机械伤检测:关键技术与行业应用
机械伤检测是工业制造、设备维护和产品质量控制中的核心环节。它通过系统化的技术手段识别材料或零部件表面及内部的物理损伤,例如划痕、裂纹、变形、磨损等,以预防因机械缺陷引发的安全隐患或功能失效。随着现代工业对精度和可靠性要求的提升,机械伤检测技术已从传统目视检查发展为涵盖光学成像、无损检测、智能算法等多学科融合的综合性检测体系。尤其在航空航天、汽车制造、精密仪器等高端领域,检测精度需达到微米甚至纳米级,这对检测项目的科学设计和技术实现提出了更高要求。
一、机械伤检测的主要项目分类
1. 表面损伤检测:包括划痕、凹坑、锈蚀等表观缺陷的识别。采用高分辨率工业相机配合环形光源进行图像采集,结合边缘检测算法实现损伤量化分析。部分场景会使用3D轮廓仪获取损伤深度数据。
2. 内部缺陷检测:针对材料内部的裂纹、气孔等隐蔽缺陷,常用超声波探伤(UT)、X射线成像(DR/CT)等技术。其中相控阵超声波可生成三维缺陷模型,检测精度可达0.1mm级。
3. 结构变形检测:通过激光扫描或数字图像相关法(DIC)测量工件形变,适用于冲压件回弹分析、装配应力检测等场景,精度通常优于0.01mm。
二、前沿检测技术的应用突破
1. 多光谱成像技术:利用不同波段光波的反射特性差异,可区分机械损伤与表面污染物,在铝合金轮毂检测中已实现98%以上的识别准确率。
2. 深度学习算法:基于卷积神经网络(CNN)的自动缺陷分类系统,经过百万级样本训练后,对复杂背景下的微小裂纹检测速度比人工快20倍以上。
3. 工业CT断层扫描:通过X射线三维重建技术,可非破坏性检测涡轮叶片内部孔隙率,检测分辨率达到2μm,有效避免传统切片检测造成的样品损耗。
三、行业质量控制标准与流程优化
在汽车制造领域,依据IATF16949标准要求,关键零部件的机械伤检测需建立SPC统计过程控制体系。某变速箱齿轮生产线通过引入在线视觉检测系统,将漏检率从1.2%降至0.05%,同时生成数字化检测报告用于工艺追溯。
航空航天领域则严格执行NAS410/EN4179标准,采用TOFD超声波检测技术对航空发动机叶片进行全生命周期监控,结合大数据分析预测剩余使用寿命,使维护成本降低37%。
四、技术挑战与发展趋势
当前行业正着力突破多模态数据融合、微小缺陷定量评价等关键技术瓶颈。德国某研究所开发的太赫兹成像系统,已实现复合材料分层缺陷的亚表面检测。未来,随着5G通信和数字孪生技术的普及,机械伤检测将向智能化、云端化方向发展,形成覆盖设计、生产、运维的全链条质量保障体系。
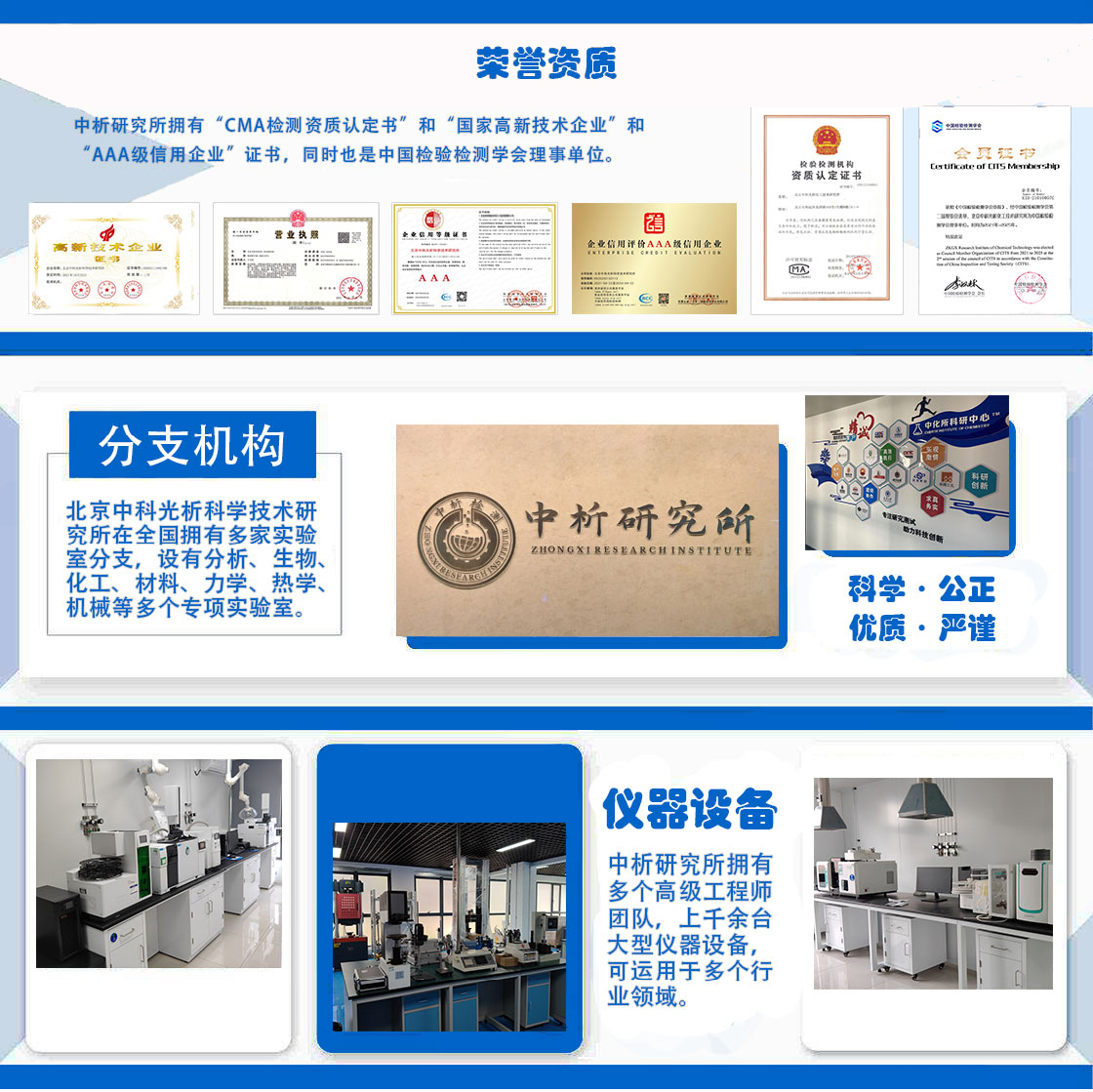
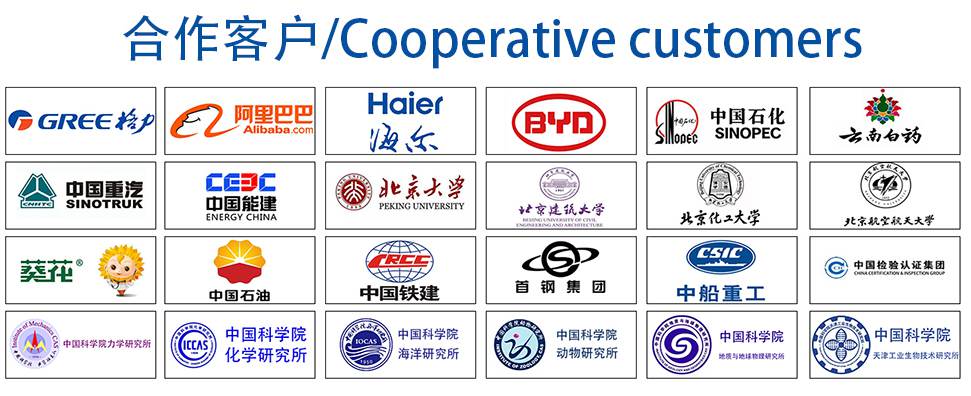