弹簧直接载荷式安全阀检测的重要性
弹簧直接载荷式安全阀作为压力容器、锅炉、管道等承压设备的关键安全附件,其性能直接关系到设备的安全运行和人员生命财产安全。该类型安全阀通过弹簧预紧力与介质压力的平衡实现启闭功能,长期使用中可能因弹簧疲劳、密封面磨损、异物卡阻等问题导致失效。定期开展检测工作,可有效验证其动作可靠性、密封性能及排放能力,确保符合TSG 21-2016《固定式压力容器安全技术监察规程》、GB/T 12241《安全阀一般要求》等标准要求,避免因安全阀故障引发的超压事故。
关键检测项目及技术要求
1. 外观与结构检查
使用目视检测和量具对阀体、阀座、阀瓣、弹簧等部件进行外观检查,要求无裂纹、腐蚀、变形等缺陷;核对铭牌信息(型号、整定压力、制造许可证号)是否完整清晰;检查弹簧自由高度、同心度是否符合设计要求,弹簧表面应无锈蚀或永久变形。
2. 密封性能试验
采用液压或气压试验方法,在90%整定压力下保压3分钟,观察泄漏情况。根据GB/T 12243标准,允许泄漏率应≤20气泡/min(液体介质)或通过听音法判定无持续泄漏(气体介质)。密封面粗糙度需达到Ra0.8μm以下,接触宽度不小于阀座密封面宽度的80%。
3. 整定压力校验
使用专用校验台进行压力整定测试,重复三次取平均值。允许偏差为±3%整定压力(当整定压力≤0.5MPa时允许±0.015MPa)。测试过程中需记录开启高度、回座压力等参数,回座压力与整定压力比值应≥80%。
4. 弹簧性能测试
通过弹簧试验机测量弹簧刚度系数,允许偏差不超过设计值的±10%;检测残余变形量(加载至1.5倍工作载荷后,永久变形量应<0.5%自由高度);进行疲劳寿命测试(≥50000次循环无断裂或刚度衰减)。
5. 排放与复位性能验证
全量程排放试验时,安全阀应在达到额定排放压力后稳定开启,排放系数不低于0.9;测试后阀瓣应自动回座至密封状态,无卡滞现象。需特别注意高温、低温等极端工况下的动作特性验证。
6. 材料理化分析
对关键部件进行材质复核,包括光谱分析(验证材料牌号)、硬度测试(弹簧HRC44-52,阀瓣HB180-250)、金相组织检查(无脱碳、过热等异常)。密封面堆焊层厚度应≥3mm,结合强度需通过超声波检测验证。
检测周期与数据管理
根据TSG规范要求,安全阀应每年至少进行一次在线校验,每3年进行解体检测。所有检测数据需完整记录,建立数字化档案,异常情况应进行失效分析并制定改进方案,确保设备全生命周期的可追溯性。
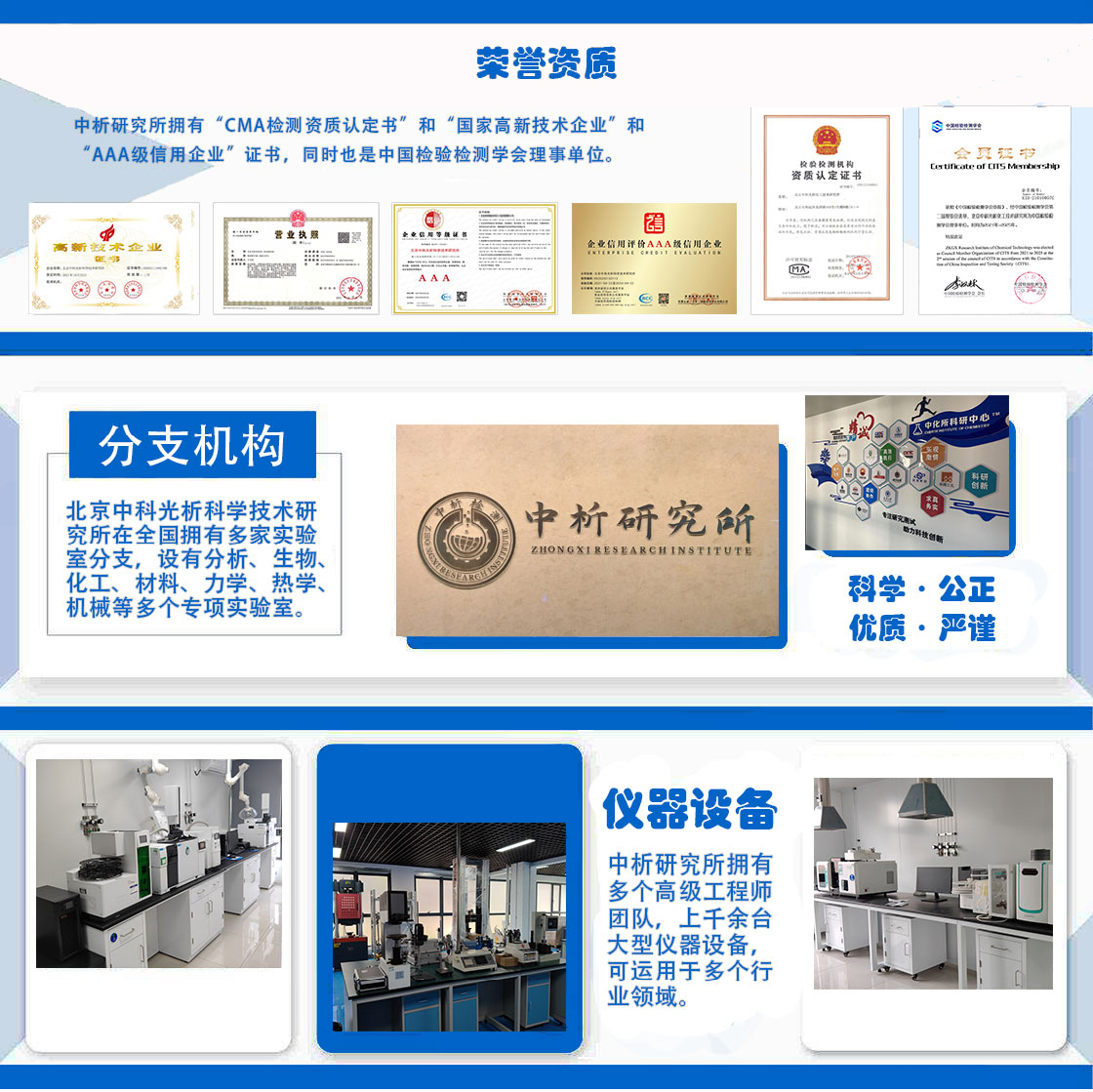
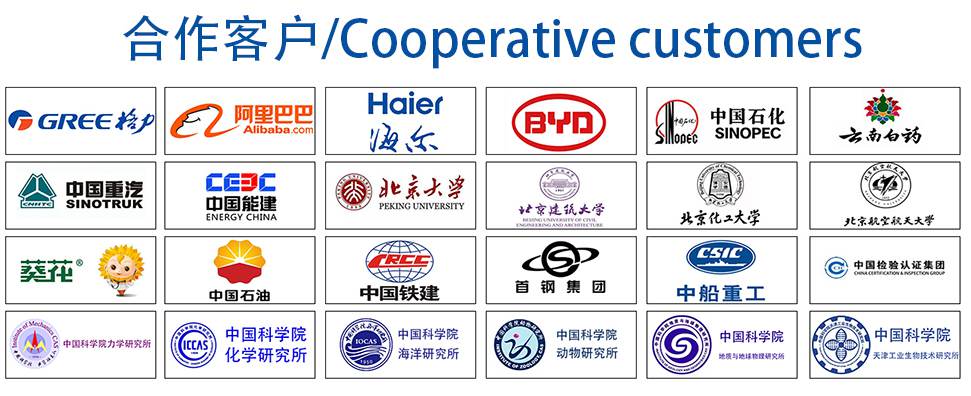