压力变送器检测的重要性
压力变送器作为工业自动化系统中的核心仪表,广泛应用于石油、化工、电力、制药等领域,其性能直接关系到生产安全与过程控制的精准性。长期运行中,压力变送器可能因介质腐蚀、机械磨损、温度波动等因素导致测量误差,甚至失效。因此,定期开展压力变送器检测是保障设备可靠性和工艺稳定性的必要措施。检测工作需依据国家标准(如GB/T 17614)或行业规范,通过专业设备和技术手段全面评估其性能指标。
压力变送器检测的核心项目
1. 静态性能检测
通过压力标准器施加不同压力值,检测变送器的零点漂移、量程误差、线性度、重复性和回程误差。需在恒定温度下进行多次加压-卸压循环,分析输出信号与理论值的偏差是否在允许范围内(通常≤±0.5%FS)。
2. 动态响应测试
模拟实际工况的快速压力变化,使用阶跃压力发生器或正弦压力源,检测变送器的响应时间、频率特性及阻尼系数。此项目尤其适用于需要实时监测压力波动的场景,如液压系统或爆炸性环境。
3. 环境适应性检测
包括温度影响试验(-40℃~85℃)、湿度测试(95%RH)、振动试验(5Hz~2000Hz)和电磁兼容性(EMC)测试,验证变送器在极端条件下的稳定性。例如,高温可能导致密封材料老化,而电磁干扰可能影响信号传输精度。
4. 密封性与耐压检测
对压力接口进行1.5倍额定压力保压测试,持续15分钟无泄漏。同时需验证过载保护能力(通常为额定压力2~3倍),确保设备在异常高压下不发生结构性损坏。
5. 电气安全检测
检查绝缘电阻(≥100MΩ@500VDC)、耐压强度(1500VAC/1分钟无击穿)及接地连续性,防止漏电风险。本安型变送器还需额外评估火花试验和温度组别。
6. 零点和量程校准
使用HART手操器或专用软件对4-20mA输出信号进行标定,确保零点(4mA)对应最低压力值,满量程(20mA)对应最高压力值。校准后需进行三点验证(0%、50%、100%量程)。
7. 外观与结构检查
目视检测外壳防护等级(IP65/IP67)、接液部件腐蚀状况、电缆接头密封性及铭牌信息完整性,排除机械损伤导致的潜在故障。
检测流程与周期建议
常规检测周期为1年/次,高风险领域(如炼化装置)应缩短至6个月。检测流程包括:预处理(清洁、消磁)→功能测试→性能校准→环境模拟→数据记录→出具报告。对于检测不合格的变送器,需根据偏差类型选择调整、维修或更换方案。
结语
通过系统化的压力变送器检测,企业可有效规避因仪表失效引发的生产事故,同时延长设备使用寿命。建议结合设备运行日志和历史检测数据,建立预测性维护模型,进一步提升检测效率与经济效益。
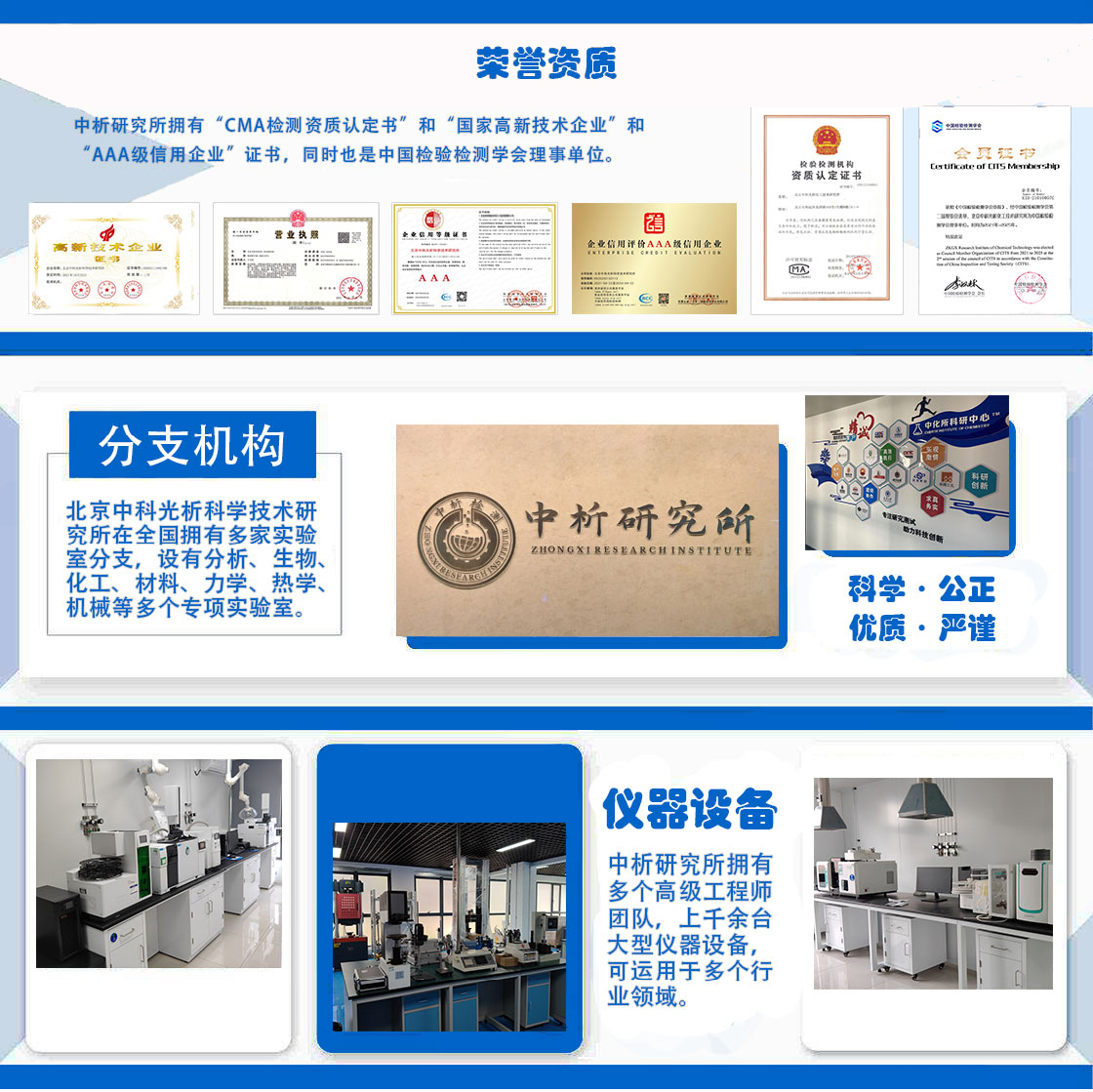
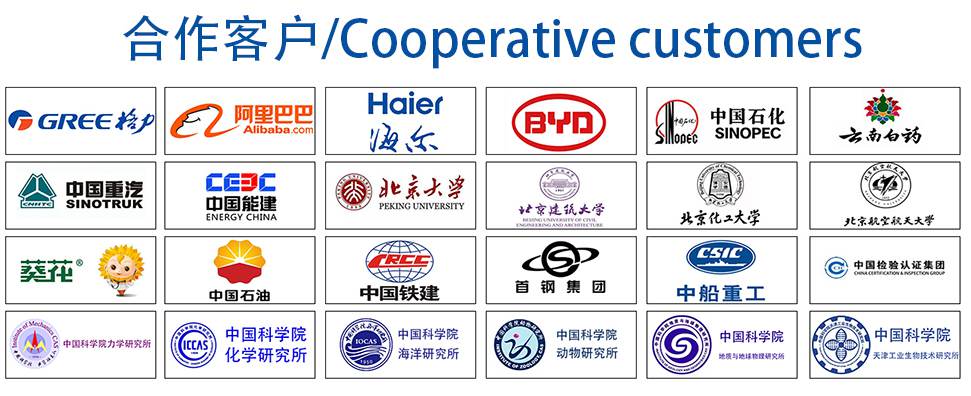