环氧涂层钢筋检测的重要性及检测项目解析
环氧涂层钢筋作为现代建筑工程中重要的防腐材料,广泛应用于跨海大桥、海洋平台、盐碱地区基础设施等腐蚀性环境中。其通过表面熔融环氧粉末涂层隔绝钢筋与腐蚀介质的接触,显著延长结构寿命。然而,涂层质量直接影响防护效果,因此在生产、运输及施工过程中必须进行系统性检测。本文围绕环氧涂层钢筋的核心检测项目展开分析,为工程质量控制提供科学依据。
一、涂层厚度检测
涂层厚度是评判防腐性能的首要指标,依据ASTM A775/A775M或GB/T 25826标准,采用磁性测厚仪进行多点测量。检测时需避开钢筋螺纹区域,取10个以上测量点计算平均厚度,要求最小局部厚度≥130μm,同一截面厚度差不超过50μm。异常薄区可能成为腐蚀突破口,需进行修补或剔除。
二、涂层附着力测试
采用划格法(ASTM D6677)或拉开法(ISO 4624)评估涂层与基体的结合强度。划格法通过专用刀具在涂层表面制作1mm×1mm网格,使用胶带撕拉后观察脱落情况;拉开法则通过液压设备测量剥离强度,要求附着力≥5MPa。该检测可有效发现涂层固化不良或表面污染等问题。
三、涂层连续性检查
使用高压电火花检测仪(15-30kV)扫描整个钢筋表面,当涂层存在针孔、裂纹等缺陷时,仪器会发出报警信号。检测需在完全干燥环境下进行,行进速度控制在0.3m/s以内,确保每平方厘米区域都被覆盖。允许缺陷密度≤4个/m²且单个缺陷面积≤25mm²。
四、耐化学腐蚀性测试
通过盐雾试验(ASTM B117)和阴极剥离试验模拟严苛环境:将试样置于5%NaCl雾化环境中1000小时后,涂层应无起泡、开裂现象;阴极剥离试验在1.5V电压下持续28天,剥离半径需≤8mm。该检测验证涂层在长期电化学腐蚀下的稳定性。
五、抗冲击性能检测
采用落锤冲击试验(ASTM D2794),使用1kg锤头从300mm高度自由下落冲击涂层表面。检测后使用10倍放大镜观察,要求冲击区域无肉眼可见裂纹或涂层剥离。该指标反映涂层在运输、施工过程中的抗机械损伤能力。
六、外观质量检验
目视检查涂层颜色均匀性、表面平整度及流挂现象,使用色差仪量化测定ΔE值≤2.0。同时检查涂层边缘覆盖完整性,特别是螺纹根部等易漏涂部位,确保无金属基体外露。优质涂层应呈现光滑、无颗粒粘附的镜面效果。
通过上述系统性检测,可全面评估环氧涂层钢筋的防护性能。建议在原材料进场、施工前及重要节点进行复检,并建立数字化检测档案,为工程全生命周期质量管理提供数据支撑。只有严格把控每个检测环节,才能充分发挥环氧涂层的防腐优势,保障钢筋混凝土结构的百年耐久性。
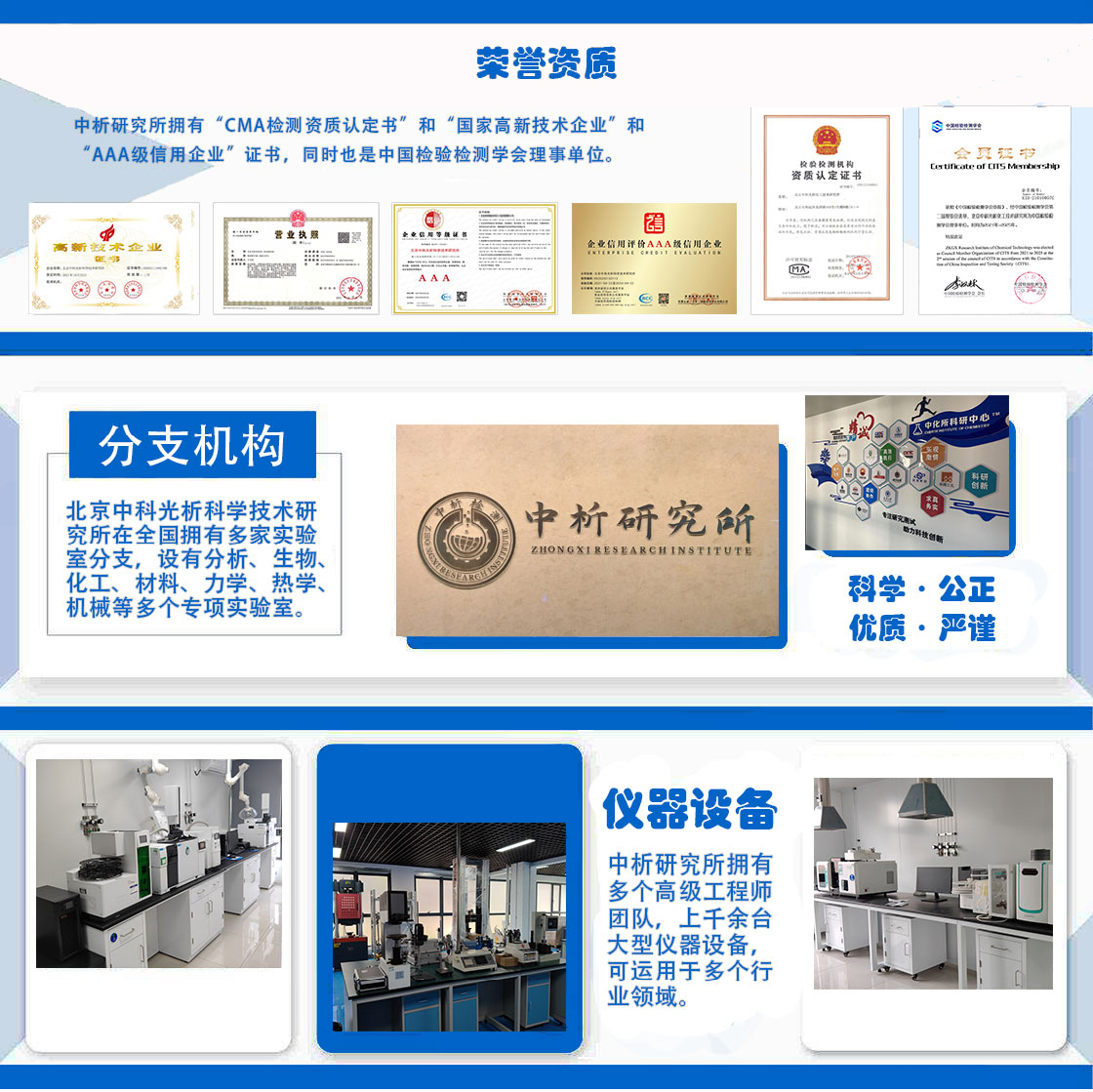
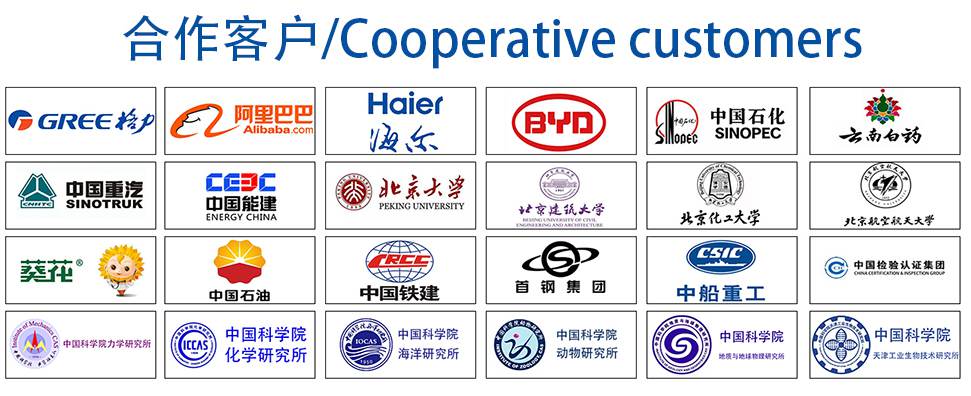