散热器检测的重要性与核心内容
散热器作为电子设备、汽车引擎、工业机械等领域的关键部件,其性能直接影响系统运行的稳定性和使用寿命。随着电子元器件功率密度的提升以及工业设备的高负荷需求,散热器的检测已成为保障设备安全的重要环节。专业的散热器检测能够有效发现材质缺陷、结构设计问题或工艺瑕疵,从而避免因散热不良导致的设备过热、效率下降甚至损毁等风险。
散热器检测的核心项目
1. 外观与尺寸检测
通过光学测量仪、三维扫描仪等设备,检测散热器表面是否存在划痕、变形、氧化等缺陷,并验证翅片间距、基板厚度等关键尺寸是否符合设计标准。例如,汽车散热器的翅片间距误差需控制在±0.1mm以内,避免影响风道效率。
2. 材料性能分析
使用光谱分析仪检测铝合金/铜材质的成分比例,确保导热系数达标(6063铝合金需≥200W/m·K)。同时通过金相显微镜观察金属晶粒结构,评估材料抗腐蚀性和机械强度。近年新增的盐雾试验可模拟极端环境下的耐蚀表现。
3. 散热性能测试
在恒温箱中模拟工作环境,利用红外热像仪监测散热器表面温度分布,结合风洞设备测量散热效率(W/℃)。高端检测还会采用流体仿真软件验证散热通道设计的合理性,确保热量能均匀扩散。
4. 密封性与耐压测试
针对液冷散热器,需进行30分钟保压试验(通常为工作压力的1.5倍),并使用氦质谱检漏仪检测微泄漏。汽车散热器要求泄漏率低于1×10⁻⁷ mbar·L/s,防止冷却液渗漏引发系统故障。
5. 振动与耐久性评估
通过电磁振动台模拟设备运行时的机械振动(频率5-2000Hz,加速度10g),检测翅片焊接强度与整体结构稳定性。部分工业散热器需连续运行2000小时以上,验证长期工况下的性能衰减情况。
检测标准与技术发展
目前主要依据GB/T 15318-2019《散热器通用技术条件》、ISO 16750-3汽车电子环境试验标准等规范。随着AI技术的应用,部分检测机构已引入机器学习算法,通过历史数据预测散热器寿命,并实现检测结果的智能判定,将传统检测效率提升40%以上。
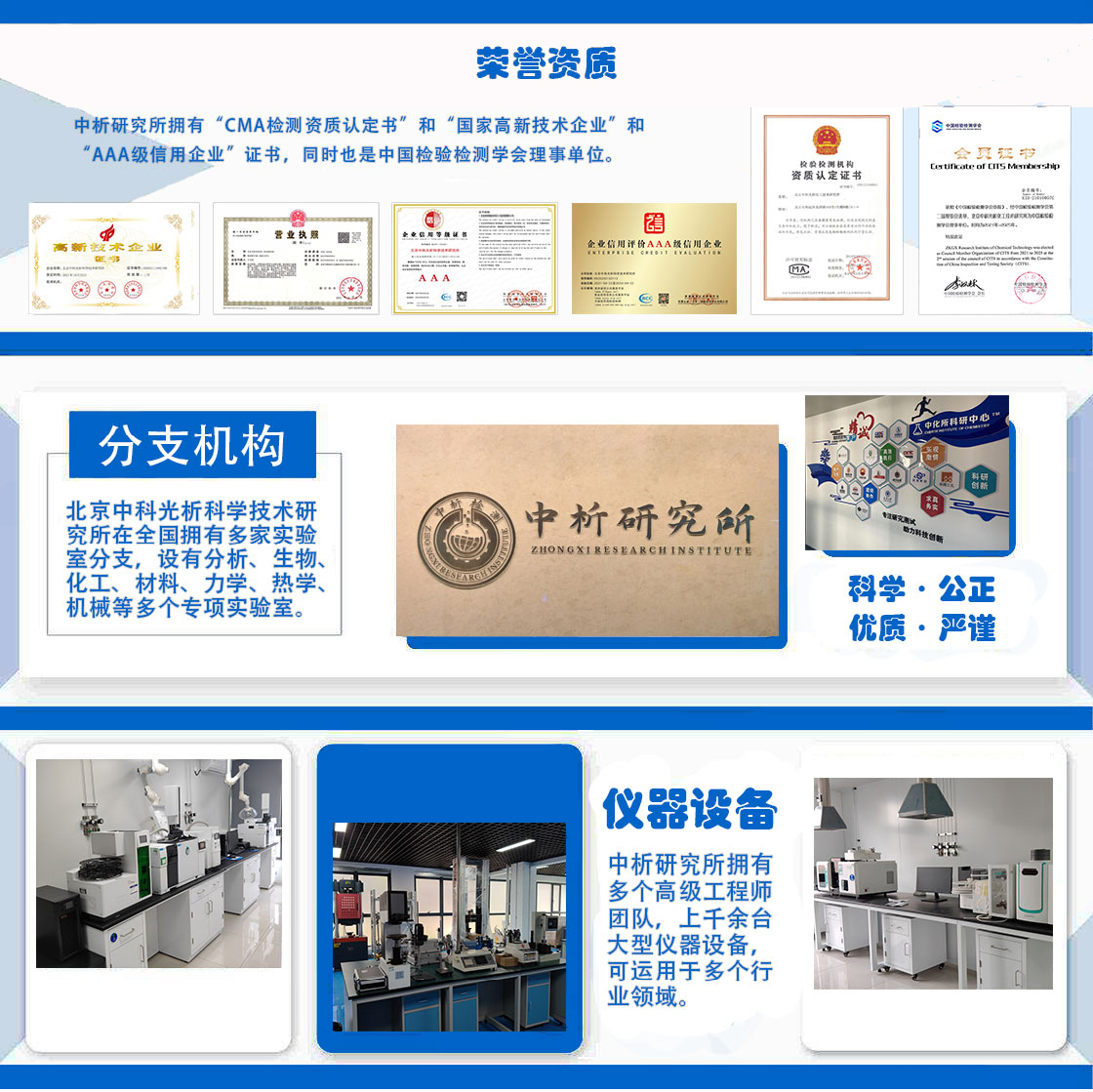
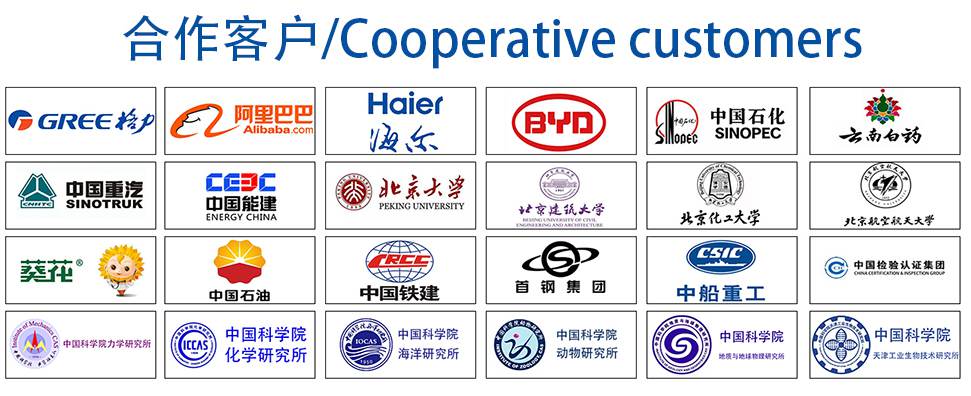