载荷布置标识与系固点检测的重要性
在物流运输、航空航天、工程机械及特种设备领域,载荷布置标识与系固点的安全性直接关系到人员、货物及设备的整体安全。这类检测的核心目标是确保载重分布符合设计要求,系固装置能够有效固定载荷,防止因振动、冲击或意外偏移导致的失效风险。随着行业标准的严格化和智能化检测技术的发展,此类检测已成为质量控制和安全管理中不可或缺的环节。
载荷布置标识通常以图形、文字或编码形式标注于设备表面,明确指示允许的载荷范围、固定点位置及配重要求;而系固点则是设备或运输工具上用于固定绳索、链条或绑带的物理结构。二者共同构成载荷管理的关键要素,其检测需结合静态强度验证、动态工况模拟和耐久性分析,确保全生命周期内的可靠性。
检测项目的核心内容
1. 标识完整性检测:检查标识的清晰度、耐久性及抗环境干扰能力,包括紫外线褪色测试、化学腐蚀耐受性验证及机械磨损试验。不符合标准的标识可能导致操作误判,进而引发安全事故。
2. 系固点几何定位精度:通过三维坐标测量仪或激光扫描技术,验证系固点的实际位置与设计图纸的偏差是否在允许范围内(通常≤±5mm)。偏差过大会改变载荷分布,影响力学性能。
3. 材料力学性能测试:对系固点所用金属材料进行抗拉强度、疲劳强度及延展性检测,重点关注焊接部位的金相组织分析和无损探伤(如超声波检测)。
4. 动态载荷模拟试验:在振动台上模拟运输过程中可能遇到的颠簸、急刹等工况,持续监测系固点的应力分布和形变量,要求最大变形量不超过初始尺寸的0.3%。
检测方法的技术演进
传统检测依赖目视检查与手动测量,存在效率低、主观性强等问题。当前主流检测已转向智能化方向:采用计算机视觉技术自动识别标识完整性,利用有限元分析(FEA)预判系固点薄弱位置,并引入物联网传感器实时监控实际使用中的载荷状态。
例如,某航空货运公司通过部署RFID电子标签与应变片传感器网络,实现了对货舱系固点的全时监控,系统可自动预警超过80%设计载荷的异常工况,将事故率降低62%。
常见问题与改进建议
检测中常发现系固点边缘出现应力集中裂纹、标识油墨耐候性不足等问题。建议采取以下措施:采用梯度热处理工艺优化金属件内部应力分布;标识制作改用纳米级防腐蚀涂层;建立基于大数据的预测性维护模型,提前识别潜在风险点。
根据ISO 1496-2:2018和GB/T 5338-2022标准要求,所有检测数据需形成可追溯的数字化档案,为全行业建立统一的安全评估体系提供基础支撑。
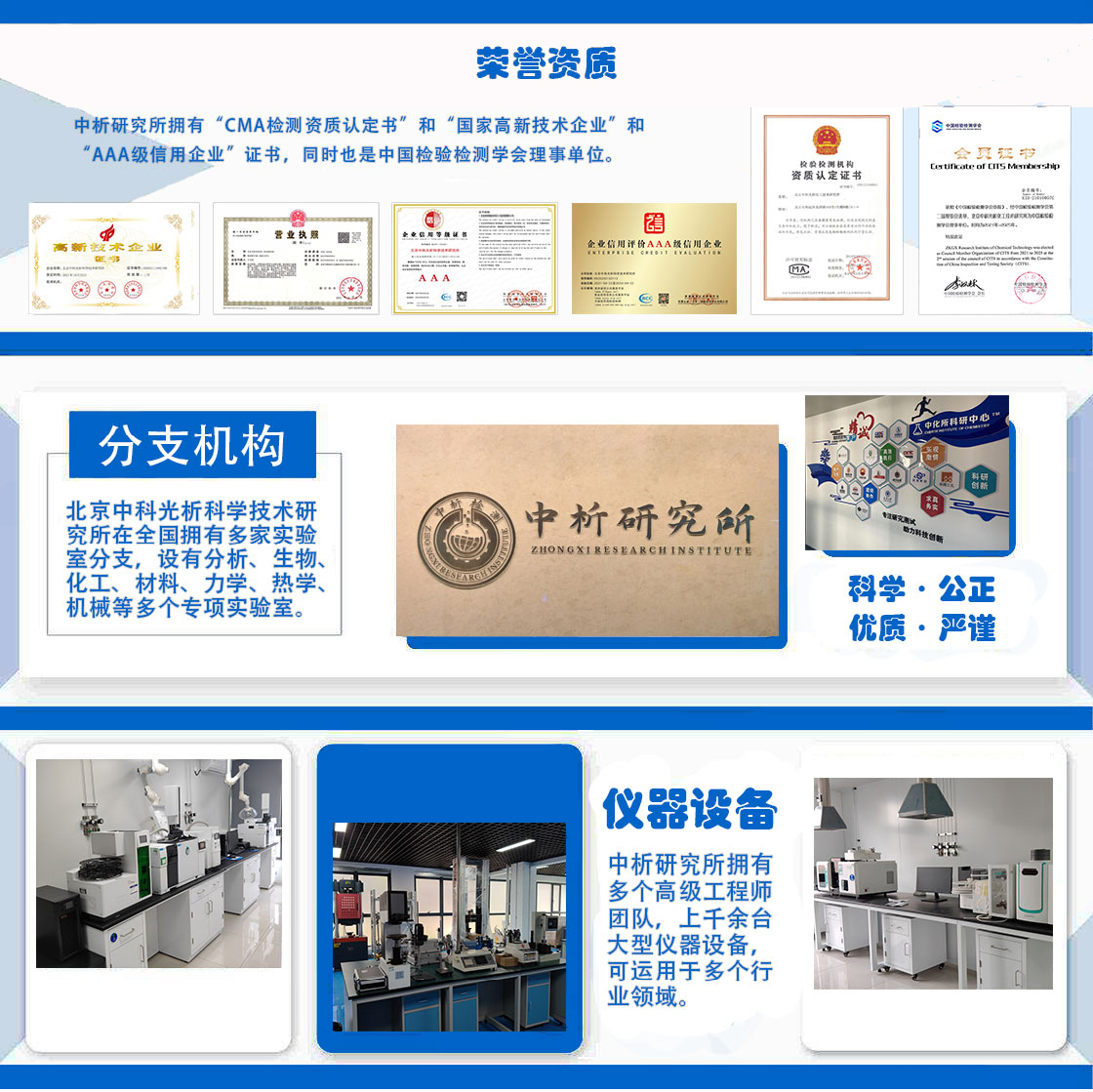
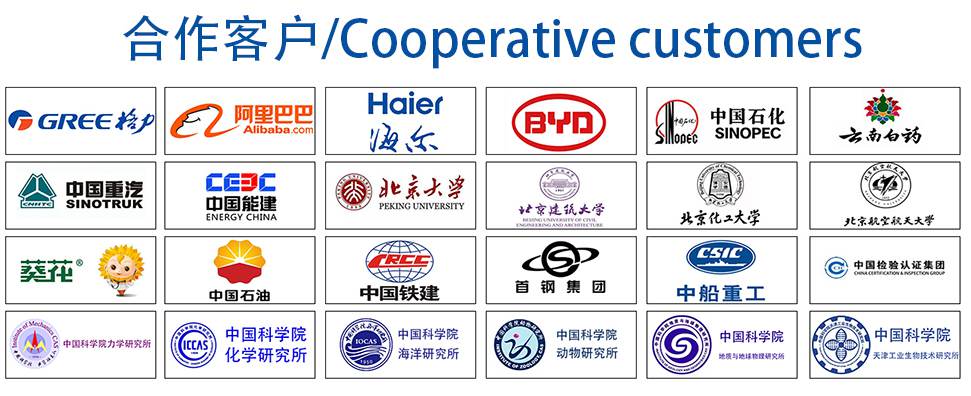