直径检测技术与方法解析
直径检测作为机械制造、精密加工、汽车工业等领域中的基础性质量检测环节,其精度直接影响产品的装配性能和最终使用效果。随着智能制造的发展,直径测量已从传统的手工卡具检测发展为集合光学、激光、计算机视觉等多技术融合的自动化检测体系。本文将从接触式与非接触式两大类别,系统梳理各类直径检测方法的原理、适用场景及技术特点。
一、接触式直径检测方法
1. 机械量具检测:采用游标卡尺、千分尺等传统工具进行点对点测量,适用于小批量产品抽检。其测量精度可达0.01mm,但存在人为读数误差风险,需配合标准量块定期校准。
2. 气动量仪检测:通过测量气流压力变化推算孔径尺寸,特别适用于深孔、盲孔等难以接触的孔径测量。该方法检测速度可达每分钟120件,但对表面粗糙度有严格要求。
二、非接触式检测技术
1. 激光扫描测量:采用激光三角测量原理,通过高速旋转的激光探头获取物体轮廓数据。如基恩士LJ-X8000系列可实现±0.3μm的重复精度,适用于轴承滚子、精密轴类零件的高速在线检测。
2. 机器视觉检测:搭配高分辨率工业相机与图像处理算法,可同步获取多个直径参数。德国ISRA VISION系统可实现每分钟600件的检测速度,并能自动生成SPC统计分析报告。
3. 超声波测量:利用声波反射原理,特别适用于橡胶管材、软质材料的直径检测。美国Olympus超声波测厚仪可在-20℃至50℃工况下保持0.02mm测量精度。
三、智能检测系统发展趋势
当前直径检测正向多传感器融合方向发展:采用接触式探针+激光位移计的组合测量方案,既能保证基准面的精确定位,又可实现复杂轮廓的快速扫描。如海克斯康Optiv系列复合式测量机,通过智能算法自动补偿温度形变,在航天发动机叶片检测中可将综合误差控制在0.8μm以内。
四、检测方案选择要点
选择直径检测方法需综合考量四大要素:①被测件材质(金属/非金属)②批量规模(单件/批量)③精度要求(IT5-IT13)④检测环境(实验室/车间)。建议针对高精度小批量零件采用三坐标测量,大批量生产线上优先配置视觉检测系统,而对柔性材料则推荐使用超声波检测方案。
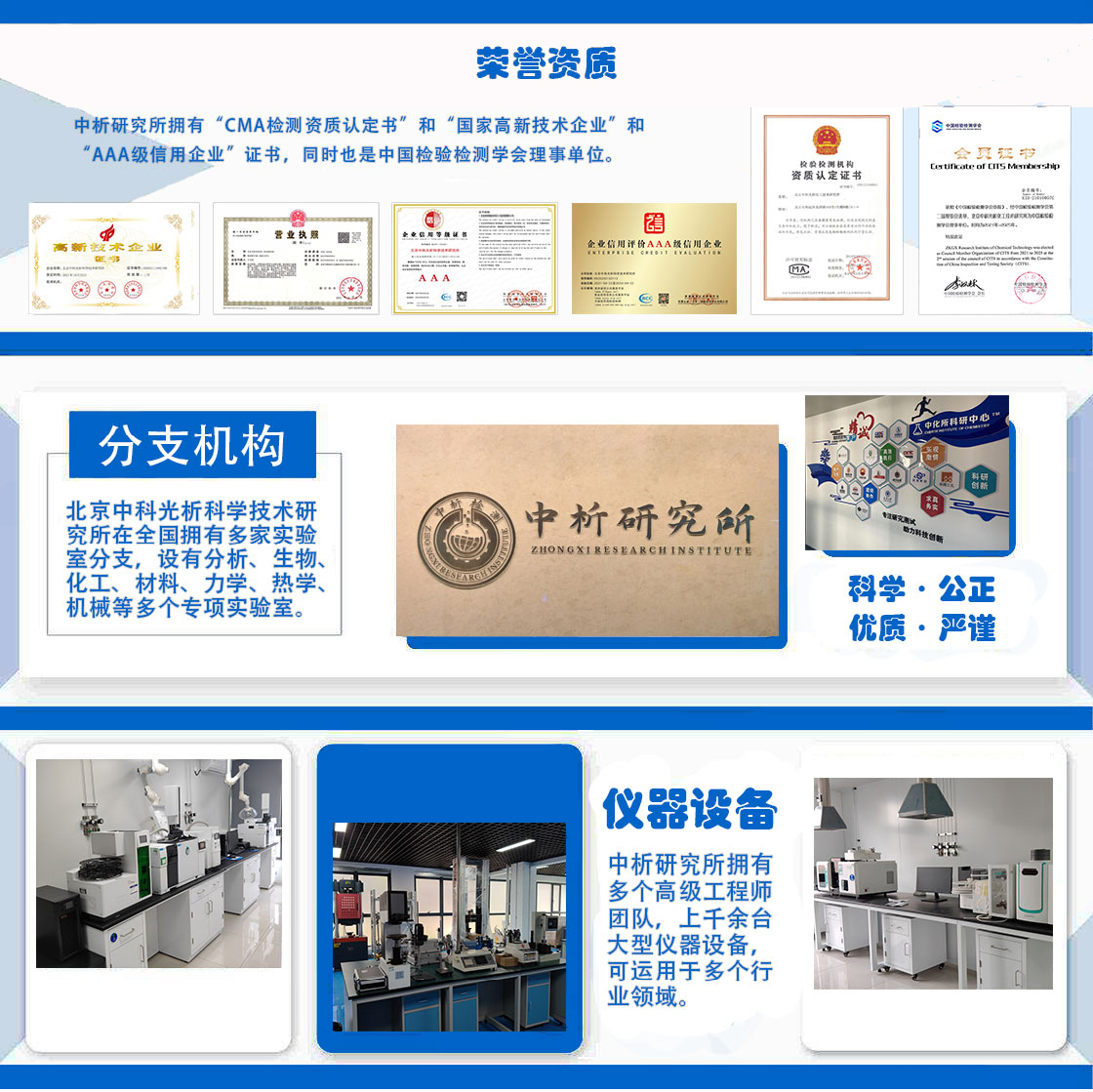
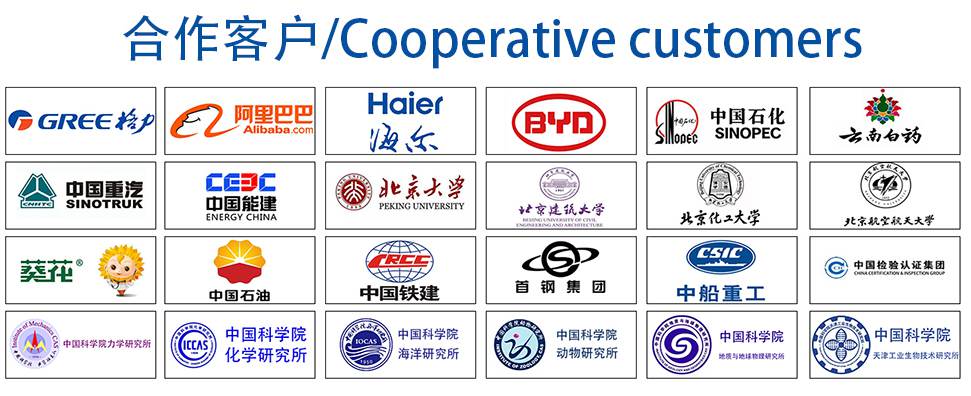