化的发展,橡胶元件需承受更复杂的动态载荷和环境条件,因此对其物理性能、耐久性和可靠性提出了更高要求。为确保橡胶弹性元件的质量符合行业标准,需通过系统的检测项目进行全方位评估,涵盖材料特性、力学性能、环境适应性等多个维度。
检测项目分类及技术要求
针对机车车辆用橡胶弹性元件,常见的检测项目主要包括以下几类:
1. 物理性能检测
物理性能是评估橡胶元件基础质量的核心指标,包括硬度、拉伸强度、断裂伸长率、压缩永久变形等参数的测试。例如,通过邵氏硬度计测量橡胶硬度,确保其在设计范围内;利用万能试验机进行拉伸试验,验证材料在极端负载下的抗拉性能。
2. 化学性能分析
通过热重分析(TGA)、差示扫描量热法(DSC)等方法,检测橡胶材料的耐老化性、耐油性及耐化学腐蚀性。重点验证元件在长期接触油脂、酸碱介质或臭氧环境下的性能稳定性,避免因材料降解导致功能失效。
3. 环境适应性测试
模拟实际工况中的极端温度、湿度及振动条件,开展高低温循环试验、湿热老化试验及动态刚度测试。例如,在-50℃至+120℃温度范围内评估橡胶的弹性恢复能力,或通过盐雾试验验证其在沿海地区的耐腐蚀性。
4. 疲劳寿命评估
采用高频疲劳试验机对橡胶元件进行数百万次动态加载,模拟长期运行中的往复受力状态。通过监测裂纹扩展速度和刚度衰减率,预测元件的使用寿命,确保其在设计周期内不发生结构性破坏。
5. 尺寸与装配精度检测
利用三维扫描仪或激光测量设备,校验橡胶制品的几何尺寸、表面平整度及安装接口匹配性,避免因尺寸偏差导致装配应力集中或密封失效问题。
6. 动态特性验证
通过动态机械分析(DMA)测试橡胶的阻尼系数、动态模量等参数,结合有限元仿真技术优化元件设计,确保其在不同频率载荷下的减震效果满足车辆运行需求。
检测标准的应用与发展
目前,国内机车车辆用橡胶弹性元件的检测主要依据TB/T 2843《机车车辆橡胶弹性元件通用技术条件》、ISO 4637国际标准等规范。随着新型复合材料应用和智能化检测技术的引入,检测项目正逐步向实时监测、无损检测方向延伸,以提高质量控制效率和可靠性。
通过上述系统性检测,可全面评估橡胶弹性元件的性能边界与失效模式,为机车车辆的安全运营提供关键技术支持,同时推动材料研发与生产工艺的持续优化。
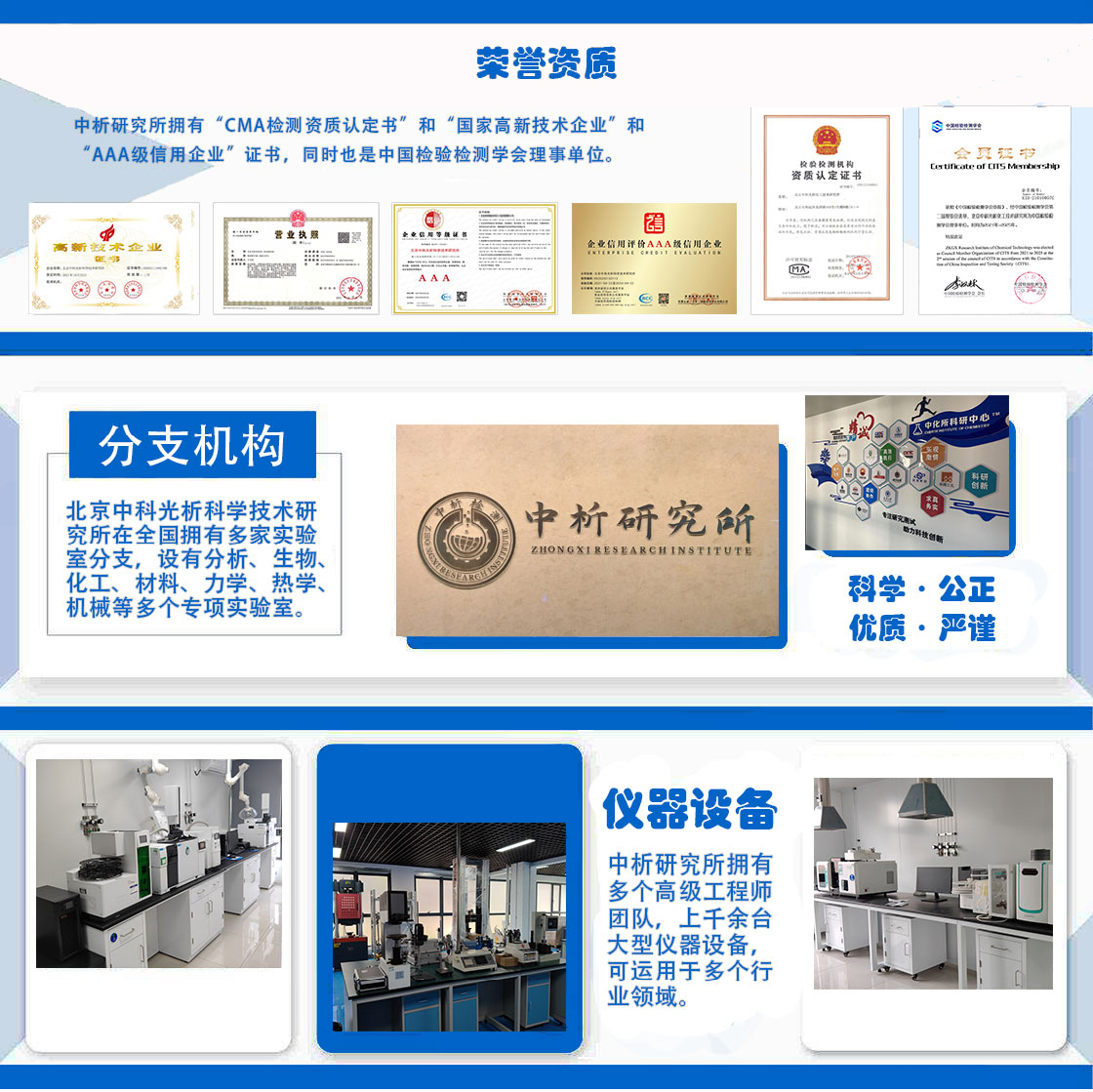
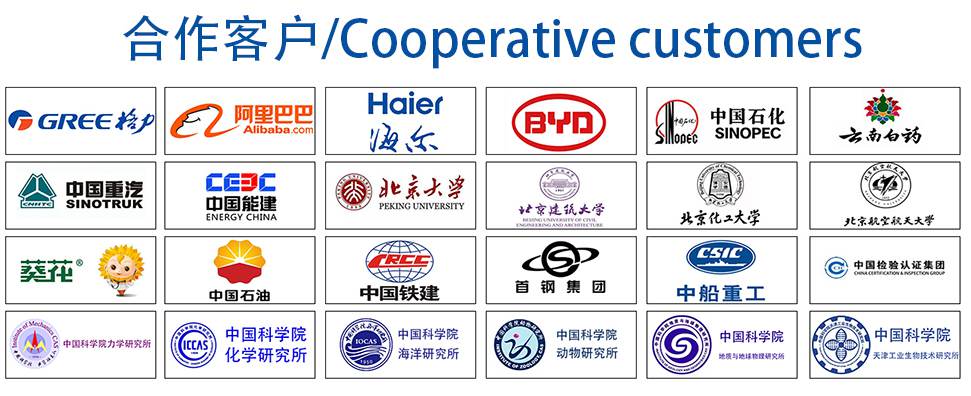